Custom HPPE Protective Gloves in 2025: Complete Guide for Sourcing and Selection
April 12, 2025
Share This Article
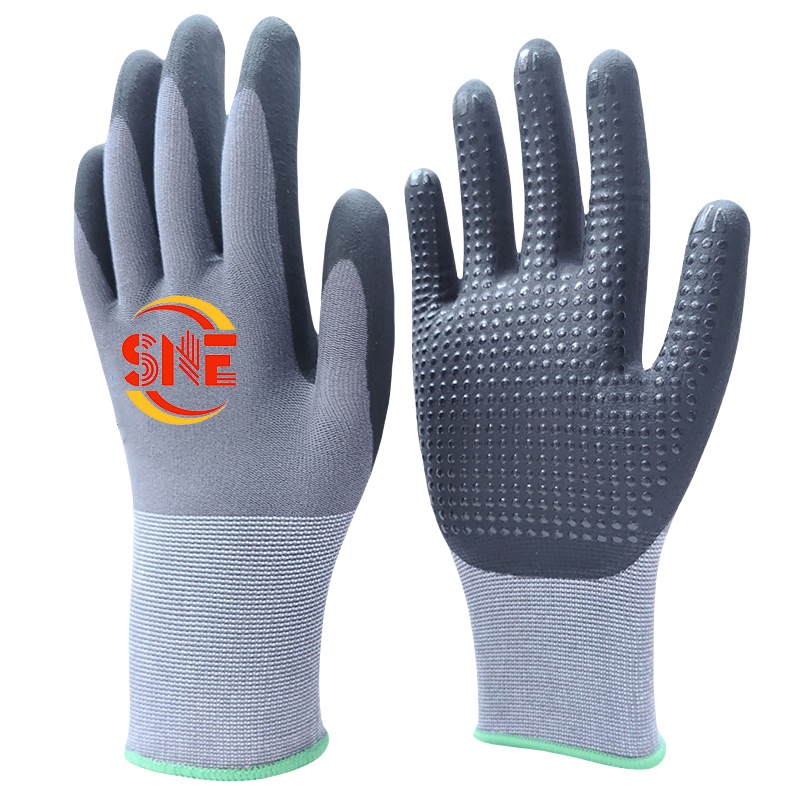
In today’s industrial landscape, hand protection remains one of the most critical aspects of workplace safety. Custom HPPE (High-Performance Polyethylene) protective gloves have emerged as an innovative solution that combines exceptional cut resistance with comfort and dexterity. As we move through 2025, these advanced protective gloves continue to evolve with new manufacturing techniques, innovative designs, and enhanced performance capabilities. Whether you’re a safety manager, procurement specialist, or business owner, understanding the intricacies of custom HPPE gloves can significantly impact your workforce’s safety and operational efficiency.
What Are HPPE Protective Gloves?
HPPE protective gloves represent the cutting edge of hand protection technology in the industrial safety equipment market. HPPE, or High-Performance Polyethylene, is an advanced synthetic fiber known for its remarkable strength-to-weight ratio. Unlike traditional materials such as leather or cotton, HPPE offers superior cut resistance without sacrificing comfort or dexterity, making it an ideal choice for various industrial applications.
The molecular structure of HPPE consists of extremely long polyethylene chains that are highly oriented, resulting in exceptional tensile strength. This unique structure enables HPPE fibers to be incredibly strong while remaining lightweight and flexible. In fact, HPPE is often compared to steel in terms of strength, but it’s significantly lighter and more comfortable to wear throughout a workday.
The development of HPPE gloves marked a significant evolution in personal protective equipment (PPE). Traditional cut-resistant gloves often relied on materials like aramid fibers (such as Kevlar), which, while effective, could be uncomfortable and prone to heat retention. HPPE addresses these limitations by offering superior cut resistance with enhanced comfort properties:
- Exceptional Cut Resistance: HPPE gloves can withstand contact with sharp objects, offering protection against cuts, slashes, and abrasions.
- Moisture Resistance: Unlike some fibers that absorb moisture, HPPE remains effective in wet conditions.
- Chemical Resistance: HPPE demonstrates good resistance to many chemicals, acids, and bases.
- Comfort and Flexibility: The lightweight nature of HPPE allows for greater dexterity and reduces hand fatigue.
- Temperature Performance: HPPE maintains its protective properties across a wide temperature range.
Manufacturing HPPE gloves typically involves blending HPPE fibers with other materials such as nylon, spandex, or fiberglass to enhance specific properties. The core HPPE liner is then often coated with materials like polyurethane (PU), nitrile, or latex to provide grip and additional protection against liquids or oils.
According to Qingdao Snell Protective Products, a leading manufacturer in this field, “The advanced properties of HPPE make it ideal for applications requiring high levels of cut protection without compromising on comfort or dexterity, which is crucial for maintaining productivity in industrial settings.”
How to Choose the Best Custom HPPE Gloves for Your Business?
Selecting the right custom HPPE gloves for your specific business needs requires careful consideration of several key factors. With numerous options available in the market, making an informed decision can significantly impact worker safety, productivity, and your overall PPE budget.
Understanding Cut Resistance Levels
The first step in choosing appropriate HPPE gloves is understanding cut resistance standards. Most safety gloves follow either the ANSI/ISEA 105 standard (used in North America) or the EN 388 standard (used in Europe). These standards provide numerical ratings that indicate the level of cut resistance:
- ANSI/ISEA 105: Uses an A1-A9 scale, with A9 offering the highest cut resistance
- EN 388: Uses a 1-5 scale (with 5 being the highest) for the older standard, and A-F scale (with F being the highest) for the current standard
Select the appropriate level based on your industry’s hazard assessment. For example, sheet metal handling might require A4/C or higher, while general warehouse work might only need A2/B protection.
Assessing Coating Requirements
HPPE gloves are typically available with various coating options, each suited to different working environments:
- Polyurethane (PU) Coating: Offers excellent grip in dry conditions, high dexterity, and good abrasion resistance. Ideal for precision assembly, electronics, and automotive manufacturing.
- Nitrile Coating: Provides superior oil and grease resistance, making it perfect for automotive, machinery, and oily component handling.
- Latex Coating: Offers excellent grip in wet conditions and good elasticity. Suitable for construction and general handling tasks.
- Sandy Nitrile Coating: Provides enhanced grip in oily conditions through a textured surface.
Considering Ergonomics and Comfort
The most protective glove is ineffective if workers remove it due to discomfort. Consider these comfort aspects:
- Breathability: Look for designs that allow heat and moisture to escape, particularly in warm environments.
- Fit and Sizing: Properly fitted gloves enhance dexterity and reduce hand fatigue. Consider offering a range of sizes to accommodate your workforce.
- Liner Material: Some HPPE gloves incorporate additional materials like spandex for stretch or bamboo fibers for enhanced comfort.
- Flexibility: Test the glove’s flexibility, particularly at the knuckles and between fingers, to ensure it allows natural hand movement.
Evaluating Additional Features for Customization
When ordering custom HPPE gloves, consider these additional features:
- Touchscreen Compatibility: Some HPPE gloves are engineered with conductive materials in the fingertips, allowing workers to operate touchscreen devices without removing gloves.
- Impact Protection: For environments with crushing or impact hazards, consider HPPE gloves with TPR (Thermoplastic Rubber) impact protection on the back of the hand.
- Color Coding: Different colors can help identify glove sizes or designate gloves for specific departments or tasks.
- Custom Branding: Company logos and safety messaging can be added to reinforce safety culture and brand identity.
Testing Before Full Deployment
Before placing a large order for custom HPPE gloves, request samples for field testing. Have workers in different roles test the gloves for:
- Protection effectiveness
- Dexterity and task performance
- Comfort during extended wear
- Durability and wear patterns
“The ideal protective glove balances safety with usability,” explains a safety expert from Qingdao Snell. “Even the highest cut resistance rating is meaningless if the glove hinders work performance or causes enough discomfort that workers remove them during hazardous tasks.”
Where to Buy Custom HPPE Protective Gloves?
Finding reliable sources for high-quality custom HPPE protective gloves requires navigating a complex global supply chain. Understanding your purchasing options can help you secure the best combination of quality, customization, and value.
Direct from Manufacturers
Purchasing directly from manufacturers often provides the best value, especially for large orders. When buying from manufacturers:
Advantages:
- Lower per-unit costs by eliminating middlemen
- Direct communication for customization requirements
- Better quality control and consistency
- Access to the latest product innovations
Considerations:
- Typically higher minimum order quantities (MOQs)
- Longer lead times, especially for custom designs
- May require more effort in relationship management
- International shipping and customs logistics
Qingdao Snell Protective Products Co., Ltd. represents an excellent example of a direct manufacturer option. With over a decade of expertise in protective glove production, Snell offers competitive pricing and factory-direct supply with no middlemen. Their product catalog showcases a wide range of HPPE glove solutions with various coatings and performance specifications.
Industrial Safety Distributors
Industrial safety distributors serve as intermediaries between manufacturers and end-users, offering a range of PPE products including HPPE gloves.
Advantages:
- Lower minimum order quantities
- Faster delivery times, especially for standard products
- Technical expertise and guidance
- Ability to bundle different safety products in one order
Considerations:
- Higher per-unit costs compared to direct manufacturing
- Limited customization options
- May stock products from multiple manufacturers with varying quality
Notable industrial safety distributors include Grainger, Fastenal, MSC Industrial Supply, and Airgas Safety. These companies maintain large inventories of safety products and can often provide next-day delivery for standard items.
Online B2B Marketplaces
Global B2B marketplaces have transformed how businesses source protective equipment, offering access to a wide range of suppliers.
Advantages:
- Easy comparison of multiple suppliers
- Typically lower MOQs than dealing directly with manufacturers
- Buyer protection policies
- User reviews and supplier ratings
Considerations:
- Variable product quality requiring careful supplier vetting
- Shipping times can be unpredictable
- Less direct communication for customization
- Potential language barriers with international suppliers
Popular B2B marketplaces for sourcing HPPE gloves include Alibaba, Global Sources, and Made-in-China.com. When using these platforms, look for suppliers with verified status, third-party certifications, and positive buyer reviews.
Specialized Safety Equipment Retailers
Specialized retailers focus exclusively on safety equipment and PPE, offering expertise and a curated selection.
Advantages:
- Specialized knowledge of safety standards and regulations
- Ability to provide samples before large orders
- Support for compliance documentation
- Often offer fit testing and training
Considerations:
- Higher prices than direct manufacturer options
- May have limited inventory of specialized designs
- Customization may require longer lead times
Examples include Safety Supplies Unlimited, PK Safety, and Northern Safety & Industrial, which provide both online and catalog ordering options.
When selecting your sourcing channel, consider your requirements for order volume, customization, delivery timeline, and budget. For large orders with specific customization needs, direct manufacturers like Qingdao Snell often provide the best combination of quality control, customization options, and value.
HPPE Protective Glove Manufacturers in China
China has emerged as the global manufacturing hub for HPPE protective gloves, offering a combination of advanced manufacturing capabilities, competitive pricing, and extensive customization options. Understanding the Chinese manufacturing landscape can help buyers make informed decisions when sourcing these critical safety products.
Overview of China’s HPPE Glove Manufacturing Industry
China’s protective glove industry has undergone significant transformation over the past decade. From basic manufacturing of low-tech cotton and leather gloves, Chinese manufacturers have invested heavily in advanced materials, manufacturing processes, and quality control systems. Today, Chinese factories produce some of the most technologically advanced HPPE protective gloves available globally.
The industry is primarily concentrated in several manufacturing clusters:
- Shandong Province: Home to numerous specialized glove manufacturers, including industry leaders like Qingdao Snell Protective Products Co., Ltd., which operates advanced production facilities in Gaomi with six production lines dedicated to high-performance protective gloves.
- Zhejiang Province: Known for factories specializing in coated gloves with a focus on export markets.
- Guangdong Province: Features manufacturers with expertise in specialized industrial gloves and innovative materials.
- Jiangsu Province: Hosts factories with advanced automation and quality control systems.
Leading Chinese HPPE Glove Manufacturers
Several Chinese manufacturers stand out for their quality, innovation, and reliability in the HPPE protective glove segment:
Qingdao Snell Protective Products Co., Ltd.
Established in 2024 but building on over a decade of production expertise, Qingdao Snell has quickly become a trusted name in the protective glove industry. The company specializes in manufacturing high-performance HPPE gloves for various industries including automotive, construction, machinery, and logistics.
Key strengths include:
- ISO9001 and CE certifications ensuring consistent quality
- Six production lines across facilities in Gaomi and Nantong
- Competitive pricing through direct factory supply
- Strong customization capabilities for industry-specific requirements
- Comprehensive range of coatings including PU, latex, and nitrile
Snell’s commitment to quality control and innovation has positioned them as a preferred supplier for businesses seeking reliable HPPE gloves with specific customization requirements. Their typical MOQ ranges from 3,000 to 20,000 pieces, making them accessible to medium and large-scale businesses.
Other Notable Chinese Manufacturers
- Shanghai Shenguang Safety Protection Products: Specializes in cut-resistant gloves with advanced coatings and ergonomic designs.
- Anhui Heron Safety Products: Known for innovation in lightweight HPPE blends with enhanced comfort features.
- Xingyu Safety Products Co., Ltd.: Focuses on high-cut-resistance gloves for metal processing and glass industries.
- Zhejiang Dongya Gloves Co., Ltd.: Recognized for high production capacity and consistent quality in export markets.
Advantages of Sourcing from Chinese Manufacturers
Chinese HPPE glove manufacturers offer several distinct advantages:
1. Advanced Manufacturing Technology
Chinese factories have invested significantly in state-of-the-art equipment, including automated knitting machines, precision coating systems, and advanced testing equipment that ensures consistency across large production runs.
2. Material Innovation
Many Chinese manufacturers work closely with material scientists to develop proprietary HPPE blends with enhanced properties, such as improved cut resistance without added weight or better grip in specific working conditions.
3. Vertical Integration
Leading manufacturers like Qingdao Snell maintain control over multiple production stages, from yarn processing to final packaging, ensuring consistent quality and enabling greater customization options.
4. Competitive Pricing
Through economies of scale, efficient production processes, and strategic material sourcing, Chinese manufacturers can offer highly competitive pricing without compromising quality.
5. Extensive Customization Options
Chinese manufacturers are known for their flexibility in accommodating customer-specific requirements, from custom colors and logos to specialized coatings and packaging.
Challenges and Considerations When Sourcing from China
While China offers compelling advantages, buyers should be aware of potential challenges:
1. Quality Variation
Quality can vary significantly between manufacturers. Look for suppliers with recognized certifications (ISO 9001, CE) and established quality control systems.
2. Communication and Language Barriers
Working with manufacturers with English-speaking sales and technical teams can significantly improve the procurement process.
3. Intellectual Property Concerns
When sharing proprietary designs or specifications, work with reputable manufacturers that respect intellectual property rights and are willing to sign confidentiality agreements.
4. Shipping and Logistics
International shipping adds complexity and time to the procurement process. Consider working with manufacturers that have experience with export logistics and can recommend reliable shipping partners.
For businesses seeking the optimal combination of quality, customization, and value, established manufacturers like Qingdao Snell represent excellent partners for sourcing custom HPPE protective gloves. Their commitment to quality control, technical innovation, and customer service has made them a preferred supplier for businesses across various industries requiring high-performance hand protection.
HPPE Protective Glove Manufacturers in the USA
The United States has a strong tradition of manufacturing high-quality personal protective equipment, including HPPE protective gloves. American manufacturers have differentiated themselves through innovation, quality control, and specialized solutions for demanding applications. This section explores the landscape of U.S.-based HPPE glove manufacturing and what sets these producers apart in the global market.
The Evolving Landscape of U.S. Glove Manufacturing
The protective glove manufacturing industry in the United States has undergone significant transformation over recent decades. While many basic glove production operations have moved offshore, U.S. manufacturers have strategically pivoted toward high-value, specialized protective solutions that leverage advanced materials, proprietary technologies, and deep application expertise.
American manufacturers have maintained competitive advantage through:
- Research and development of next-generation materials and designs
- Specialized production techniques for premium market segments
- Rapid prototyping and custom solutions for specific industries
- Strong compliance with stringent regulatory requirements
- Close collaboration with end-users on application-specific designs
Leading American HPPE Glove Manufacturers
Several U.S. manufacturers stand out for their contributions to HPPE glove technology and market leadership:
Ansell Protective Solutions
With manufacturing facilities in North Carolina and R&D centers across the country, Ansell has established itself as a leader in high-performance protective gloves. Their HyFlex® series incorporates advanced HPPE fibers with proprietary coatings developed specifically for precision assembly, automotive manufacturing, and metal fabrication applications.
Hexarmor
Based in Kentucky with additional manufacturing in the Midwest, Hexarmor specializes in premium protective gloves that combine HPPE with their proprietary SuperFabric® technology. Their products are particularly valued in oil and gas, mining, and heavy industry applications where maximum cut and puncture resistance are critical.
West Chester Protective Gear
Operating manufacturing and distribution centers in several U.S. states, West Chester has developed specialized HPPE gloves for industries ranging from food processing to glass handling. Their Iron Clad® series features ergonomic designs optimized for specific work environments and tasks.
Superior Glove Works
While headquartered in Canada, Superior Glove maintains significant manufacturing operations in the United States. Their TenActiv™ line utilizes composite HPPE filament technology developed in their U.S. research facilities to create gloves with exceptional dexterity for critical applications in aerospace, electronics, and precision manufacturing.
Differentiating Factors of U.S. Manufacturers
American HPPE glove manufacturers differentiate themselves through several key factors:
1. Material Science and R&D Focus
U.S. manufacturers invest heavily in research and development, often partnering with universities and material science laboratories to develop proprietary HPPE blends and coating technologies. This results in products with performance characteristics tailored to specific applications and environments.
2. Advanced Testing and Validation
American manufacturers typically employ comprehensive testing protocols that exceed industry standards. This includes specialized testing for specific hazards and application environments, such as testing for fine puncture resistance in medical applications or resistance to specialized chemicals in the energy sector.
3. Ergonomic Design Expertise
U.S. manufacturers have pioneered advances in glove ergonomics, developing anatomically correct designs that reduce hand fatigue and improve dexterity. These designs often incorporate variable knitting patterns, strategically placed padding, and specialized grip enhancements.
4. Integration with Digital Technologies
Leading American manufacturers are at the forefront of integrating digital technologies with traditional PPE. This includes developing HPPE gloves with conductive materials for touchscreen compatibility, RFID tracking for inventory management, and smart sensors for monitoring environmental conditions or worker biometrics.
5. Rapid Customization Capabilities
U.S. manufacturers excel at creating customized solutions for specialized applications with relatively low minimum order quantities compared to overseas options. This includes industry-specific designs, custom sizing options, and application-optimized features.
Market Positioning and Pricing
American-made HPPE protective gloves typically position themselves in the premium market segment, with prices reflecting their advanced features, specialized performance characteristics, and compliance with stringent quality standards. While unit prices are higher than those from international suppliers, many customers find value in:
- Shorter lead times for customized orders
- Reduced compliance risk through documented quality control
- Greater application support and technical guidance
- Simplified logistics with domestic shipping
- Protection of proprietary designs and specifications
For organizations prioritizing maximum protection, specialized performance, or unique design requirements, American manufacturers offer compelling options despite the premium pricing. However, for standard applications where cost-efficiency is paramount, international suppliers like Qingdao Snell may provide better value while still meeting essential performance requirements.
The decision between domestic and international sourcing should be based on a thorough assessment of your specific application requirements, budget constraints, customization needs, and timeline considerations.
HPPE Protective Glove Suppliers in Europe
Europe has a rich tradition of industrial safety equipment manufacturing, with several countries hosting established manufacturers of high-performance protective gloves. European suppliers are particularly noted for their stringent adherence to safety standards, innovative technical solutions, and sustainable manufacturing practices. Understanding the European market is essential for global buyers seeking to diversify their supplier network and access unique technologies.
European Manufacturing Landscape
The European HPPE protective glove market is characterized by a combination of long-established manufacturers and innovative newcomers. The industry is particularly strong in:
- Germany: Known for engineering excellence and meticulous quality control
- France: Recognized for innovative material combinations and ergonomic designs
- United Kingdom: Specialists in application-specific protective solutions
- Poland and Czech Republic: Emerging as cost-competitive manufacturing hubs with strong technical capabilities
- Sweden and Finland: Leading in environmentally sustainable manufacturing processes
European manufacturers typically focus on premium market segments, specializing in high-performance protective gloves for industries with specific requirements such as food processing, pharmaceuticals, automotive manufacturing, and precision engineering.
Leading European HPPE Glove Suppliers
Several European manufacturers have established global reputations for their HPPE protective gloves:
MAPA Professional (France)
With over 70 years of experience in protective glove manufacturing, MAPA has pioneered several innovations in HPPE glove technology. Their Krytech series combines HPPE with other high-performance fibers and proprietary coatings optimized for specific industry applications. MAPA’s strengths include advanced ergonomic designs and specialized solutions for the food industry where cut resistance must be combined with food safety compliance.
Uvex Safety Group (Germany)
Uvex has built its reputation on precision German engineering applied to safety equipment. Their HexArmor and uvex phynomic series feature proprietary HPPE blends developed in their Lüneburg research facility. Uvex distinguishes itself through comprehensive testing protocols that evaluate gloves against specific industry hazards rather than generic standards alone.
ATG (UK/Sri Lanka)
ATG (Allied Technical Group) represents a successful European-Asian manufacturing partnership. Their MaxiCut Ultra series features HPPE composite yarns developed in their European R&D facilities and manufactured in state-of-the-art facilities in Sri Lanka. ATG has pioneered water-based manufacturing processes that eliminate harmful solvents while maintaining high performance standards.
Polyco Healthline (UK)
Specializing in protective gloves for healthcare and controlled environments, Polyco has developed specialized HPPE gloves that combine cut resistance with requirements for clean room compatibility and chemical resistance. Their Matrix and Dyflex ranges feature innovative coating technologies that address multiple hazards simultaneously.
European Regulatory Standards and Certifications
European suppliers adhere to some of the world’s most stringent safety standards, with particular emphasis on:
EN 388:2016 – The European standard for mechanical risks, which evaluates gloves for resistance to abrasion, blade cut, tear, puncture, and ISO 13997 cut. The latest version includes more rigorous testing methods for cut resistance particularly relevant to HPPE gloves.
EN 420 – General requirements for protective gloves, covering ergonomics, construction, innocuousness, cleaning, and comfort.
REACH Compliance – European regulation addressing the production and use of chemical substances and their potential impacts on human health and the environment.
Oeko-Tex Standard 100 – Certification ensuring textiles and fabrics are free from harmful substances.
Many European manufacturers also adhere to additional voluntary standards related to environmental management (ISO 14001) and social responsibility (SA8000), reflecting the region’s emphasis on sustainable and ethical manufacturing practices.
Advantages of European Suppliers
European HPPE glove suppliers offer several distinct advantages:
1. Technical Innovation
European manufacturers typically invest heavily in R&D, resulting in proprietary materials and designs that address specific application challenges. This includes innovations in fiber blending, coating technologies, and ergonomic construction.
2. Documented Compliance
European suppliers excel at providing comprehensive documentation of compliance with relevant standards, including detailed test reports and material safety data. This is particularly valuable for industries with stringent regulatory requirements.
3. Application-Specific Solutions
Rather than generic products, European manufacturers often develop gloves for specific applications or industries, with performance characteristics optimized for particular hazards, environments, and tasks.
4. Sustainable Manufacturing
Many European suppliers have adopted environmentally sustainable manufacturing processes, reducing water usage, eliminating harmful chemicals, and implementing renewable energy solutions in their facilities.
5. Worker Welfare Assurance
European manufacturing generally operates under stringent labor laws and safety regulations, providing assurance that products are manufactured under ethical working conditions.
Considerations When Sourcing from Europe
While European suppliers offer significant advantages, buyers should consider:
1. Premium Pricing
European-manufactured HPPE gloves typically command higher prices than those from Asian manufacturers, reflecting higher labor costs, stringent regulatory compliance, and investment in R&D.
2. Higher Minimum Order Quantities
Some European manufacturers focus on larger volume customers, with minimum order quantities that may be challenging for smaller businesses.
3. Longer Lead Times
Custom solutions from European manufacturers may involve longer development and production lead times due to their systematic approach to design and testing.
4. Geographic Logistics
For buyers outside Europe, shipping logistics and import procedures may add complexity and cost to the procurement process.
For organizations prioritizing documented compliance, application-specific solutions, and sustainable manufacturing, European suppliers represent an excellent choice despite the premium pricing. However, for many standard applications, Asian manufacturers like Qingdao Snell may offer comparable performance at more competitive price points while still meeting essential safety standards.
Comparison of HPPE Glove Manufacturers Across Different Regions
When sourcing custom HPPE protective gloves, understanding the relative strengths and characteristics of manufacturers from different regions can help you make an informed decision that balances quality, cost, and specific requirements. This comparative analysis examines key differences between manufacturers in China, the USA, and Europe to help guide your sourcing strategy.
Manufacturing Region | Cost Competitiveness | Customization Flexibility | Minimum Order Quantity | Production Capacity | Innovation & R&D | Quality Assurance | Sustainability Practices | Typical Lead Times |
---|---|---|---|---|---|---|---|---|
China (e.g., Qingdao Snell) | High | High | Medium (3,000-20,000 pcs) | Very High | Medium to High | Good with proper certifications | Improving rapidly | 30-45 days |
USA | Low | Medium to High | Low to Medium | Medium | Very High | Excellent | High | 15-30 days |
Europe | Low to Medium | Medium | Medium | Medium | Very High | Excellent | Very High | 20-40 days |
Manufacturing Strengths by Region
Chinese Manufacturers
Chinese manufacturers like Qingdao Snell excel in cost-effective production of large volumes while maintaining reasonable quality standards. Recent years have seen significant improvements in:
- Manufacturing technology with investments in automated production lines
- Quality control systems with implementation of international standards
- Material innovation through partnerships with global material suppliers
- Production flexibility allowing for customization at scale
Chinese manufacturers typically offer the best value proposition for medium to large orders where cost efficiency is important while still meeting international safety standards. Qingdao Snell, for example, provides ISO9001 and CE certified products at competitive prices while offering customization options for branding, packaging, and technical specifications.
American Manufacturers
U.S. manufacturers differentiate through:
- Specialized high-performance products for niche applications
- Advanced ergonomic designs based on extensive field testing
- Rapid development of custom solutions with lower MOQs
- Comprehensive technical support and application engineering
- Strong domestic supply chain relationships
American manufacturers are typically the preferred choice for specialized applications with unique requirements, particularly in highly regulated industries or those requiring rapid prototype development and testing.
European Manufacturers
European suppliers stand out for:
- Stringent quality control and documentation systems
- Advanced material science and innovative coating technologies
- Industry-specific expertise, particularly in food processing, pharmaceuticals, and precision manufacturing
- Environmental sustainability throughout the production process
- Comprehensive compliance with international standards and regulations
European manufacturers often serve premium market segments where performance, documentation, and compliance are prioritized over cost considerations.
Selecting the Right Manufacturing Partner
When evaluating potential manufacturing partners across these regions, consider these key factors:
1. Application Requirements
- For standard industrial applications with well-defined protection needs, Chinese manufacturers like Qingdao Snell often provide the best value.
- For specialized applications with unique hazards or performance requirements, American or European manufacturers may offer superior solutions.
2. Volume Needs
- For high-volume requirements (10,000+ pieces), Chinese manufacturers typically offer the best combination of capacity, quality, and cost.
- For smaller runs or pilot projects, American manufacturers generally offer more flexible MOQs.
3. Technical Support Requirements
- If extensive application engineering or on-site technical support is needed, regional proximity may favor domestic suppliers.
- For standard products with well-defined specifications, international suppliers can provide excellent value.
4. Compliance Documentation
- All regions can provide basic compliance documentation, but European manufacturers typically excel at providing comprehensive testing data and certification documentation.
- For highly regulated industries, the additional documentation from European or American suppliers may justify the premium pricing.
5. Total Cost of Ownership
- Consider not just unit pricing but also shipping costs, customs duties, lead times, and potential quality variation when calculating total cost.
- Faster availability of replacements from domestic suppliers may offset higher unit costs in critical applications.
For many organizations, the optimal strategy involves diversifying suppliers across regions:
- High-volume standard products from Chinese manufacturers
- Specialized or critical application products from American or European suppliers
- Contingency relationships across multiple regions to mitigate supply chain disruptions
As a procurement professional from a multinational manufacturing company noted, “We’ve found that companies like Qingdao Snell provide excellent value for our standard HPPE glove requirements, while we maintain relationships with specialized American and European suppliers for our more demanding applications. This hybrid approach gives us the best combination of cost efficiency and performance.”
What to Look for in a Reliable HPPE Glove Manufacturer
When investing in custom HPPE protective gloves, selecting a reliable manufacturer is crucial for ensuring consistent quality, timely delivery, and appropriate protection for your workforce. This section outlines the key criteria to evaluate when selecting a manufacturing partner for your HPPE glove requirements.
Quality Management Systems and Certifications
A manufacturer’s commitment to quality is best evidenced through formal certifications and documented quality management systems:
Essential Certifications
- ISO 9001: This internationally recognized standard for quality management systems demonstrates a manufacturer’s ability to consistently provide products that meet customer and regulatory requirements.
- CE Marking: For the European market, CE certification indicates compliance with health, safety, and environmental protection standards.
- EN 388: This specific standard for protective gloves against mechanical risks provides a numerical rating for cut, tear, puncture, and abrasion resistance.
- ANSI/ISEA 105: The American standard for hand protection classification provides performance ratings for various hazards.
Production Process Documentation
Look for manufacturers with:
- Documented production processes
- Material traceability systems
- Statistical process control methods
- Regular internal and third-party quality audits
Qingdao Snell exemplifies this commitment to quality with its comprehensive certifications including ISO 9001 and CE, ensuring their HPPE gloves meet international safety and quality standards across all production batches.
Manufacturing Capabilities and Technology
A manufacturer’s technological capabilities directly impact product consistency and performance:
Production Equipment
Evaluate manufacturers based on:
- Automated knitting machines for consistent HPPE liner production
- Precision coating systems for uniform application
- Advanced cutting and finishing equipment for consistent sizing
- Modern packaging systems for efficient handling
Testing Facilities
Reliable manufacturers maintain in-house testing equipment for:
- Cut resistance testing per relevant standards
- Abrasion resistance measurement
- Tear and puncture resistance verification
- Grip performance under various conditions
- Dexterity and flexibility assessment
Research and Development
Leading manufacturers invest in ongoing product development:
- Material research for enhanced performance
- Ergonomic design improvements
- Application-specific coating formulations
- Comfort and breathability enhancements
Supply Chain Stability and Material Sourcing
The reliability of your glove supply depends on the manufacturer’s supply chain management:
Material Sourcing
Evaluate how manufacturers:
- Source high-quality HPPE fibers from reputable suppliers
- Maintain relationships with multiple material vendors for continuity
- Implement material quality control and testing
- Secure sufficient material inventories for consistent production
Production Capacity and Flexibility
Reliable partners demonstrate:
- Sufficient production capacity to meet your volume requirements
- Flexible manufacturing systems that accommodate varying order sizes
- Ability to scale production during peak demand periods
- Contingency plans for equipment maintenance or breakdowns
Qingdao Snell operates six production lines across their facilities in Gaomi and Nantong, providing the capacity and flexibility to meet varying customer demands while maintaining consistent quality standards.
Customization Capabilities
For custom HPPE gloves, evaluate the manufacturer’s ability to accommodate your specific requirements:
Design Expertise
Look for manufacturers with:
- Technical design teams experienced in glove ergonomics
- 3D modeling and prototyping capabilities
- Understanding of industry-specific requirements
- Ability to translate performance specifications into design features
Customization Options
Evaluate the range of available customizations:
- Custom sizing beyond standard S-XXL ranges
- Color options for department or hazard coding
- Logo printing or embroidery for branding
- Specialized packaging for your distribution requirements
- Custom hang tags or product information
Sample Development Process
A systematic sample development process includes:
- Detailed specification review and confirmation
- Pre-production sample creation
- Performance testing of samples against specifications
- Approval process with clear communication
Business Ethics and Communication
The day-to-day working relationship with your manufacturer is crucial for successful partnerships:
Communication Effectiveness
Evaluate potential partners on:
- Clear, prompt communication in your business language
- Transparent discussion of capabilities and limitations
- Proactive notification of potential issues
- Accessible technical support for product questions
Business Ethics
Look for manufacturers demonstrating:
- Transparent pricing structures
- Honest representation of capabilities
- Respect for intellectual property and confidentiality
- Adherence to agreed terms and specifications
Social and Environmental Responsibility
Leading manufacturers increasingly emphasize:
- Ethical labor practices and worker safety
- Environmental management systems
- Waste reduction and energy efficiency initiatives
- Community engagement and responsibility
When evaluating manufacturers like Qingdao Snell, look beyond basic specifications to assess these broader aspects of reliability. The most successful partnerships balance technical capabilities with effective communication and ethical business practices to ensure consistent delivery of high-quality custom HPPE protective gloves that meet your specific requirements.
MOQ (Minimum Order Quantity) Considerations When Ordering HPPE Gloves
Understanding minimum order quantity (MOQ) requirements is crucial when sourcing custom HPPE protective gloves. MOQs directly impact your procurement strategy, inventory management, and unit pricing. This section explores key MOQ considerations to help you navigate this important aspect of glove procurement.
Typical MOQ Ranges by Manufacturer Type
Minimum order quantities vary significantly depending on the manufacturer’s size, location, and business model:
Direct Manufacturers in Asia
- Large manufacturers: 5,000-50,000 pairs per style/color
- Mid-sized manufacturers: 3,000-20,000 pairs per style/color
- Smaller specialized manufacturers: 1,000-5,000 pairs per style/color
Qingdao Snell Protective Products Co., Ltd., for example, has MOQs ranging from 3,000 to 20,000 pieces depending on the specific HPPE glove model and customization requirements. This positions them as accessible to mid-sized businesses while maintaining the economies of scale necessary for competitive pricing.
European Manufacturers
- Premium manufacturers: 1,000-10,000 pairs per style/color
- Specialized niche producers: 500-3,000 pairs per style/color
- Custom design specialists: 300-1,500 pairs per style/color
North American Manufacturers
- Large domestic producers: 2,500-15,000 pairs per style/color
- Mid-sized specialists: 1,000-5,000 pairs per style/color
- Custom/specialty manufacturers: 250-1,000 pairs per style/color
Distributors and Trading Companies
- Large industrial distributors: 500-2,000 pairs per style/color
- Specialized safety equipment distributors: 100-1,000 pairs per style/color
- Local distributors: As low as 25-100 pairs (with premium pricing)
Factors Affecting MOQ Requirements
Several factors influence a manufacturer’s MOQ requirements:
1. Production Setup Costs
Each production run involves fixed setup costs including:
- Machine programming and calibration
- Material changeovers
- Quality control setup
- Packaging line configuration
These fixed costs must be amortized across the production volume, necessitating minimum quantities for cost-efficiency.
2. Material Purchasing Economics
Raw materials for HPPE gloves, including HPPE yarn, coating chemicals, and reinforcement materials, are typically purchased in bulk quantities:
- HPPE fiber is often available only in minimum lot sizes
- Coating materials have minimum batch sizes for consistency
- Custom colored yarns have higher minimum purchase requirements
3. Customization Complexity
More complex customization typically increases MOQ requirements:
- Standard catalog items: Lower MOQs
- Custom colors: Moderate increase in MOQs
- Custom patterns or designs: Significant increase in MOQs
- Custom sizing or special features: Highest MOQs
4. Manufacturer’s Business Model
A manufacturer’s target market and business strategy influence their MOQ approach:
- Mass production-focused manufacturers: Higher MOQs, lower unit costs
- Flexible manufacturers serving diverse markets: Moderate MOQs with balanced pricing
- Custom specialists: Lower MOQs with premium pricing
Strategies for Managing MOQ Challenges
If a manufacturer’s standard MOQ exceeds your immediate needs, consider these approaches:
1. Order Consolidation
Combine orders across multiple departments or facilities to meet minimum quantities while distributing inventory appropriately.
2. Phase-In Testing Approach
Negotiate a smaller initial order for testing and evaluation, with a commitment to larger follow-on orders if performance meets expectations.
3. Standard with Modified Branding
Select standard catalog items that meet your technical requirements, with only simple customization like logo printing, which typically has lower MOQ requirements.
4. Distributor Partnerships
Work with distributors who can aggregate demand from multiple customers, enabling access to custom products with lower individual order quantities.
5. Long-Term Agreements
Negotiate lower MOQs in exchange for longer-term purchase commitments that provide manufacturers with production stability.
Calculating the True Cost Impact of MOQs
When evaluating MOQ requirements, consider these factors to determine the true cost impact:
1. Unit Price Differentials
Calculate the unit price difference between ordering at minimum quantity versus your ideal order quantity.
2. Inventory Carrying Costs
Factor in the cost of holding excess inventory:
- Warehouse space requirements
- Capital tied up in inventory
- Risk of obsolescence or expiration
- Insurance and handling costs
3. Order Frequency Impact
Compare the costs of:
- Fewer orders at higher quantities
- More frequent orders at lower quantities (if available)
- Mixed approach with stock replenishment planning
4. Quality and Consistency Benefits
Consider the quality advantages of larger production runs:
- Greater consistency across production
- Potentially better economies of scale in production
- Established relationship with the manufacturer
For many organizations, working with manufacturers like Qingdao Snell that offer moderate MOQs represents an ideal balance between cost efficiency and inventory management. Their MOQ range of 3,000-20,000 pieces accommodates mid-sized operations while providing the volume necessary for competitive pricing and consistent quality.
“Understanding a manufacturer’s MOQ requirements is essential for effective procurement planning,” notes a procurement expert from a leading industrial company. “We’ve found that manufacturers with moderate MOQs like Qingdao Snell often provide the best balance between flexibility and value for our industrial safety equipment needs.”
How to Customize HPPE Gloves with Your Logo and Branding
Customizing HPPE protective gloves with your company’s logo and branding creates numerous benefits beyond mere aesthetics. Custom-branded gloves reinforce safety culture, promote corporate identity, reduce theft, and facilitate inventory management. This comprehensive guide explores the customization options, processes, and best practices for creating HPPE gloves that represent your brand while maintaining optimal protection.
Benefits of Custom Branding on HPPE Gloves
Investing in custom-branded gloves delivers multiple organizational advantages:
1. Enhanced Safety Culture
Branded PPE reinforces your company’s commitment to worker safety, serving as a constant visual reminder of safety protocols and ownership of protection.
2. Corporate Identity Reinforcement
Custom gloves extend your brand identity to every aspect of operations, creating a cohesive professional appearance across your workforce.
3. Reduced Loss and Theft
Distinctively branded gloves are less likely to be removed from the workplace, reducing replacement costs and ensuring workers always have appropriate protection available.
4. Improved Inventory Management
Custom branding makes it easier to identify your company’s gloves during inventory counts, reducing confusion with similar standard models.
5. Departmental Differentiation
Color-coded branding can help identify gloves designated for specific departments, processes, or hazard levels, improving compliance with job-specific protection requirements.
Available Customization Methods
Several methods are available for applying your brand to HPPE protective gloves, each with distinct advantages and limitations:
Screen Printing
- Process: Ink is forced through a mesh screen onto the glove surface
- Advantages: Vibrant colors, detailed logos, durable in most environments, cost-effective for larger orders
- Limitations: Limited placement options (typically back of hand), minimum order quantities, potential durability issues with heavy abrasion
- Best for: Bold logos, text, and simple graphics on the back of the hand
Heat Transfer
- Process: Logo is printed on a transfer material and heat-pressed onto the glove
- Advantages: Detailed multi-color designs, consistent application, good durability
- Limitations: Higher cost for small quantities, limited placement options
- Best for: Complex logos or designs requiring precise color matching
Embroidery
- Process: Logo is stitched directly onto the glove material
- Advantages: Premium appearance, exceptional durability, textured finish
- Limitations: Limited to cuff area to avoid compromising protection, limited color gradients, higher cost
- Best for: Premium branding on glove cuffs, particularly for supervisory or customer-facing roles
Silicone Printing
- Process: Silicone-based ink creates a raised, three-dimensional logo
- Advantages: Enhanced visibility, tactile feel, excellent durability, potential grip enhancement
- Limitations: Higher cost, limited color options, minimum order requirements
- Best for: Applications where the logo may also serve as a functional grip element
Pad Printing
- Process: Silicone pad transfers ink from an etched plate to the glove surface
- Advantages: Works on curved surfaces, precise detail reproduction, cost-effective for smaller designs
- Limitations: Limited size of imprint area, typically single-color applications
- Best for: Small logos or text on fingertips or curved surfaces
Design Considerations for Effective Branding
Creating effective branding for HPPE gloves requires balancing visibility with practicality:
Logo Placement Options
- Back of Hand: Most visible and common placement, minimal interference with function
- Cuff Area: Less visible during use but offers larger printing area and doesn’t affect dexterity
- Palm Side: Limited visibility but creates brand presence during handshakes or when hands are visible
- Fingertips: High visibility for specific applications but limited space for designs
Design Simplification
Complex logos may need simplification for effective reproduction on gloves:
- Reduce intricate details that may not reproduce well at small sizes
- Consider single-color versions of multi-color logos
- Ensure text is large enough to remain legible after application
- Maintain adequate spacing between design elements
Color Selection Strategies
- Choose colors with high contrast against the glove base color
- Limit the number of colors to control costs (each additional color typically increases price)
- Consider how colors will appear under different lighting conditions in the workplace
- Select colors that align with your corporate standards while ensuring visibility
Working with Manufacturers on Custom Branding
Collaborating effectively with manufacturers ensures successful customization:
Artwork Preparation
- Provide vector files (AI, EPS, PDF) for optimal reproduction quality
- Include Pantone color specifications for accurate color matching
- Supply minimum resolution of 300 dpi for any raster artwork
- Include dimensions and placement specifications
Sampling Process
A typical customization process includes:
- Digital proof approval (artwork rendering on glove template)
- Physical sample production for approval
- Production sample from actual production run
- Final approval before full production
Quality Control Specifications
Establish clear quality parameters including:
- Color matching tolerance
- Logo placement accuracy
- Print adhesion testing protocols
- Wash/wear durability requirements
Qingdao Snell Protective Products Co., Ltd. offers comprehensive customization services for HPPE gloves, including all major printing methods and color options. Their design team can assist with artwork adaptation and provides digital proofs and physical samples before production. With their established quality control systems, they ensure consistent branding across large production runs while maintaining the protective integrity of the gloves.
Their typical process involves a 3-5 day sample development timeline followed by production runs of 20-30 days depending on volume and complexity. As a factory-direct supplier, they can accommodate various customization requirements while maintaining competitive pricing, with minimum order quantities typically starting at 3,000 pieces for custom-branded HPPE gloves.
“Effective customization balances brand visibility with the functional requirements of the glove,” explains a design specialist from Qingdao Snell. “We work closely with customers to ensure their branding enhances rather than compromises the protective qualities that make HPPE gloves essential safety equipment.”
What Are the Most Durable Materials for HPPE Protective Gloves?
The durability and performance of HPPE protective gloves depend significantly on the materials used in their construction. HPPE itself offers exceptional properties, but when combined with other materials and coatings, its protective capabilities can be substantially enhanced. This section explores the most durable material combinations for HPPE gloves and how they address specific workplace hazards.
Core HPPE Fiber Technologies
The foundation of cut-resistant gloves begins with the HPPE fiber itself, available in several variations:
Standard HPPE
- Offers 3-5 times the strength of standard aramid fibers
- Provides good cut resistance with excellent comfort
- Maintains flexibility and dexterity
- Resistant to moisture absorption
- Maintains properties in wet environments
Enhanced HPPE Blends
- HPPE combined with steel or fiberglass microfibers
- Significantly higher cut resistance than standard HPPE
- Maintains flexibility while increasing protection
- Can achieve ANSI cut levels A4-A7
- Ideal for high-risk environments with sharp materials
Engineered HPPE Composites
- Proprietary blends incorporating advanced nanomaterials
- Exceptional cut resistance with reduced weight
- Enhanced durability against abrasion
- Superior performance in extreme conditions
- Typically used in specialized industrial applications
According to materials engineering data, the tensile strength of HPPE fibers can range from 2.4 to 3.5 GPa, making them significantly stronger than conventional synthetic fibers while maintaining lower weight and greater flexibility.
Reinforcement Materials for Enhanced Protection
To address specific protection requirements, HPPE is often combined with reinforcement materials:
Steel or Stainless Steel Microfiber
- Dramatically increases cut resistance
- Excellent for extreme cutting hazards
- Adds some weight to the glove
- May reduce flexibility slightly
- Can be engineered to maintain dexterity
Fiberglass Filaments
- Enhances cut resistance with minimal weight increase
- Does not conduct electricity
- Maintains good flexibility
- Less expensive than steel reinforcement
- Breaks rather than stretches when cut
Carbon Fiber
- Excellent tensile strength with minimal weight
- Good cut resistance properties
- Anti-static properties for electronic applications
- Superior temperature resistance
- Premium pricing reflects advanced technology
Aramid Fibers (Kevlar®/Twaron®)
- Complements HPPE with heat resistance
- Good cut and abrasion resistance
- Excellent durability in high-wear applications
- Higher cost than standard reinforcements
- Slightly more rigid than pure HPPE
Coating Technologies for Enhanced Grip and Protection
Coatings significantly affect durability, grip, and specific hazard protection:
Polyurethane (PU) Coatings
- Excellent abrasion resistance
- Superior dexterity and tactile sensitivity
- Good dry grip characteristics
- Moderate oil resistance
- Cost-effective option for precision work
Nitrile Coatings
- Exceptional abrasion resistance (up to 3x that of latex)
- Excellent resistance to oils, fuels, and many chemicals
- Good puncture resistance
- Maintains grip in oily conditions
- Available in various thicknesses for specific applications
Sandy/Foam Nitrile Coatings
- Enhanced grip in oily/wet conditions
- Microsurface increases friction coefficient
- Excellent wear resistance
- Superior oil dispersion properties
- Ideal for handling slippery components
Latex Coatings
- Excellent elasticity and comfort
- Superior grip in dry and wet conditions
- Good abrasion resistance
- Limited chemical and oil resistance
- Cost-effective for general applications
Specialized Polymer Coatings
- Proprietary blends for specific applications
- Enhanced chemical resistance profiles
- Specialized temperature resistance
- Application-specific grip characteristics
- Often developed for particular industries
Qingdao Snell offers a comprehensive range of coating options across their HPPE glove lines, including specialized formulations developed for specific industry requirements. Their coating technologies are engineered to maximize durability while maintaining the comfort and dexterity that make HPPE gloves practical for all-day wear.
Durability-Enhancing Construction Techniques
Beyond materials, construction techniques significantly impact glove durability:
Seamless Knitting Technology
- Eliminates weak points created by seams
- Reduces irritation and pressure points
- Enhances overall glove lifespan
- Allows for anatomically correct fit
- Enables zone-specific reinforcement
Double-Layer Construction
- Provides additional protection in high-wear areas
- Extends glove lifespan significantly
- Can incorporate different materials in each layer
- Allows for specialized protection zones
- Maintains flexibility through engineered design
Reinforced Thumb Crotch
- Addresses common failure point between thumb and forefinger
- Extends glove life significantly
- Maintains dexterity in critical pinch area
- Can incorporate higher cut-resistance in this zone
- Critical for applications with gripping actions
Extended Cuff Designs
- Protects the wrist area from hazards
- Reduces gap between glove and sleeve
- Prevents debris entry into the glove
- Available in various lengths for specific applications
- Can incorporate additional securing mechanisms
Material Selection for Specific Applications
The optimal material combination depends on specific industry requirements:
Metal Fabrication and Sheet Metal Handling
- HPPE-fiberglass composite liner
- Sandy nitrile coating for oily metal sheets
- Reinforced thumb crotch for handling actions
- Cut level A4-A6 (ANSI) or D-E (EN 388)
Glass Manufacturing and Handling
- HPPE-steel microfiber composite
- Full nitrile coating for liquid barrier
- Extended cuff for wrist protection
- Cut level A5-A7 (ANSI) or E-F (EN 388)
Automotive Assembly
- Lightweight HPPE-composite liner
- Polyurethane fingertip coating for dexterity
- Breathable back for comfort during extended wear
- Cut level A2-A4 (ANSI) or B-C (EN 388)
Food Processing
- Food-grade HPPE liner (non-colored)
- Food-safe nitrile or polyurethane coating
- Fully washable construction
- Cut level appropriate to specific processing tasks
Through careful selection of core materials, reinforcements, and coatings, modern HPPE protective gloves can deliver an optimal balance of protection, comfort, and durability for specific workplace hazards. Consulting with established manufacturers like Qingdao Snell can help identify the most appropriate material combination for your specific application requirements.
How to Ensure Quality Control About HPPE Protective Gloves?
Implementing effective quality control for HPPE protective gloves is crucial for ensuring consistent protection, durability, and performance. A comprehensive quality control program encompasses everything from raw material inspection to final product testing. This section outlines best practices for quality assurance when sourcing or manufacturing HPPE gloves.
Establishing Clear Quality Specifications
The foundation of effective quality control is a detailed set of specifications that define acceptable quality standards:
Performance Specifications
- Cut resistance level per relevant standards (ANSI/ISEA 105, EN 388)
- Abrasion resistance requirements with test methods
- Tear and puncture resistance minimums
- Grip performance under specified conditions
- Dexterity requirements (e.g., ability to pick up small objects)
Material Specifications
- HPPE fiber type, denier, and blend composition
- Coating material composition and thickness
- Liner weight and gauge measurements
- Reinforcement material specifications
- Color stability and colorfastness requirements
Construction Specifications
- Knitting technique and stitch density
- Seamless construction verification
- Coating application method and coverage
- Cuff design and elasticity requirements
- Size tolerance measurements
Appearance Standards
- Color consistency requirements
- Coating uniformity specifications
- Logo/branding placement accuracy
- Packaging presentation standards
- Freedom from visual defects (spots, runs, thin areas)
Quality specifications should be documented in a formal quality manual that serves as the reference standard for all inspection and testing activities.
Raw Material Inspection and Testing
Quality control begins with thorough inspection of incoming materials:
HPPE Fiber Verification
- Certificate of analysis review from fiber supplier
- Fiber diameter consistency testing
- Tensile strength verification
- Color matching to standards
- Contamination inspection
Coating Materials Assessment
- Viscosity testing of liquid coatings
- Specific gravity measurement
- Curing properties verification
- Chemical composition analysis
- Shelf life verification
Reinforcement Materials Inspection
- Dimensional consistency verification
- Material certification review
- Structural integrity testing
- Compatibility testing with HPPE fiber
Qingdao Snell implements rigorous raw material inspection protocols, including supplier certification requirements and incoming material testing. This foundation ensures that only approved materials meeting their specifications enter the production process, supporting consistent final product quality.
In-Process Quality Control Measures
Quality control continues throughout the manufacturing process with specific checkpoints:
Liner Production Monitoring
- Knitting machine setup verification
- Stitch density checks
- Dimensional stability testing
- Weight consistency verification
- Visual inspection for defects
Coating Application Control
- Coating thickness measurement
- Coverage uniformity inspection
- Curing temperature and time monitoring
- Adhesion testing
- Visual inspection for skips or bubbles
Assembly and Finishing Inspection
- Size verification against specifications
- Seam inspection where applicable
- Cuff elasticity testing
- Pairing accuracy verification
- Pre-packaging visual inspection
Statistical process control methods should be implemented at each stage, with control charts monitoring critical parameters to identify trends before they result in quality issues.
Final Product Testing and Inspection
Comprehensive testing of finished gloves ensures they meet all performance requirements:
Physical Testing Protocol
- Cut resistance testing per ANSI/ISEA 105 or EN 388
- Abrasion resistance testing (Taber/Martindale method)
- Tear strength measurement
- Puncture resistance verification
- Tensile strength testing
Functional Testing Protocol
- Dexterity testing (coin pick-up or similar methods)
- Grip testing under dry, wet, and oily conditions
- Donning and doffing evaluation
- Sizing verification against standards
- Comfort assessment with test wearers
Inspection Sampling Plan
- AQL (Acceptable Quality Level) determination
- Statistical sampling methodology
- Critical/major/minor defect classifications
- Inspection frequency requirements
- Documentation and traceability procedures
Leading manufacturers like Qingdao Snell maintain comprehensive testing laboratories with specialized equipment for evaluating protective glove performance. Their testing protocols align with international standards while also incorporating application-specific tests developed through customer collaboration.
Supplier Qualification and Monitoring
For organizations sourcing rather than manufacturing HPPE gloves, supplier qualification is critical:
Initial Supplier Assessment
- Manufacturing capability evaluation
- Quality management system verification
- Compliance certification review
- Reference checks and historical performance
- Financial stability assessment
Ongoing Supplier Monitoring
- Regular quality performance reviews
- Statistical analysis of defect rates
- Corrective action verification
- Periodic facility audits
- Management system certification maintenance
Supplier Development Initiatives
- Joint quality improvement projects
- Technical capability enhancement
- Process standardization collaboration
- Technology transfer where appropriate
- Long-term partnership development
Documentation and Traceability Systems
Effective quality control requires comprehensive documentation:
Product Traceability Documentation
- Lot coding systems
- Material source traceability
- Production date and shift identification
- Inspector identification on records
- Test result documentation by batch
Quality Records Maintenance
- Incoming inspection results
- In-process inspection data
- Final testing documentation
- Customer feedback and complaints
- Corrective action records
Certification Documentation
- Test reports from accredited laboratories
- Compliance certificates for applicable standards
- Material safety data sheets
- Technical specification documents
- User instruction development and verification
Qingdao Snell maintains comprehensive documentation for all products, with traceability from raw material receipt through production to final shipment. This documentation supports both quality assurance and regulatory compliance requirements.
“Quality isn’t just about inspection—it’s built into every stage of our production process,” explains a quality manager at Qingdao Snell. “From material selection through final testing, we maintain rigorous standards that ensure our HPPE gloves deliver consistent protection and performance for every customer.”
By implementing comprehensive quality control measures throughout the supply chain, organizations can ensure that their HPPE protective gloves consistently deliver the protection, comfort, and durability required for their specific applications.
Frequently Asked Questions About HPPE Protective Gloves
What makes HPPE gloves different from standard cut-resistant gloves?
HPPE (High-Performance Polyethylene) gloves represent an advanced category of cut-resistant protection that offers several advantages over traditional materials. Unlike standard cut-resistant gloves made with materials like leather, cotton, or basic aramid fibers, HPPE gloves provide superior cut resistance while maintaining exceptional comfort and dexterity.
The molecular structure of HPPE creates a fiber that is up to 15 times stronger than steel on a weight-for-weight basis, yet remains lightweight and flexible. This allows HPPE gloves to achieve high cut-resistance ratings (ANSI A3-A7 or EN 388 C-F) without the bulk and stiffness associated with traditional cut-resistant materials.
Additionally, HPPE is inherently moisture-resistant and performs well in both wet and dry conditions, unlike some aramid fibers that can absorb moisture and become uncomfortable. HPPE also maintains its protective properties across a wider temperature range than many alternative materials.
For applications requiring both high cut resistance and precision handling, HPPE gloves provide an optimal balance of protection and functionality that standard cut-resistant gloves cannot match.
How do I determine the right cut level for my application?
Selecting the appropriate cut resistance level requires a systematic risk assessment approach:
- Identify Hazards: Document all cutting hazards in the specific work environment, including sharp materials, tools, equipment, and processes.
- Assess Severity and Likelihood: Evaluate both the potential severity of cuts (from minor to severe/life-threatening) and the likelihood of occurrence (from rare to frequent).
- Review Incident History: Analyze past cut injuries in similar operations to identify patterns and high-risk activities.
- Understand Cut Resistance Standards:
- ANSI/ISEA 105 (North America): Rates gloves on an A1-A9 scale with A9 providing the highest protection
- EN 388 (Europe): Uses an A-F scale with F offering maximum cut resistance
- Match Protection to Risk Level: Application Type Typical ANSI Cut Level Typical EN 388 Cut Level Light assembly, packaging A1-A2 A-B General warehouse, light materials handling A2-A3 B-C Automotive assembly, HVAC work A3-A4 C-D Metal fabrication, glass handling A4-A6 D-E Recycling, sheet metal stamping A6-A9 E-F
- Field Testing: Before full implementation, test selected gloves in the actual work environment to confirm they provide adequate protection without hindering required tasks.
- Regular Reassessment: Cut hazards may change with new materials, processes, or equipment, requiring periodic review of protection requirements.
Remember that higher cut resistance typically involves trade-offs in dexterity, comfort, or cost. The goal is to select the minimum cut level that provides adequate protection for the specific hazards present.
How long do HPPE protective gloves typically last?
The lifespan of HPPE protective gloves varies significantly based on several factors:
Usage Intensity:
- Light use (1-2 hours daily): Typically 3-6 weeks
- Moderate use (4-5 hours daily): Typically 2-4 weeks
- Heavy use (8+ hours daily): Typically 1-2 weeks
Application Environment:
- Clean assembly environments: Extended lifespan
- Abrasive materials handling: Reduced lifespan
- Chemical exposure: Potentially shortened lifespan depending on chemical compatibility
- Oil/grease exposure: Variable impact depending on coating type
Glove Construction Quality:
- Premium HPPE blends with reinforcement: Longer lifespan
- Higher gauge (thinner knit) gloves: Generally shorter lifespan
- Quality of coating application: Significant impact on durability
Care and Maintenance:
- Proper cleaning according to manufacturer instructions can extend lifespan by 15-30%
- Rotation between multiple pairs reduces wear accumulation
- Proper storage away from UV exposure, heat, and contaminants extends useful life
For optimal cost-efficiency, implement a glove management program that tracks replacement frequency across different job functions and environments. This data can help refine glove selection and identify opportunities for improved worker training or process modifications that might extend glove lifespan.
Can HPPE gloves be washed and reused?
Yes, most HPPE protective gloves can be washed and reused, but proper washing procedures are essential to maintain protective properties:
Washing Guidelines for HPPE Gloves:
Coating Type | Recommended Cleaning Method | Maximum Wash Temperature | Drying Method | Special Considerations |
---|---|---|---|---|
Polyurethane (PU) | Machine wash, mild detergent | 40°C/104°F | Air dry only | Avoid fabric softeners |
Nitrile | Machine or hand wash | 60°C/140°F | Air dry only | Can withstand stronger detergents |
Latex | Hand wash recommended | 40°C/104°F | Air dry only | Avoid bleach-based products |
Uncoated HPPE | Machine wash, mild cycle | 40°C/104°F | Air dry only | Use mesh laundry bag |
Important Washing Precautions:
- Never use bleach as it can degrade HPPE fibers
- Avoid high-temperature washing or drying which can damage coatings
- Do not dry clean HPPE gloves
- Check manufacturer’s specific instructions as they may vary
Post-Washing Inspection:
Before reuse, inspect washed gloves for:
- Signs of cuts or tears in the liner
- Coating degradation or separation
- Reduced elasticity in the cuff
- Any holes or thin spots
Washing Impact on Protection:
While washing extends the useful life of HPPE gloves, be aware that:
- Cut resistance generally remains stable through multiple wash cycles
- Grip performance may gradually diminish with repeated washing
- Coating durability will determine maximum number of wash cycles
- Some specialized treatments may have reduced effectiveness after washing
For food processing or cleanroom environments, select HPPE gloves specifically designed for repeated washing, as these incorporate more wash-resistant coatings and construction methods.
Are there specific storage requirements for HPPE gloves?
Proper storage of HPPE protective gloves is essential for maintaining their protective properties and extending their shelf life. Follow these guidelines for optimal storage:
Environmental Conditions:
- Store in cool, dry conditions between 10-25°C (50-77°F)
- Maintain relative humidity between 30-50%
- Avoid direct sunlight or UV exposure, which can degrade polymers
- Keep away from ozone sources like electric motors or high-voltage equipment
- Store away from heating vents, radiators, or other heat sources
Storage Configuration:
- Store flat or hang gloves in a way that maintains their natural shape
- Avoid folding or creasing coated gloves for extended periods
- Do not place heavy objects on stored gloves
- Use original packaging when possible for additional protection
Inventory Management:
- Implement a first-in, first-out (FIFO) inventory system
- Rotate stock to ensure older gloves are used before newer stock
- Typical shelf life is 3-5 years when stored properly
- Date marking on packaging helps track storage duration
Separation Requirements:
- Store away from chemicals, solvents, and oils that could contaminate gloves
- Keep separate from sharp objects that could damage gloves during storage
- Maintain separation from incompatible materials that might cause degradation
Pre-Distribution Inspection:
After extended storage periods, inspect gloves for:
- Coating tackiness or degradation
- Unusual stiffness or loss of flexibility
- Discoloration indicating potential degradation
- Odor changes that might indicate material breakdown
By following these storage guidelines, you can ensure your inventory of HPPE protective gloves maintains its protective properties and remains ready for use when needed.
What certifications should I look for when purchasing HPPE gloves?
When purchasing HPPE protective gloves, look for these key certifications and standards to ensure you’re getting a quality product that meets relevant safety requirements:
Essential Safety Standards:
- EN 388:2016 (European Standard for Protective Gloves against Mechanical Risks)
- Features a pictogram with four to six performance levels
- Measures: abrasion, blade cut, tear, puncture resistance
- Newer version includes ISO 13997 cut test (A-F scale)
- Impact protection (P) if applicable
- ANSI/ISEA 105-2016 (American National Standard for Hand Protection Classification)
- Cut resistance rated on A1-A9 scale
- Puncture resistance rated on 1-5 scale
- Abrasion resistance rated on 0-6 scale
- ISO 13997 (Protective Clothing – Mechanical Properties – Cut Resistance Test)
- Measures force required to cut through material with single blade pass
- Results expressed in Newtons (N)
- Critical for high-performance cut-resistant gloves
Quality Management Certifications:
- ISO 9001 (Quality Management System)
- Ensures consistent quality through documented processes
- Indicates manufacturer has formal quality control systems
- Requires regular third-party audits
Environmental Standards:
- ISO 14001 (Environmental Management System)
- Indicates environmentally responsible manufacturing
- Ensures compliance with environmental regulations
- Demonstrates commitment to sustainable production
Industry-Specific Certifications:
- FDA Compliance (for food processing applications)
- Confirms materials are safe for food contact
- Required for gloves used in food handling
- REACH Compliance (Registration, Evaluation, Authorization of Chemicals)
- Ensures gloves don’t contain restricted substances
- Important for European markets and chemical safety
Product Verification:
When evaluating certifications, verify that:
- Certification marks appear on both product and packaging
- Test reports are available upon request
- Certificates are issued by accredited testing bodies
- Performance levels match your specific application requirements
Qingdao Snell Protective Products maintains comprehensive certifications including ISO 9001 and CE marking with EN 388 testing for their HPPE glove range, ensuring their products meet international safety and quality standards.
How do different coatings affect HPPE glove performance?
Coatings significantly impact the performance and application suitability of HPPE protective gloves. Understanding these differences helps in selecting the optimal glove for specific work environments:
Coating Type | Grip Performance | Durability | Oil/Liquid Resistance | Breathability | Best Applications |
---|---|---|---|---|---|
Polyurethane (PU) | Excellent in dry conditions, Good in light wet | Good abrasion resistance (3-4 on EN 388 scale) | Moderate resistance to light oils | Excellent breathability | Precision assembly, electronics, automotive components |
Nitrile | Very good in dry conditions, Excellent in oily environments | Excellent abrasion resistance (4-5 on EN 388 scale) | Superior resistance to oils, fuels, and many chemicals | Moderate breathability | Oil and gas, automotive, machinery maintenance, metal fabrication |
Sandy/Foam Nitrile | Superior in oily conditions, Excellent in wet environments | Very good abrasion resistance (4 on EN 388 scale) | Enhanced oil grip through dispersion | Moderate breathability | Heavy machinery, oily parts handling, wet work environments |
Latex | Excellent in dry and wet conditions, Poor in oily environments | Good abrasion resistance (3 on EN 388 scale) | Poor resistance to oils and solvents | Good breathability | Construction, general handling, glass handling |
PVC/Vinyl | Moderate in dry conditions, Good in wet environments | Moderate abrasion resistance (2-3 on EN 388 scale) | Good chemical resistance, moderate oil resistance | Poor breathability | Chemical handling, janitorial work, light industrial applications |
Uncoated | Limited grip in all conditions | Variable based on liner construction | No resistance to liquids | Maximum breathability | Inspection tasks, light assembly, liner gloves |
Additional Coating Considerations:
Coverage Options Impact:
- Full Coating: Maximizes liquid protection but reduces breathability
- Palm Coating: Balances protection with breathability for general use
- Fingertip Coating: Optimizes tactile sensitivity while providing grip where most needed
- Three-Quarter Coating: Offers expanded protection while maintaining partial breathability
Coating Thickness Trade-offs:
- Thinner coatings provide better dexterity but reduced durability
- Thicker coatings offer enhanced durability and chemical resistance but reduce tactile sensitivity
- Microfoam structures can provide thickness without sacrificing flexibility
Environmental Factors:
- Temperature extremes can affect coating performance (nitrile hardens in cold, PU softens in heat)
- UV exposure degrades some coatings more rapidly than others
- Chemical exposure can cause swelling or deterioration depending on coating compatibility
Qingdao Snell offers a comprehensive range of coating options across their HPPE glove line, allowing customers to select the ideal combination of grip, durability, and protection for their specific application requirements.
Can HPPE gloves protect against chemicals and liquids?
HPPE gloves primarily provide cut protection rather than chemical resistance. However, their performance against chemicals and liquids depends largely on the coating applied:
Chemical and Liquid Protection Capabilities:
Coating Type | Water Resistance | Oil Resistance | Organic Solvent Resistance | Acid/Base Resistance | Limitations |
---|---|---|---|---|---|
Nitrile | Excellent | Excellent | Good against many solvents | Good against dilute solutions | Not effective against ketones, some aromatics |
Polyurethane (PU) | Good | Moderate | Poor to Fair | Limited | Degrades with extended chemical exposure |
Latex | Very Good | Poor | Poor | Good against dilute bases, Fair against acids | Allergenic for some users, breaks down with oils |
PVC | Excellent | Good | Fair | Good | Less dexterity, environmental concerns |
Uncoated HPPE | Poor | Poor | Poor | Poor | Provides no chemical barrier |
Important Limitations to Consider:
- Permeation vs. Degradation:
- Coatings may initially resist penetration but degrade with extended exposure
- Breakthrough times vary significantly based on chemical concentration and temperature
- Permeation may occur without visible signs of degradation
- Coating Coverage Matters:
- Only fully coated gloves provide liquid barrier protection across the entire hand
- Palm-coated gloves leave the back of the hand exposed to liquid contact
- Knit HPPE liners typically allow liquid to pass through eventually
- Not a Substitute for Chemical Gloves:
- HPPE gloves, even with coatings, are not designed as primary chemical protection
- For known chemical hazards, use gloves specifically designed and tested for chemical resistance
- For combined chemical and cut hazards, consider chemical-resistant gloves with cut protection or layering options
- Application Considerations:
- Incidental/splash contact: Coated HPPE gloves may provide adequate short-term protection
- Immersion applications: HPPE gloves are generally unsuitable
- Mixed hazards: Assess primary risk (cut vs. chemical) to determine appropriate protection
For applications requiring both chemical protection and cut resistance, consider these options:
- Chemical-resistant gloves with built-in cut protection
- Cut-resistant HPPE liner worn under a chemical-resistant outer glove
- Specialized composite gloves designed for specific combined hazards
Always consult chemical compatibility charts and manufacturer recommendations for specific applications involving chemical exposure.
What are the latest innovations in HPPE glove technology?
The HPPE protective glove industry continues to evolve with significant innovations enhancing performance, comfort, and sustainability. Here are the latest advancements shaping the future of hand protection:
Advanced Material Developments:
- Nano-Engineered HPPE Fibers
- Incorporation of nanoparticles into HPPE structure
- Enhanced cut resistance without added weight
- Improved abrasion resistance at the molecular level
- Potential for specialized properties (antimicrobial, conductive)
- Bio-Based HPPE Alternatives
- Development of plant-derived high-performance fibers
- Reduced environmental impact while maintaining protection
- Biodegradable options for specific applications
- Renewable resource utilization
- Hybrid Composite Materials
- Specialized blends combining HPPE with other high-performance fibers
- Targeted performance enhancements for specific applications
- Multi-hazard protection in single-layer construction
- Optimized comfort-to-protection ratios
Manufacturing and Design Innovations:
- 3D Knitting Technology
- Seamless gloves with anatomically correct shaping
- Zone-specific performance characteristics
- Reduced waste through precision manufacturing
- Enhanced comfort through engineered fit
- Advanced Coating Technologies
- Water-based formulations reducing environmental impact
- Grip-enhancing microstructures for extreme conditions
- Self-cleaning surface treatments
- Application-specific coating patterns
- Smart/Connected Glove Integration
- Embedded sensors monitoring environmental conditions
- Impact detection and warning systems
- Usage tracking for safety compliance
- Temperature monitoring for extreme environments
Ergonomic and Comfort Advancements:
- Thermoregulating Technologies
- Phase-change materials for temperature stability
- Enhanced breathability through engineered structures
- Moisture-wicking treatments for improved comfort
- Cold environment performance optimization
- Reduced Hand Fatigue Design
- Mapped flexibility zones aligned with hand anatomy
- Variable compression for improved circulation
- Reduced weight through material optimization
- Enhanced dexterity through strategic reinforcement
Industry-Specific Innovations:
- Task-Optimized Designs
- Industry-specific glove architecture for specialized tasks
- Performance customization for unique work environments
- Application-engineered protection zones
- Task-specific grip patterns
- Enhanced Visibility Features
- High-visibility materials for low-light environments
- Color-coding systems for safety protocols
- Reflective elements for hazardous environments
- Visual wear indicators for replacement timing
Qingdao Snell Protective Products continues to invest in research and development, incorporating many of these innovations into their HPPE glove lineup. Their technical team works closely with material scientists and end-users to develop next-generation protective solutions that address evolving workplace safety challenges while maintaining the comfort and usability essential for workforce adoption.
As a procurement professional notes, “The rapid pace of innovation in HPPE glove technology means that solutions that weren’t possible just a few years ago are now becoming standard. Working with forward-thinking manufacturers helps ensure your safety program benefits from these advancements.”
How do I properly size HPPE gloves for my workforce?
Proper sizing of HPPE protective gloves is crucial for both safety and productivity. Ill-fitting gloves can reduce protection, decrease dexterity, accelerate hand fatigue, and ultimately lead to non-compliance. Follow these comprehensive guidelines to ensure optimal fit across your workforce:
Standard Sizing Measurement Procedure:
- Measure Hand Circumference:
- Wrap measuring tape around the palm at its widest point (excluding thumb)
- Keep tape snug but not tight
- Record measurement in inches or centimeters
- Measure Hand Length:
- Measure from wrist crease to tip of middle finger
- Keep hand flat during measurement
- Use for verification of overall size
- Determine Glove Size:
- Use this standard conversion chart:
Hand Circumference (inches) | Hand Circumference (cm) | Glove Size |
---|---|---|
6-7 | 15-18 | XS (6) |
7-8 | 18-20 | S (7) |
8-9 | 20-23 | M (8) |
9-10 | 23-25 | L (9) |
10-11 | 25-28 | XL (10) |
11-12 | 28-30 | XXL (11) |
12+ | 30+ | XXXL (12) |
Fit Verification Checks:
- Fingertip Test: Fingertips should reach near the end of the glove fingers without stretching or excess material
- Pinch Test: Should be able to pinch small objects without excess material bunching
- Grip Test: Make a fist to ensure material doesn’t overly stretch or restrict movement
- Wrist Fit: Cuff should secure glove without being too tight or too loose
Specialized Sizing Considerations:
- Gender-Specific Sizing:
- Women generally have proportionally longer fingers relative to palm width
- Consider women-specific designs for workforces with significant female populations
- Coated vs. Uncoated Sizing:
- Coatings can affect the stretch and flexibility of gloves
- May need to adjust size up for heavily coated styles
- Task-Specific Considerations:
- Precision tasks may benefit from more fitted sizing
- Heavy-duty applications might require slightly larger sizing for comfort during extended wear
Implementing an Effective Sizing Program:
- Sizing Kits and Trials:
- Request sizing samples from manufacturers
- Allow workers to test different sizes during actual work tasks
- Collect feedback on comfort, dexterity, and fatigue
- Size Verification Process:
- Train safety personnel on proper measurement techniques
- Document individual worker sizes for consistent reordering
- Periodically verify sizes as work tasks or workforce changes
- Size Identification Systems:
- Use color-coded cuffs or labels for easy size identification
- Consider departmental color schemes for simplified distribution
- Implement clear size marking on storage containers
- Custom Sizing Options:
- For workforce populations with atypical size distributions
- For specialized applications requiring non-standard proportions
- Usually requires higher minimum order quantities
“The most protective glove provides no value if workers remove it due to poor fit,” notes a safety manager from a manufacturing facility. “We’ve found that investing time in proper sizing significantly increases compliance and reduces hand injuries.”
Qingdao Snell offers comprehensive sizing programs including measurement guides, sizing samples, and consulting services to help organizations implement effective glove sizing initiatives. Their sizing specialists can work with safety managers to develop custom sizing solutions for workforces with unique requirements.
How do environmental conditions affect HPPE glove performance?
Environmental conditions can significantly impact the performance, durability, and protection level of HPPE protective gloves. Understanding these effects helps in selecting appropriate gloves for specific work environments and implementing proper usage protocols.
Temperature Effects on HPPE Gloves:
Temperature Range | Effects on HPPE Material | Effects on Coatings | Recommended Adaptations |
---|---|---|---|
Extreme Cold(-30°C to 0°C) | Minimal effect on HPPE fibersMaintains flexibilityCut resistance remains stable | Nitrile becomes stifferPU remains relatively flexibleLatex becomes brittle | Select PU coatings for cold environmentsConsider thermal lined versionsSize up to accommodate liners |
Standard Range(0°C to 30°C) | Optimal performance rangeFull flexibility and dexteritySpecified protection levels maintained | All coatings perform as designedGrip properties maintainedDurability as specified | Standard selection based on applicationRegular replacement scheduleNormal care protocols |
High Heat(30°C to 100°C) | HPPE begins to soften above 70°CProlonged exposure may affect cut resistanceNot suitable for molten material | PU softens at elevated temperaturesNitrile more heat-stableLatex degrades with prolonged heat | Select nitrile for hot environmentsConsider specialized heat-resistant glovesImplement more frequent replacement |
Extreme Heat(Above 100°C) | Melts at approximately 145°CNot suitable for direct flame or extreme heatCan transfer heat to skin | Most coatings degrade rapidlyProtection compromisedPotential for melting | HPPE not recommendedUse specialized heat-resistant glovesConsider multi-layer protection |
Moisture and Liquid Exposure:
- HPPE Material Response:
- Hydrophobic properties resist water absorption
- Maintains cut resistance when wet
- Does not become heavier or swell when exposed to water
- Dries relatively quickly compared to natural fibers
- Coating Performance Changes:
- Nitrile maintains grip in wet/oily conditions
- PU performance degrades somewhat in wet environments
- Latex excels in wet conditions but fails with oils
- Uncoated areas allow moisture to reach skin
- Adaptations for Wet Environments:
- Select fully coated styles for consistent liquid exposure
- Choose sandy nitrile for oily/wet grip requirements
- Implement rotation program for high-moisture environments
- Consider drainage features for extensive water exposure
UV and Weather Exposure:
- Degradation Mechanisms:
- UV radiation gradually breaks down polymer bonds
- Repeated wet/dry cycles can stress material interfaces
- Temperature fluctuations may affect coating adhesion
- Atmospheric contaminants can accelerate degradation
- Observable Effects:
- Coating becomes tacky or brittle
- Color fading indicates polymer degradation
- Reduced flexibility and increased stiffness
- Premature failure at stress points
- Mitigation Strategies:
- Store gloves away from direct sunlight
- Implement more frequent replacement schedules for outdoor use
- Select UV-stabilized versions for outdoor applications
- Consider darker colors which typically have better UV resistance
Chemical Environment Considerations:
- Common Industrial Chemicals:
- Petroleum products: Nitrile coating recommended
- Alcohols: Most coatings provide short-term resistance
- Acids/Bases: Limited resistance, specialized gloves needed for direct exposure
- Solvents: Generally degrade coatings, verify compatibility
- Airborne Contaminants:
- Dust particles accelerate abrasion wear
- Oil mist may affect some coating types
- Cement dust creates alkaline environment
- Metal particles may embed in coatings
- Performance Maintenance:
- Regular cleaning removes damaging contaminants
- Proper storage prevents chemical absorption
- Inspection protocols identify chemical damage
- Training on chemical compatibility limitations
Understanding these environmental factors allows for more effective glove selection, appropriate replacement schedules, and proper storage practices. For environments with multiple or extreme conditions, consult with manufacturers like Qingdao Snell who can recommend specialized solutions or custom designs to address your specific environmental challenges.