OEM Work Gloves Factory: Ultimate Guide to Oil Cut Resistant Gloves Bulk in 2025
April 13, 2025
Share This Article
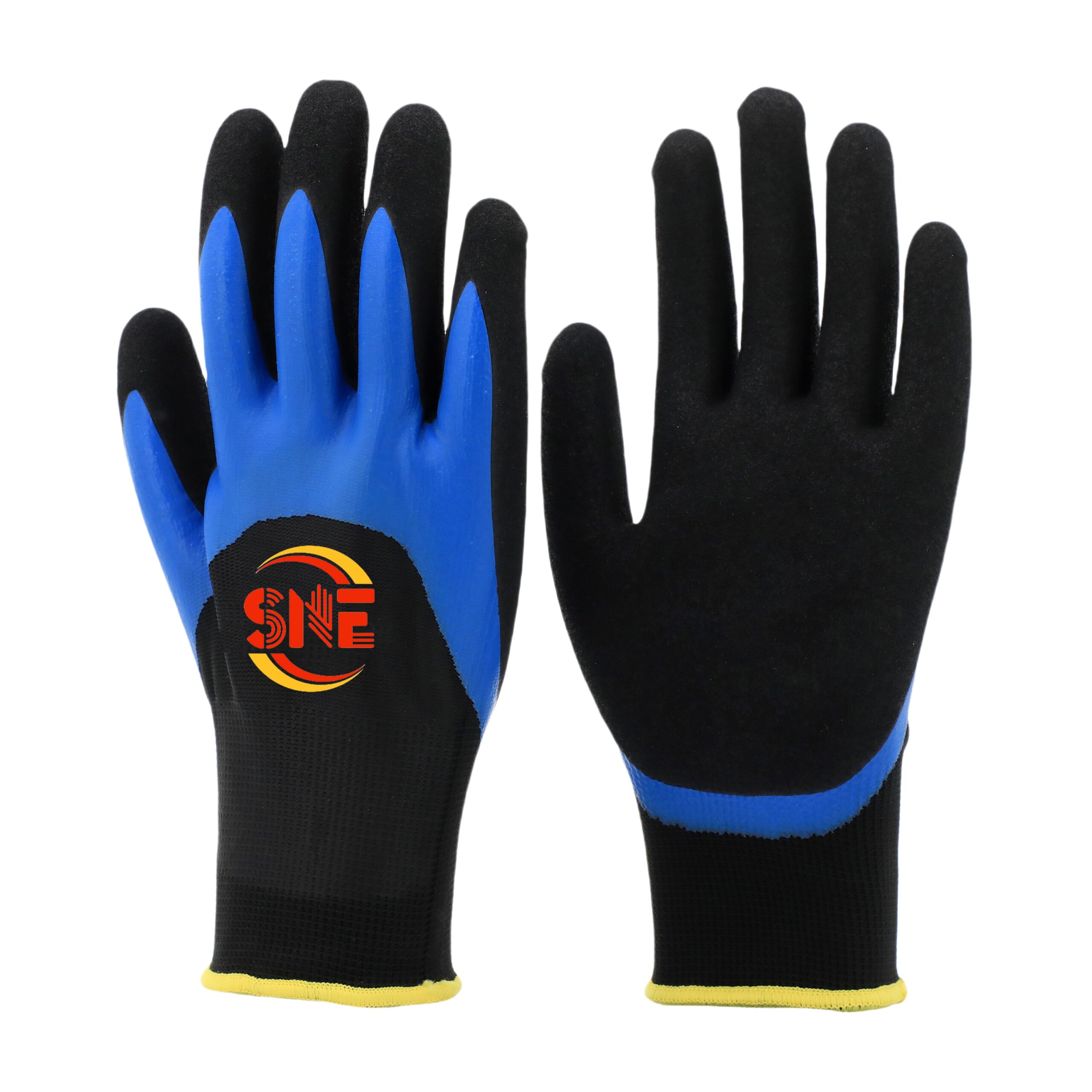
In today’s industrial landscape, worker safety remains a top priority for businesses across various sectors. Among the most critical protective equipment are high-quality oil cut resistant gloves, which provide essential protection against sharp objects, chemicals, and slippery conditions. This comprehensive guide explores everything you need to know about sourcing oil cut resistant gloves in bulk from OEM work gloves factories in 2025, helping you make informed decisions for your business’s safety needs.
What Are Oil Cut Resistant Gloves?
Oil cut resistant gloves represent a specialized category of personal protective equipment designed to address two significant workplace hazards simultaneously: sharp objects and oily substances. These innovative gloves combine cut-resistant materials with oil-resistant coatings to create a versatile safety solution.
The foundation of these gloves typically consists of engineered yarns like HPPE (High-Performance Polyethylene), Kevlar, or composite materials that provide exceptional resistance to cuts and punctures. These base materials are then enhanced with specialized coatings—most commonly nitrile, polyurethane (PU), or latex—that deliver oil resistance, chemical protection, and improved grip in slippery conditions.
What sets oil cut resistant gloves apart from standard work gloves is this dual-protection capability. The cut-resistant fibers prevent lacerations from sharp tools, metal edges, glass, and other hazards, while the oil-resistant coating prevents penetration of oils, greases, and many industrial fluids that might otherwise compromise grip or expose skin to harmful substances.
These gloves are categorized according to standardized cut resistance levels, typically following the ANSI/ISEA 105 or EN 388 standards. The ANSI scale ranges from A1 (lowest) to A9 (highest) cut resistance, while EN 388 uses a scale from 1 to 5 (with 5 being the highest protection). Higher-rated gloves contain more advanced materials or denser construction to withstand greater cutting forces.
Modern oil cut resistant gloves also incorporate ergonomic design features such as seamless knit construction, breathable materials, and anatomical shapes that enhance dexterity and reduce hand fatigue during prolonged use. This makes them suitable for precision work even while providing substantial protection.
How to Choose the Best Oil Cut Resistant Gloves for Your Business?
Selecting the optimal oil cut resistant gloves for your specific business requirements involves careful consideration of multiple factors. This decision directly impacts both worker safety and operational efficiency, making it crucial to evaluate various aspects before committing to a bulk purchase.
Understanding Your Industry-Specific Requirements
Different industries face unique hazards that demand specialized glove features:
- Automotive Manufacturing: Workers handling sharp metal components and engine parts need gloves with high cut resistance (typically ANSI A4-A6) combined with oil grip for handling lubricated parts.
- Oil & Gas Industry: Environments with crude oil exposure require superior chemical resistance alongside cut protection, often necessitating fully nitrile-coated gloves with extended cuffs.
- Food Processing: This sector requires gloves that not only protect against cuts from knives and processing equipment but must also comply with food safety regulations and be detectable by metal detectors.
- Glass Handling: Extremely high cut resistance (ANSI A7-A9) is essential, along with palm coatings that maintain grip on smooth, potentially oily glass surfaces.
Assessing Cut Resistance Levels
When evaluating cut resistance, consider:
- Material Composition: HPPE provides excellent cut resistance with comfort, Kevlar offers heat resistance alongside cut protection, while composite materials containing steel or glass fibers deliver the highest levels of protection.
- Protection Standards: Verify that gloves are certified according to recognized standards like ANSI/ISEA 105 or EN 388. Request test reports from manufacturers to confirm performance claims.
- Application Requirements: Match the cut level to the specific hazards present—lightweight protection for minimal risks, medium protection for general maintenance, and maximum protection for high-hazard environments like metal stamping or glass handling.
Coating Types and Their Applications
The coating material significantly impacts performance in oily conditions:
- Nitrile Coatings: Provide excellent resistance to oils, fuels, and many chemicals. Their durability makes them ideal for automotive, manufacturing, and chemical industries. Nitrile-coated gloves offer outstanding puncture resistance as well.
- Polyurethane (PU) Coatings: Deliver superior dexterity and tactile sensitivity while providing good oil resistance. These are preferable for precision assembly tasks involving oily components.
- Sandy or Foam Nitrile: These textured coatings enhance grip in extremely slippery conditions by channeling away oils from the contact surface, making them excellent for work with lubricants and cutting fluids.
Comfort and Ergonomic Considerations
Comfort directly affects compliance with safety protocols. Key comfort factors include:
- Breathability: Gloves with open backs or moisture-wicking liners help reduce hand perspiration during extended wear.
- Sizing Options: Proper fit is crucial—too tight restricts movement and causes fatigue, while too loose compromises dexterity and increases hazard risks.
- Liner Materials: Engineered yarn blends can enhance comfort without sacrificing protection. Some manufacturers incorporate materials like nylon or spandex to improve stretch and fit.
- Seamless Construction: Elimination of seams reduces irritation and pressure points during prolonged wear.
Price vs. Quality Analysis
When evaluating cost considerations:
- Total Cost of Ownership: Lower-quality gloves may save money initially but require more frequent replacement. Calculate cost per use rather than just purchase price.
- Durability Factors: Examine reinforcement in high-wear areas, coating thickness, and base material density to assess likely service life.
- Volume Discounts: Bulk purchasing directly from OEM manufacturers typically provides significant cost advantages, especially when ordering container quantities.
Qingdao Snell Protective Products Co., Ltd. offers an excellent balance of quality and cost-effectiveness in their oil cut resistant glove lines. With ISO9001 and CE certifications, their products meet international standards while remaining competitively priced for bulk orders.
Where to Buy Oil Cut Resistant Gloves in Bulk?
Sourcing oil cut resistant gloves in bulk requires identifying reliable supply channels that offer both quality assurance and competitive pricing. In today’s global marketplace, businesses have multiple options for procuring these essential safety items.
Direct OEM Manufacturers
Purchasing directly from Original Equipment Manufacturers (OEMs) offers several distinct advantages:
- Cost Efficiency: Eliminating intermediaries can reduce per-unit costs by 15-30%, especially for large orders.
- Customization Options: OEMs can tailor gloves to specific requirements, including custom sizes, colors, and features.
- Quality Control Access: Direct relationships with manufacturers allow buyers to request specific testing or inspection protocols.
- Consistent Supply: Established manufacturers maintain dedicated production capacity for regular customers, reducing supply disruptions.
Qingdao Snell Protective Products Co., Ltd. exemplifies the benefits of working with a specialized OEM manufacturer. With over a decade of expertise in protective gloves, Snell operates two factories with six production lines dedicated to high-performance safety gloves. Their direct-from-factory model eliminates middlemen, resulting in more competitive pricing while maintaining ISO9001 and CE certified quality standards.
Online B2B Marketplaces
Global B2B platforms connect buyers with multiple suppliers:
- Alibaba/AliExpress: Hosts thousands of work glove manufacturers with varied minimum order quantities (MOQs) and price points.
- Global Sources: Focuses on verified suppliers with third-party quality assessments.
- Made-in-China: Specializes in connecting international buyers with Chinese manufacturers.
These platforms offer convenience but require careful verification of supplier credentials and product testing certificates. Request sample products before committing to large orders through these channels.
Industrial Safety Distributors
Specialized distributors offer advantages for businesses requiring smaller quantities or immediate delivery:
- Grainger, Uline, MSC Industrial: Stock comprehensive ranges of safety gloves with express shipping options.
- Regional Safety Suppliers: Often provide personalized service and technical guidance for local businesses.
- Industry-Specific Distributors: Companies focusing on particular sectors (e.g., food processing or automotive) may offer specialized knowledge about appropriate glove selections.
While distributors typically charge premium prices compared to direct manufacturing sources, they add value through inventory management, technical support, and flexible ordering quantities.
Trade Shows and Industry Exhibitions
These events provide opportunities to:
- Evaluate products hands-on before purchasing
- Compare multiple suppliers efficiently
- Negotiate favorable terms for bulk orders
- Build relationships with manufacturer representatives
- Discover innovative products not yet widely marketed
Major safety equipment exhibitions such as the A+A Safety Show in Germany, the National Safety Council Expo in the US, and China International Occupational Safety & Health Exhibition showcase the latest developments in protective gloves.
Factors to Consider When Selecting a Supplier
When evaluating potential suppliers for bulk purchases, assess:
- Production Capacity: Ensure the manufacturer can fulfill large orders consistently and meet delivery timelines.
- Quality Certifications: Verify ISO 9001 certification for quality management systems and product-specific certifications like EN 388 or ANSI/ISEA 105.
- Minimum Order Quantities: These can range from 500 pairs with some distributors to 3,000-20,000 pairs with direct manufacturers like Qingdao Snell.
- Sample Availability: Reputable suppliers provide samples for evaluation before large orders.
- Communication Responsiveness: Test how quickly and comprehensively potential suppliers respond to inquiries—this often indicates their service level after purchase.
Oil Cut Resistant Gloves Manufacturer in China
China has established itself as the global leader in protective glove manufacturing, combining advanced production technologies with cost-efficient operations. Understanding the Chinese manufacturing landscape helps buyers make informed sourcing decisions for oil cut resistant gloves.
Major Manufacturing Regions
Chinese glove production is concentrated in specific industrial clusters:
- Shandong Province: Home to major manufacturers like Qingdao Snell Protective Products Co., Ltd., this region specializes in high-performance cut-resistant gloves with advanced coatings. The area benefits from proximity to major ports and a robust supply chain for specialized yarns and coating materials.
- Guangdong Province: Companies in this southern manufacturing hub focus on gloves requiring sophisticated manufacturing processes, including multi-layer designs and specialized grip patterns for oily environments.
- Zhejiang Province: Known for innovation in textile technologies, manufacturers here often lead in developing new cut-resistant fibers and coating applications.
- Jiangsu Province: Specializes in higher-end technical gloves with precision coating applications and ergonomic design features.
These regional specializations have developed through decades of industry concentration, creating ecosystems of component suppliers, technical expertise, and logistics infrastructure that enhance manufacturing efficiency.
Technological Capabilities
Modern Chinese manufacturers have invested heavily in advanced production technologies:
- Automated Knitting Systems: Computer-controlled machines produce seamless liners with precise blends of cut-resistant fibers, ensuring consistent protection levels.
- Advanced Coating Processes: Specialized equipment applies precisely controlled layers of nitrile, polyurethane, or latex coatings, optimizing both protection and dexterity.
- Quality Testing Facilities: Leading manufacturers maintain in-house laboratories equipped with cut resistance testers, abrasion testing machines, and chemical resistance evaluation equipment.
- Research & Development Capabilities: Top-tier manufacturers like Qingdao Snell invest in ongoing material research and ergonomic design improvements to enhance both protection and comfort.
These technological investments have elevated Chinese manufacturing quality while maintaining competitive pricing through production efficiencies.
Quality Control Standards
Reputable Chinese manufacturers adhere to rigorous quality management systems:
- ISO 9001 Certification: Establishes standardized quality management processes across all production stages.
- EN 388 and ANSI Testing: Validated performance testing for cut resistance, puncture resistance, abrasion resistance, and tear strength.
- In-Line Inspection Protocols: Systematic quality checks throughout the production process, from raw material verification to finished product testing.
- Third-Party Testing: Independent laboratory verification of performance claims and compliance with international standards.
Qingdao Snell exemplifies this commitment to quality with comprehensive certification and testing protocols. Their production facilities in Gaomi and Nantong implement systematic quality management systems backed by both ISO 9001 and CE certifications, ensuring consistent product performance for bulk orders.
Competitive Advantages of Chinese Manufacturers
Several factors contribute to China’s dominance in oil cut resistant glove production:
- Materials Ecosystem: Proximity to suppliers of specialized yarns, coating chemicals, and other components reduces costs and improves supply chain reliability.
- Scale Economies: High-volume production enables investment in specialized equipment that improves both quality and efficiency.
- Workforce Expertise: Decades of manufacturing experience have created a skilled labor pool with specialized knowledge in glove production techniques.
- Export Infrastructure: Well-developed logistics networks facilitate efficient international shipping, with established routes to major markets worldwide.
- Cost Efficiency: Despite rising labor costs, operational efficiencies and automation investments help maintain competitive pricing.
When considering Chinese manufacturers, it’s important to distinguish between different tiers of producers. Premium manufacturers like Qingdao Snell maintain higher quality standards and offer more consistent production capabilities, which justifies their slightly higher pricing compared to smaller operations with less sophisticated quality systems.
What to Look for in a Reliable OEM Work Gloves Factory?
Identifying a dependable manufacturing partner for your oil cut resistant gloves requires thorough evaluation across multiple dimensions. This systematic assessment helps ensure you establish a relationship with a factory capable of consistently meeting your quality, volume, and timing requirements.
Manufacturing Capabilities and Facilities
A comprehensive understanding of a factory’s production infrastructure provides insight into their ability to fulfill your requirements:
- Production Capacity: Verify the number of production lines, daily output capacity, and ability to scale during peak demand periods. Factories with multiple production lines like Qingdao Snell’s six dedicated lines can better accommodate large bulk orders while maintaining consistent delivery schedules.
- Equipment Technology: Assess the manufacturer’s investment in modern knitting machines, coating application systems, and curing equipment. Advanced machinery produces more consistent products with fewer defects.
- Facility Certifications: Look for ISO 9001:2015 certification as a minimum standard, indicating that the factory maintains recognized quality management systems. Additional certifications relevant to specific industries (such as food processing or automotive) provide further assurance of specialized capabilities.
- Product Testing Infrastructure: On-site testing laboratories demonstrate commitment to quality control and allow manufacturers to verify performance standards before products leave the facility. Tests should include cut resistance, abrasion resistance, and coating integrity verification.
- Research & Development Capabilities: Manufacturers with dedicated R&D departments can help develop customized solutions for specific applications and tend to incorporate more innovative materials and techniques into their products.
Quality Assurance Processes
Reliable manufacturers implement comprehensive quality control systems throughout the production process:
- Raw Material Inspection: Verification of incoming materials against specifications, including fiber composition, yarn tensile strength, and coating chemical compliance.
- In-Process Inspections: Regular checks during manufacturing to identify and correct issues before they affect finished products. This includes monitoring knitting tension, coating application thickness, and curing parameters.
- Statistical Quality Control: Systematic sampling and testing of production batches to ensure consistent performance across large production runs.
- Finished Product Testing: Comprehensive evaluation of completed gloves against performance standards, including physical testing of cut resistance, abrasion resistance, and grip performance.
- Documentation Systems: Detailed record-keeping that enables traceability from raw materials through production to final delivery, supporting quality verification and problem resolution.
Ethical Manufacturing Practices
Responsible sourcing requires verification of ethical business practices:
- Labor Conditions: Ensure the factory complies with local labor laws regarding working hours, compensation, and workplace safety. Some manufacturers maintain certifications like BSCI (Business Social Compliance Initiative) or WRAP (Worldwide Responsible Accredited Production).
- Environmental Compliance: Verify adherence to environmental regulations, including proper handling of coating chemicals, waste management protocols, and energy efficiency measures.
- Transparency Policies: Factories that welcome client visits and third-party audits demonstrate commitment to accountable business practices.
- Corporate Social Responsibility: Some manufacturers like Qingdao Snell implement additional programs supporting worker welfare, community engagement, or environmental sustainability that indicate a broader commitment to ethical business conduct.
Communication and Customer Service
Effective partnership requires strong communication infrastructure:
- Technical Support Capabilities: Access to knowledgeable staff who can advise on appropriate glove specifications for specific applications.
- Response Timeliness: Evaluate how quickly the factory responds to inquiries, sample requests, and technical questions.
- Language Proficiency: Ensure the manufacturer has staff with sufficient English proficiency (or your preferred language) to prevent misunderstandings about technical requirements.
- Documentation Clarity: Detailed product specifications, test reports, and certification documents provided in accessible formats.
- Problem Resolution Processes: Established procedures for addressing quality issues or delivery challenges that may arise.
Companies like Qingdao Snell demonstrate their commitment to customer service through dedicated account managers who provide personalized support throughout the ordering process and beyond, ensuring smooth communication even across language and time zone differences.
MOQ Considerations When Ordering Oil Cut Resistant Gloves in Bulk
Understanding minimum order quantity (MOQ) requirements is essential when planning bulk purchases of oil cut resistant gloves. These requirements vary significantly based on manufacturer policies, production economics, and the specific glove specifications requested. Navigating these considerations effectively can help optimize your purchasing strategy.
Standard MOQ Ranges by Manufacturer Type
Different supplier categories maintain distinct MOQ policies that reflect their business models:
- Large OEM Manufacturers: Primary producers like Qingdao Snell typically require MOQs ranging from 3,000 to 20,000 pairs per order, depending on glove specifications. These higher minimums reflect the economics of dedicated production runs and specialized material sourcing.
- Mid-Sized Manufacturers: Regional producers often accept orders between 1,000-5,000 pairs, offering a middle ground for medium-volume buyers.
- Distributors and Wholesalers: These intermediaries purchase in large volumes from manufacturers and can often accommodate smaller orders of 200-500 pairs, though at higher per-unit costs.
- Retail Supply Companies: Businesses purchasing for immediate operational needs rather than resale can often buy in quantities as low as 10-100 pairs through industrial supply companies, though at significantly higher prices.
Factors Affecting MOQ Requirements
Several variables influence the minimum quantities manufacturers will accept:
- Customization Level: Standard glove designs have lower MOQs compared to customized products. Adding features like custom colors, special coatings, or proprietary designs typically increases minimum quantities significantly.
- Material Specifications: Gloves utilizing specialized cut-resistant materials or advanced coating formulations often require higher MOQs due to material sourcing economics and production setup requirements.
- Size Distribution: Manufacturers prefer balanced size assortments. Orders with unusual size distributions (e.g., predominantly small or extra-large sizes) may face higher minimums or surcharges.
- Seasonal Factors: During peak production periods, manufacturers may increase MOQs to optimize their production schedules and focus on larger, more profitable orders.
- Relationship Status: Established customers with regular ordering patterns sometimes negotiate reduced MOQs based on their annual purchase volume and predictable ordering schedules.
Strategies for Managing MOQ Constraints
Businesses can employ several approaches to work effectively within MOQ limitations:
- Consolidated Purchasing: Combine requirements across multiple departments or facilities to meet higher MOQs while distributing inventory appropriately.
- Staggered Delivery Arrangements: Negotiate production of the full MOQ with phased deliveries to manage inventory levels and cash flow more effectively.
- Mixed-Model Orders: Some manufacturers allow combined orders of different glove models to reach total MOQ thresholds, providing greater flexibility in product assortment.
- Distributor Partnerships: Work with distributors who consolidate requirements from multiple end users to meet manufacturer MOQs, though this adds a layer of cost.
- Long-Term Agreements: Commit to annual volumes with scheduled releases, potentially securing lower MOQs for individual shipments while guaranteeing the manufacturer’s total volume.
Cost Implications of MOQ Decisions
MOQ choices significantly impact the economics of glove procurement:
Order Quantity | Typical Price Premium | Inventory Carrying Costs | Supply Security |
---|---|---|---|
Below 1,000 pairs | +35-50% above base price | Low | Vulnerable to stockouts |
1,000-5,000 pairs | +15-25% above base price | Moderate | Adequate for most operations |
5,000-10,000 pairs | +5-10% above base price | Moderate-High | Good protection against disruptions |
10,000+ pairs | Base price | High | Excellent supply security |
When working with manufacturers like Qingdao Snell that have MOQs in the 3,000-20,000 pair range, businesses benefit from significant per-unit cost advantages. While these quantities require greater upfront investment and storage capacity, the 30-40% cost savings compared to small-quantity purchases often justify the higher initial outlay for businesses with steady, predictable usage patterns.
How to Customize Oil Cut Resistant Gloves with Your Logo and Branding?
Customized oil cut resistant gloves offer multiple advantages beyond basic hand protection. They reinforce brand identity, promote safety culture, and can even assist with inventory management. Understanding the customization options and processes helps businesses maximize these benefits while working effectively with manufacturers.
Available Customization Options
Modern glove manufacturers offer various branding and personalization techniques:
- Logo Application Methods:
- Screen Printing: The most common and cost-effective method for adding logos to the back of gloves, offering good durability and color options.
- Heat Transfer: Provides more detailed imagery with multiple colors but at a higher cost per unit.
- Embossing/Debossing: Creates raised or recessed designs in the coating material, offering subtle but durable branding.
- Custom-Colored Materials: Some manufacturers can incorporate colored yarns or tinted coatings to match corporate color schemes.
- Customizable Elements:
- Back-of-Hand Area: The primary location for logos and text, offering the largest printable surface.
- Cuff Design: Custom lengths, colors, or printed information on fabric cuffs.
- Packaging: Branded poly bags, boxes, or dispensing systems for the gloves.
- Hang Tags: Custom information cards attached to gloves with product information or safety instructions.
- Safety Enhancement Options:
- High-Visibility Elements: Fluorescent colors or reflective materials incorporated into the design.
- Color-Coding Systems: Different colors for size identification or department designation.
- Embedded RFID Tags: Advanced tracking capabilities for inventory management or restricted area access control.
Working with Manufacturers on Custom Designs
Effective collaboration with manufacturers ensures successful customization projects:
- Design Preparation:
- Provide vector-format logos (.ai, .eps, or high-resolution .pdf files) for optimal reproduction quality.
- Specify exact Pantone colors for consistent brand representation.
- Consider the surface texture and color when designing—simpler logos with fewer colors typically reproduce better on glove materials.
- Sampling Process:
- Request pre-production samples to verify appearance and positioning.
- Allow 2-4 weeks for initial sample development, depending on complexity.
- Approve samples in writing before proceeding to full production.
- Technical Considerations:
- Printing area limitations (typically 3″×3″ maximum on most gloves).
- Color restrictions based on base material (dark gloves may require underbase printing).
- Durability expectations (prints may show wear over time with heavy use).
Cost Implications of Customization
Customization affects overall project economics in several ways:
Customization Type | Typical Cost Addition | Minimum Order Impact | Production Time Extension |
---|---|---|---|
Basic one-color logo | 0.15−0.15-0.15−0.30 per pair | Usually doubles standard MOQ | +7-10 days |
Multi-color logo | 0.30−0.30-0.30−0.60 per pair | Often 2-3× standard MOQ | +10-14 days |
Custom cuff colors | 0.10−0.10-0.10−0.25 per pair | Typically 3× standard MOQ | +14-21 days |
Full custom design | 0.75−0.75-0.75−2.00 per pair | 5× standard MOQ or higher | +21-30 days |
Qingdao Snell offers customization services with MOQs starting at 3,000 pairs for basic logo printing and 5,000 pairs for more complex customization options. Their dedicated design team works with clients to optimize logo reproduction while maintaining the performance characteristics of their oil cut resistant gloves.
Case Study: Successful Branding Implementation
A North American oil and gas company partnered with Qingdao Snell to develop custom-branded oil cut resistant gloves that addressed specific worksite hazards while reinforcing safety protocols through visual branding.
The customization included:
- Company logo screen-printed on the back of the hand
- Safety reminder message printed on the cuff
- Color-coded cuffs indicating cut-resistance levels
- Custom packaging with QR codes linking to training videos
Results included:
- 23% increase in proper glove usage compliance
- Improved inventory management through visual identification
- Enhanced corporate identity at multi-company worksites
- Reduced loss/theft due to distinctive appearance
This implementation demonstrates how strategic customization can deliver benefits beyond simple branding, contributing to overall safety program effectiveness while maintaining the essential protective qualities of the oil cut resistant gloves.
What Are the Most Durable Materials for Oil Cut Resistant Gloves?
The durability and performance of oil cut resistant gloves depend largely on their material composition. Understanding these materials helps procurement specialists select gloves that deliver optimal protection and longevity for specific work environments.
Core Cut-Resistant Materials
The foundation of any cut resistant glove is its liner material, which provides the primary defense against lacerations:
- HPPE (High-Performance Polyethylene):
- Industry-leading cut resistance with exceptional comfort
- 10-15 times stronger than steel on a weight-for-weight basis
- Excellent durability with repeated washing
- Resistant to many chemicals and UV degradation
- Commonly used in ANSI cut levels A2-A7
- Para-aramid Fibers (Kevlar® and similar materials):
- Outstanding cut and heat resistance (functional up to 800°F/427°C)
- Excellent tensile strength and durability
- More rigid than HPPE, which affects dexterity
- Degrades with exposure to UV light and certain chemicals
- Common in applications requiring both cut and heat protection
- Composite Materials:
- Engineered blends incorporating steel, fiberglass, or basalt fibers
- Highest cut resistance (typically ANSI A7-A9)
- Exceptionally durable in harsh environments
- Heavier and less flexible than pure synthetic options
- Often used in metal stamping, glass handling, and recycling industries
- Steel or Fiberglass Core Yarns:
- Wrapped steel or fiberglass filaments provide extreme cut resistance
- Significantly heavier than synthetic alternatives
- Limited flexibility impacts fine manipulation tasks
- Unmatched durability in high-abrasion environments
- Common in meat processing and metal fabrication
Oil-Resistant Coating Technologies
The coating material determines oil resistance, grip performance, and often the overall durability of the glove:
- Nitrile Coatings:
- Superior resistance to oils, fuels, and many industrial chemicals
- Excellent puncture resistance compared to other polymers
- Maintains flexibility in both hot and cold environments
- Available in various formulations from ultra-thin to heavy-duty
- Typical lifespan 30-50% longer than PU coatings in oily environments
- Polyurethane (PU) Coatings:
- Excellent abrasion resistance with superior tactile sensitivity
- Good oil resistance with exceptional dexterity
- Breathable characteristics reduce hand fatigue
- Less chemical resistance than nitrile in harsh environments
- Preferable for precision work requiring finger dexterity
- Sandy/Foam Nitrile Finishes:
- Microscopic surface texture channels away oils for enhanced wet grip
- Increased durability in abrasive applications
- Greater coating thickness extends service life
- Reduced tactile sensitivity compared to smooth coatings
- Ideal for handling small, oily components
- Bi-Polymer and Hybrid Coatings:
- Combines benefits of different polymers (often nitrile and PU)
- Enhanced durability while maintaining dexterity
- Specialized formulations for extreme temperature environments
- Premium price point reflects advanced technology
- Increasingly popular for demanding multi-hazard environments
Material Performance Comparison
This comparison highlights the relative performance of common material combinations for oil cut resistant gloves:
Material Combination | Cut Resistance | Oil Resistance | Durability | Dexterity | Typical Applications |
---|---|---|---|---|---|
HPPE + Thin Nitrile | A3-A5 | Good | Good | Excellent | Precision assembly with oils |
HPPE + Foam Nitrile | A4-A6 | Excellent | Very Good | Good | General maintenance, automotive |
Kevlar + Nitrile | A3-A5 | Good | Excellent | Good | Hot components with oils |
HPPE/Steel + Heavy Nitrile | A7-A9 | Excellent | Excellent | Fair | Metal stamping, recycling |
Composite + Bi-polymer | A6-A9 | Excellent | Excellent | Good | Oil/gas industry, heavy machinery |
Qingdao Snell has developed proprietary material blends that optimize the balance between protection and comfort. Their high-end oil cut resistant gloves incorporate advanced HPPE composite liners with specialized nitrile formulations engineered specifically for extended durability in oil-contaminated environments.
Innovations in Material Technology
Recent advancements have introduced new materials that further enhance glove performance:
- Microencapsulated Cooling Agents: Materials that provide cooling effects during wear, reducing hand fatigue in hot environments.
- Biodegradable Cut-Resistant Fibers: Environmentally friendly alternatives that maintain protection while reducing end-of-life environmental impact.
- Impact-Resistant Materials: TPR (Thermoplastic Rubber) reinforcements combined with cut-resistant liners and oil-resistant coatings for comprehensive hand protection.
- Antimicrobial Treatments: Additives that inhibit bacterial growth during extended wear, particularly valuable in humid work environments.
- Touchscreen-Compatible Fibers: Conductive materials incorporated into fingertips allowing device operation without glove removal.
These innovations demonstrate the ongoing evolution of glove materials to address multiple workplace hazards simultaneously while enhancing comfort and functionality.
How to Ensure Quality Control When Ordering Oil Cut Resistant Gloves in Bulk
Implementing effective quality control measures ensures that bulk purchases of oil cut resistant gloves consistently meet performance requirements and safety standards. A systematic approach to quality verification protects both worker safety and procurement investments.
Establishing Clear Specifications
Comprehensive product specifications form the foundation of effective quality control:
- Performance Requirements:
- Specific cut resistance level (ANSI/ISEA 105 or EN 388 rating)
- Oil resistance standards (penetration resistance, degradation limits)
- Grip performance metrics (coefficient of friction in oily conditions)
- Abrasion resistance expectations (cycles to failure)
- Material Specifications:
- Base liner composition and weight
- Coating type, thickness, and coverage area
- Specific chemical resistance requirements
- Allowable tolerance ranges for key measurements
- Ergonomic Criteria:
- Sizing accuracy across the size range
- Dexterity requirements (fine manipulation capability)
- Weight limitations
- Comfort factors (breathability, flexibility)
- Appearance Standards:
- Color consistency requirements
- Acceptable cosmetic variation limits
- Logo placement precision
- Packaging presentation specifications
Documenting these requirements in detail provides clear benchmarks against which quality can be measured throughout the procurement process.
Pre-Production Sampling and Testing
Thorough evaluation before full production prevents large-scale quality issues:
- Sample Evaluation Process:
- Request pre-production samples representing actual production materials
- Obtain multiple pieces to assess consistency
- Compare against specification requirements
- Document findings with photographs and measurements
- Laboratory Testing Protocols:
- Third-party verification of cut resistance claims
- Oil penetration resistance testing
- Abrasion resistance evaluation
- Tensile strength and seam integrity assessment
- Field Testing Procedures:
- Deploy samples to actual work environments
- Gather structured feedback from end-users
- Document performance in real-world conditions
- Compare results against laboratory findings
Working with manufacturers like Qingdao Snell that maintain comprehensive in-house testing facilities expedites this process. Their laboratory can perform standardized tests according to international protocols, providing documented evidence of performance before production begins.
In-Production Quality Monitoring
Ongoing verification during manufacturing ensures consistency across large production runs:
- Statistical Process Control:
- Regular sampling throughout production for measurement and testing
- Tracking of key quality indicators against control limits
- Documentation of process variables affecting quality
- Immediate corrective action when variations are detected
- Critical Control Points:
- Material receiving inspection (fiber composition, yarn quality)
- Knitting tension monitoring
- Coating application thickness verification
- Curing temperature and duration validation
- Final dimensional inspection
- Inspection Protocols:
- AQL (Acceptable Quality Level) standards appropriate for safety equipment
- Tiered inspection levels (normal, tightened, or reduced) based on quality history
- Clear defect classification (critical, major, minor)
- Documentation requirements for inspection records
Pre-Shipment Verification
Final quality assessment before dispatch provides the last opportunity to catch defects:
- Final Inspection Elements:
- Visual inspection of appearance and workmanship
- Dimensional verification across size range
- Performance testing on production samples
- Packaging and labeling accuracy
- Quantity verification
- Documentation Requirements:
- Test reports demonstrating compliance with specifications
- Material certificates confirming composition
- Inspection reports with statistical findings
- Certificate of Compliance or Conformity
- Shipping and packing list accuracy
- Issue Resolution Procedures:
- Clear protocols for addressing identified issues
- Decision criteria for acceptance, rework, or rejection
- Documentation of corrective actions implemented
- Verification of effectiveness before approval
Supplier Quality Management
Building quality partnerships enhances long-term product consistency:
- Supplier Qualification Process:
- Initial capability assessment
- Quality management system evaluation
- Process audit of manufacturing facilities
- Review of quality history with similar products
- Performance Metrics Tracking:
- Defect rates per shipment
- On-time delivery performance
- Responsiveness to quality issues
- Continuous improvement initiatives
- Collaborative Improvement Approaches:
- Regular quality reviews with suppliers
- Joint problem-solving for recurring issues
- Shared investment in quality improvements
- Recognition for exceptional quality performance
Qingdao Snell’s quality management systems exemplify best practices in this area. Their ISO 9001 certified processes incorporate comprehensive documentation, statistical quality control, and continuous improvement methodologies that ensure consistent product quality across large production volumes.