OEM Impact Resistant Gloves Factory: Complete Sourcing Guide in 2025
April 13, 2025
Share This Article
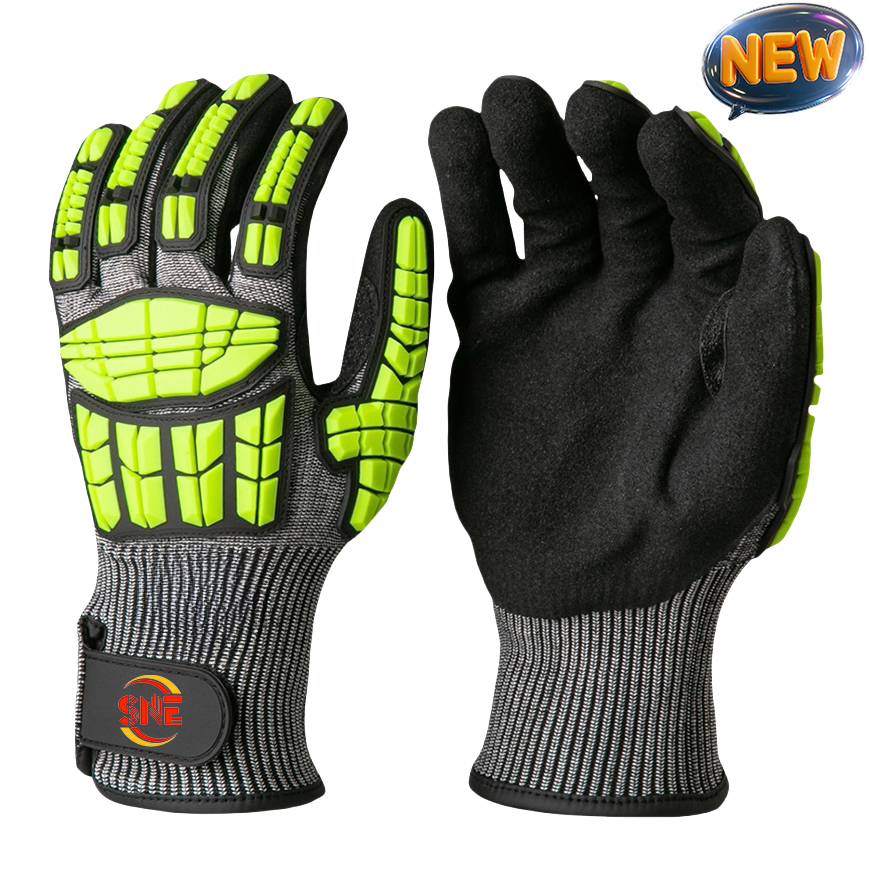
What Are Impact Resistant Gloves?
Impact resistant gloves represent a critical advancement in hand protection technology designed specifically to shield workers from one of the most common and potentially devastating workplace injuries – impact trauma. Unlike standard work gloves that primarily focus on cut resistance or general protection, impact resistant gloves incorporate specialized materials and design elements specifically engineered to absorb and dissipate impact forces.
These specialized protective gloves feature strategic padding, typically made from thermoplastic rubber (TPR) or other shock-absorbing materials, positioned over the knuckles, fingers, and back of the hand. These reinforced areas create a protective barrier that absorbs and redistributes impact energy rather than allowing it to transfer directly to the wearer’s hand. The result is significant protection against crushing injuries, pinching hazards, and blunt force trauma that commonly occur in industries like oil and gas, construction, mining, and heavy manufacturing.
Modern impact resistant gloves have evolved substantially from early designs that were often bulky and restrictive. Today’s versions incorporate ergonomic design principles that maintain dexterity and comfort while providing superior protection. Many models feature breathable fabrics, flexible joints, and reinforced palm areas that allow for precise handling of tools and equipment.
The importance of impact protection cannot be overstated. According to safety statistics, hand injuries account for nearly 30% of all workplace injuries, with a significant portion involving impact trauma. The average cost of a single hand injury can range from 7,500to7,500 to 7,500to26,000 when considering medical expenses, lost productivity, and workers’ compensation. Impact resistant gloves have been proven to dramatically reduce both the frequency and severity of these injuries, making them an essential component of personal protective equipment (PPE) programs across numerous industries.
As a specialized form of PPE, impact resistant gloves must typically meet specific industry standards and certifications, such as EN 388:2016, which now includes a specific impact resistance rating, or the ANSI/ISEA 138-2019 standard that categorizes impact protection levels. These standards provide benchmarks for performance and help safety managers select appropriate protection for their specific work environments.
For companies seeking to source these critical safety products, understanding the fundamentals of impact resistance technology, material options, and quality indicators is essential to making informed procurement decisions that will adequately protect their workforce.
How to Choose the Best Impact Resistant Gloves for Your Business?
Selecting the optimal impact resistant gloves for your specific business needs requires a systematic approach that balances protection, functionality, comfort, and cost-effectiveness. Here’s a comprehensive guide to navigating this critical decision-making process:
1. Assess Your Specific Industry Risks
Begin by conducting a thorough hazard assessment of your workplace environment. Different industries present unique impact risks:
- Oil and gas operations typically require maximum impact protection due to heavy equipment handling, pipe manipulation, and exposure to high-pressure environments
- Construction sites need protection against falling objects, tool impacts, and compression between hard surfaces
- Mining operations face risks from rock falls, heavy machinery, and tool handling
- Automotive manufacturing involves parts assembly that can lead to pinch points and compression hazards
Document specific tasks where hands are vulnerable to impact injuries and note the intensity and frequency of potential impacts to determine the appropriate level of protection required.
2. Understand Protection Standards and Certifications
Familiarize yourself with the relevant industry standards that govern impact resistant gloves:
- ANSI/ISEA 138-2019: This American standard specifically addresses impact protection, categorizing gloves into three performance levels (1-3, with 3 providing the highest protection) based on transmitted force measurements
- EN 388:2016: The European standard includes an impact resistance test indicated by a “P” marking when passed
- CE Marking: Ensures compliance with European health, safety, and environmental protection standards
A reliable OEM work glove manufacturer like Qingdao Snell Protective Products will clearly communicate which standards their products meet and provide testing documentation to verify compliance.
3. Evaluate Protection Features and Materials
Impact resistant gloves utilize various protective technologies, each with distinct advantages:
- Thermoplastic Rubber (TPR): The most common impact-absorbing material, offering excellent protection-to-weight ratio
- D3O: A specialized material that remains flexible during normal use but instantly hardens upon impact
- EVA Foam: Lightweight with good shock absorption properties
- Air Cushioning Systems: Some advanced designs incorporate air chambers that compress upon impact
Consider the coverage area as well—some gloves protect only knuckles, while others extend protection to fingers, thumbs, and palm areas. For comprehensive protection, look for designs that shield all vulnerable areas without compromising mobility.
4. Consider Secondary Protection Needs
Many work environments require multiple types of protection beyond impact resistance:
- Cut Resistance: Often rated on a scale from A1 to A9 under ANSI/ISEA 105
- Puncture Resistance: Critical for environments with sharp objects
- Oil/Chemical Resistance: Essential for industries using hazardous substances
- Heat/Cold Protection: Important for extreme temperature environments
- Vibration Damping: Valuable for workers using power tools regularly
Select gloves that address all relevant hazards, as multi-hazard protection eliminates the need for workers to switch between different types of hand protection.
5. Prioritize Comfort and Dexterity
Even the most protective gloves will be ineffective if workers remove them due to discomfort or inability to perform tasks:
- Material Flexibility: Evaluate how the protective elements affect natural hand movement
- Breathability: Consider moisture-wicking liners and ventilation features to reduce hand fatigue
- Weight Distribution: Heavier protection should be balanced to prevent strain
- Sizing Options: Proper fit is crucial—too tight restricts movement and blood flow; too loose compromises dexterity and increases catching hazards
Request samples from manufacturers to allow workers to test comfort and usability in real working conditions before making bulk purchases.
6. Assess Durability and Cost-Effectiveness
Impact resistant gloves represent a significant investment in worker safety, but cost considerations should include:
- Lifespan Under Working Conditions: Higher quality gloves may cost more initially but offer better value through extended wear life
- Washing/Maintenance Requirements: Some gloves maintain performance through multiple cleaning cycles, while others degrade quickly
- Total Cost of Ownership: Calculate cost per day of use rather than just purchase price
- Replacement Indicators: Look for gloves with clear visual indicators showing when protection has been compromised
Manufacturers like Qingdao Snell often provide durability metrics based on accelerated wear testing, which can help estimate replacement frequency in your specific application.
7. Consider Supply Chain Reliability
Ensure your chosen supplier can consistently meet your needs:
- Production Capacity: Can they scale to meet your demand even during peak seasons?
- Lead Times: How quickly can they fulfill orders, especially for customized products?
- Minimum Order Quantities (MOQ): Do their minimum requirements align with your usage patterns?
- Sample Availability: Can they provide samples for testing before large orders?
Establishing a relationship with a manufacturer that offers flexibility in these areas provides long-term advantages for your PPE program.
By methodically evaluating these factors, you can identify impact resistant gloves that provide optimal protection for your specific workplace hazards while ensuring worker acceptance and cost-effectiveness.
Where to Buy Impact Resistant Gloves?
Finding reliable sources for high-quality impact resistant gloves is crucial for maintaining workplace safety standards. The marketplace offers several procurement channels, each with distinct advantages and considerations:
Direct from OEM Manufacturers
Purchasing directly from Original Equipment Manufacturers (OEMs) offers several significant advantages, particularly for medium to large businesses:
- Cost Efficiency: Eliminating intermediaries typically results in pricing advantages of 15-30% compared to distributor channels
- Customization Options: Direct manufacturer relationships facilitate tailored solutions including custom sizing, specific protection levels, and branded elements
- Quality Control: Direct communication lines with the production facility enable more rigorous quality oversight
- Technical Expertise: OEM engineers and safety specialists can provide application-specific guidance for your industry challenges
Leading impact glove manufacturers like Qingdao Snell Protective Products have established streamlined processes for international clients, with dedicated export departments handling logistics, compliance documentation, and shipping arrangements. For businesses requiring substantial volumes (typically 3,000-20,000 pairs minimum), this direct relationship proves most advantageous.
The process typically involves initial consultation, sample development and testing, production scheduling, quality control inspections, and shipping coordination. While lead times may range from 30-45 days for custom orders, the benefits in terms of product specificity and cost savings often outweigh the slightly longer procurement timeline.
Industrial Safety Distributors
National and regional safety equipment distributors serve as valuable intermediaries, particularly for businesses with lower volume requirements or those needing immediate delivery:
- Product Variety: Access to multiple manufacturers’ offerings through a single purchasing channel
- Technical Guidance: Experienced safety specialists can recommend appropriate solutions
- Inventory Availability: Stock on hand for urgent replacement needs
- Consolidated Purchasing: Efficiency in procuring multiple safety products from one source
- Local Support: Many distributors offer fitting services, training, and quick replacement
Major distributors like Grainger, Fastenal, MSC Industrial, and regional specialists maintain extensive catalogs of impact resistant gloves with standard configurations and sizing. While prices typically reflect a 15-30% markup over direct manufacturer pricing, the convenience and immediate availability often justify this premium for smaller operations or emergency situations.
Online Marketplaces
E-commerce platforms have transformed industrial safety procurement, offering unprecedented convenience and price comparison capabilities:
- Amazon Business: Features specialized industrial categories with business pricing
- GlobalIndustrial.com: Focus on workplace safety equipment with comprehensive filtering options
- Alibaba/Global Sources: Direct access to international manufacturers with MOQ considerations
- Industry-specific platforms: Specialized marketplaces catering to construction, oil and gas, or manufacturing sectors
These platforms excel for price comparison, small quantity purchases, and discovering new suppliers. Most offer detailed product specifications, certification verification, and user reviews that help evaluate performance. However, buyers should verify authenticity and certification claims, particularly when purchasing through generalized marketplaces rather than specialized industrial suppliers.
Trade Shows and Industry Exhibitions
Safety industry events provide unique opportunities to evaluate products hands-on and establish supplier relationships:
- National Safety Council (NSC) Expo: North America’s largest safety event
- A+A Safety Exhibition: Premier European safety equipment showcase
- China International Occupational Safety & Health Exhibition: Major Asian marketplace for safety innovations
- Regional industrial safety expositions: Smaller events focused on specific geographic markets
These events allow procurement specialists to physically examine products, discuss technical specifications directly with manufacturers, and often negotiate favorable terms for future orders. While not a direct purchasing channel, trade shows significantly inform buying decisions and establish valuable supplier contacts.
Manufacturer Representatives and Import Agents
For businesses lacking direct import capabilities or seeking supplier vetting assistance:
- Manufacturer Representatives: Work directly for international producers to facilitate sales in specific regions
- Import Agents: Independent third parties who handle supplier identification, quality control, logistics, and customs clearance
These intermediaries typically charge 5-15% commission but provide valuable services including supplier verification, pre-shipment inspections, consolidated shipping, and import documentation. For organizations new to international procurement or lacking established relationships with overseas manufacturers, these services often justify the additional cost through risk reduction and logistics simplification.
Choosing the Right Procurement Channel
The optimal purchasing strategy depends on several organizational factors:
- Volume Requirements: Direct OEM relationships become most advantageous above 3,000-5,000 pairs annually
- Customization Needs: Specialized protection requirements or branding necessitate manufacturer relationships
- Delivery Timeframes: Urgent requirements favor distributors or e-commerce solutions
- Technical Support: Complex applications benefit from distributors or direct manufacturer guidance
- Budget Constraints: Larger operations typically achieve better value through direct procurement
Many organizations implement hybrid strategies, establishing OEM relationships for standard inventory while maintaining distributor accounts for emergency needs or specialty items. Whatever approach you choose, ensuring supplier reliability, product certification, and consistent quality should remain paramount considerations.
Impact Resistant Gloves Manufacturer in China
China has emerged as the global manufacturing hub for industrial safety equipment, including advanced impact resistant gloves. The country’s manufacturing ecosystem offers unique advantages while requiring specific considerations for international buyers seeking reliable partnerships.
Chinese Manufacturing Landscape for Impact Resistant Gloves
The Chinese impact resistant glove manufacturing sector has undergone remarkable transformation over the past decade, evolving from basic production capabilities to sophisticated technical manufacturing:
- Manufacturing Clusters: Production is concentrated in several specialized regions:
- Zhejiang Province: Known for technical textiles and advanced work glove production
- Shandong Province: Home to established manufacturers like Qingdao Snell with integrated production facilities
- Guangdong Province: Specializes in high-end PPE with advanced manufacturing technologies
- Hebei Province: Emerging as a center for cost-effective industrial glove production
- Technological Advancement: Leading Chinese manufacturers have invested heavily in:
- Automated cutting and sewing systems for consistent production quality
- Computer-assisted design for ergonomic optimization
- Advanced materials science for improved impact absorption
- Testing laboratories for in-house certification verification
- Vertical Integration: Many established factories maintain comprehensive production capabilities:
- In-house yarn and textile production
- Molding facilities for TPR and other protective elements
- Coating application systems for palm treatments
- Packaging and quality control departments
Top Chinese Impact Resistant Glove Manufacturers
Several manufacturers have distinguished themselves through consistent quality, international certification compliance, and export capabilities:
- Qingdao Snell Protective Products Co., Ltd. – A leading OEM manufacturer specializing in industrial safety gloves, including advanced impact protection designs. With ISO 9001 certification and CE compliance, Qingdao Snell operates modern production facilities in Gaomi and Nantong. Their specialized impact resistant glove offerings include:
- Oil and gas industry-specific designs with enhanced dorsal protection
- Construction-oriented models combining impact and cut resistance
- Automotive assembly gloves with precision fingertip sensitivity
- Customization capabilities for specific workplace requirements
- Shanghai Saidisi Safety Products Co., Ltd. – Specializing in premium impact resistant designs with proprietary shock-absorbing technologies, their product line focuses on heavy industry applications.
- Hebei Jiansheng Safety Equipment Co., Ltd. – Known for cost-effective impact gloves with standardized protection patterns, they serve markets requiring high-volume, entry-level impact protection.
- Guangzhou Safety Equipment Manufacturing Group – Offers comprehensive safety solutions including specialized impact gloves for oil drilling, mining, and heavy machinery operation.
- Xingyu Gloves Technology (Zhejiang) Co., Ltd. – Focuses on innovative material combinations, including their proprietary impact-absorbing compounds that provide superior protection-to-weight ratios.
Quality and Certification Considerations
When sourcing from Chinese manufacturers, verification of quality standards and certifications is essential:
- International Certifications: Legitimate manufacturers will provide verifiable:
- CE certification for European market compliance
- EN 388:2016 test reports with impact protection ratings
- ISO 9001 quality management certification
- ANSI/ISEA 138-2019 test results for North American markets
- Testing Capabilities: Leading factories maintain:
- In-house testing laboratories for ongoing quality control
- Relationships with independent testing organizations like SGS, Bureau Veritas, or TÜV
- Documentation of regular third-party verification
- Quality Control Systems: Advanced manufacturers implement:
- Statistical process control throughout production
- Multiple inspection points from raw material to finished product
- Documented quality control procedures with traceability
Manufacturing Capabilities and Customization
Chinese manufacturers offer varying levels of production capability and customization options:
- Production Capacity: Output ranges from 10,000 to 500,000+ pairs monthly depending on facility size
- Customization Options:
- OEM branding and packaging
- Modified protection patterns for specific hazards
- Custom colors and visibility features
- Proprietary palm materials or coatings
- Specialized cuff designs or closure systems
- Sample Development: Timeframes typically range from:
- 7-10 days for modifications to existing designs
- 15-30 days for completely custom developments
- Production scaling following sample approval
Economic Considerations When Sourcing from China
Several factors influence the total cost of ownership when importing from Chinese manufacturers:
- Pricing Structure:
- FOB pricing (Free On Board) typically ranges from $4-15 USD per pair for impact resistant designs depending on protection level and features
- Volume discounts typically begin at 5,000 pairs with significant economies at 10,000+ pairs
- Customization may add 5-15% to base pricing depending on complexity
- Payment Terms:
- Standard terms often include 30% deposit with 70% payment before shipping
- Established relationships may secure more favorable terms
- Letters of credit provide security for larger transactions
- Logistics Considerations:
- Shipping times of 30-45 days for sea freight to North America or Europe
- Air freight options for urgent requirements at premium pricing
- Import duties ranging from 7-12% depending on destination country
- Customs clearance requirements and documentation
Establishing Effective Supplier Relationships
Building productive partnerships with Chinese manufacturers requires understanding cultural and business practices:
- Communication Protocols:
- Clear technical specifications with detailed diagrams
- Regular video conferences for complex discussions
- Documented email trails for all agreements
- Professional translation services when necessary
- Relationship Development:
- Face-to-face meetings establish stronger foundations
- Factory visits for initial qualification and periodic quality review
- Understanding of Chinese business customs and negotiation styles
- Long-term relationship focus rather than transaction-based approach
- Quality Assurance Practices:
- Pre-production sample approval processes
- Third-party inspection services like SGS or Bureau Veritas
- Container loading supervision for large shipments
- Regular supplier evaluation and development programs
The Chinese manufacturing landscape for impact resistant gloves offers compelling advantages in terms of cost efficiency, production capacity, and increasingly sophisticated technical capabilities. By implementing thorough due diligence in supplier selection, quality verification, and relationship management, international buyers can establish valuable supply partnerships that deliver consistent protection for their workforce.
What to Look for in a Reliable Impact Resistant Gloves Manufacturer?
Identifying a trustworthy impact resistant glove manufacturer requires evaluating multiple factors beyond just pricing. This comprehensive assessment framework will help you select manufacturing partners capable of delivering consistent quality, compliance, and service.
Manufacturing Expertise and Specialization
The depth of a manufacturer’s experience with impact resistant technologies significantly affects product performance and reliability:
- Production History: Companies with extensive experience in impact protection have typically refined their designs through multiple iterations based on field feedback and testing. Look for manufacturers with at least 5-10 years of specific experience in impact glove production rather than general work glove manufacturing.
- Technical Specialization: The most reliable manufacturers demonstrate deep technical knowledge in impact absorption science. During consultations, they should articulate:
- How different impact-absorbing materials perform under various conditions
- The relationship between protection placement and common injury patterns
- How protection thickness affects both safety and dexterity
- Trade-offs between different design approaches
- Material Innovation: Leading manufacturers continuously improve their offerings through material science advancements. Companies like Qingdao Snell invest in research and development to incorporate next-generation materials like:
- Advanced TPR (Thermoplastic Rubber) formulations with enhanced flexibility
- Specialized impact-absorbing foams with memory properties
- Hybrid protection systems combining multiple technologies
- Breathable impact protection that reduces heat buildup
- Engineering Capability: Look for evidence of engineering sophistication through:
- Computer-aided design processes for protection optimization
- Ergonomic analysis capabilities
- 3D modeling and prototyping systems
- Documented design revision processes
Quality Management Systems
Reliable manufacturers implement comprehensive quality systems throughout their production process:
- Certifications and Standards:
- ISO 9001 certification demonstrates systematic quality management
- ISO 14001 indicates environmental management commitment
- OHSAS 18001/ISO 45001 reflects workplace safety priorities
- SA8000 or WRAP certification addresses social compliance concerns
- Testing Capabilities:
- In-house testing laboratories for routine quality verification
- Equipment calibration programs and documentation
- Demonstrated knowledge of testing methods specified in EN 388, ANSI/ISEA 138
- Relationships with accredited third-party testing facilities
- Quality Control Processes:
- Incoming material inspection procedures
- In-process quality checks at critical production stages
- Final product inspection protocols with statistical sampling
- Documented non-conformance procedures and corrective action systems
- Traceability systems linking finished products to material batches
- Documentation Standards:
- Comprehensive technical files for each product
- Detailed material specifications and test reports
- Process control documents and work instructions
- Calibration certificates for testing equipment
Production Capabilities and Scale
Manufacturing capacity and production sophistication directly impact a supplier’s ability to meet your requirements:
- Facility Infrastructure:
- Modern, purpose-built production facilities
- Climate-controlled environments for consistent production conditions
- Dedicated areas for different production stages
- Appropriate storage for raw materials and finished goods
- Production Technology:
- Automated cutting systems for consistency
- Specialized equipment for TPR molding and attachment
- Computer-controlled stitching for critical seams
- Modern coating application systems
- Capacity and Flexibility:
- Sufficient monthly capacity to accommodate your peak requirements
- Ability to scale production during high-demand periods
- Flexibility to handle both standard and rush orders
- Production planning systems for accurate lead time estimation
- Vertical Integration:
- In-house textile knitting or weaving capabilities
- TPR or protective element manufacturing
- Coating formulation and application
- Packaging production
Compliance and Ethical Manufacturing
Responsible sourcing requires verification of regulatory compliance and ethical practices:
- Product Compliance:
- CE marking with supporting documentation
- Third-party verification of protection claims
- Compliance with EU REACH regulations for chemical safety
- Documentation supporting ANSI/ISEA certifications for North American markets
- Social Compliance:
- Fair labor practices verification
- Appropriate working conditions
- No child labor utilization
- Fair compensation practices
- Environmental Responsibility:
- Waste reduction programs
- Energy efficiency initiatives
- Chemical management systems
- Sustainable material sourcing where possible
- Transparency:
- Willingness to host facility audits
- Open disclosure of subcontractors if used
- Clear communication about production methods
- Honesty about capabilities and limitations
Business Practices and Customer Service
Reliable manufacturers demonstrate professional business conduct and customer orientation:
- Communication Effectiveness:
- Responsive communication systems
- English-proficient key personnel
- Clear documentation and correspondence
- Transparency about challenges or delays
- Customer Support Structure:
- Dedicated account representatives
- Technical support capabilities
- Sampling programs
- Problem resolution processes
- Financial Stability:
- Established business history
- Appropriate facilities investment
- Reasonable payment terms
- Banking references
- Intellectual Property Respect:
- Confidentiality agreements for proprietary designs
- No unauthorized reproduction of patented features
- Clear agreements regarding design ownership
- Protection of customer information
Long-term Partnership Potential
Beyond immediate transaction considerations, evaluate manufacturers as potential long-term partners:
- Continuous Improvement Philosophy:
- Regular investment in equipment upgrades
- Staff training and development programs
- Implementation of efficiency improvements
- Design evolution based on market feedback
- Innovation Capability:
- New product development roadmaps
- Material research initiatives
- Awareness of industry trends
- Customer collaboration on advances
- Strategic Alignment:
- Understanding of your industry’s specific needs
- Willingness to develop market-specific solutions
- Compatibility with your growth projections
- Shared quality philosophy
- Relationship Approach:
- Focus on mutual benefit rather than transactional thinking
- Interest in understanding your application requirements
- Proactive problem-solving attitude
- Investment in relationship development
By thoroughly evaluating potential manufacturers against these criteria, procurement teams can identify partners capable of consistently delivering impact resistant gloves that meet both protection requirements and business objectives. The most successful supplier relationships typically develop with manufacturers who demonstrate strength across multiple evaluation categories rather than excelling in just one area.
MOQ (Minimum Order Quantity) Considerations When Ordering Impact Resistant Gloves
Understanding minimum order quantity requirements is essential when sourcing impact resistant gloves from manufacturers. These requirements significantly influence your procurement strategy and supply chain planning. Here’s what you need to know about MOQ considerations to optimize your purchasing decisions:
Why Manufacturers Set MOQs
Manufacturers establish minimum order quantities for several legitimate business reasons:
- Production Efficiency: Impact resistant glove production involves multiple setup processes including material preparation, die cutting, TPR molding, and sewing line configuration. These setup costs remain relatively fixed regardless of production volume, making smaller runs economically unfeasible.
- Material Procurement Economics: Raw materials for specialized impact gloves (especially TPR compounds, high-performance yarns, and specialized coatings) often have their own minimum purchase requirements from suppliers. Manufacturers must order these in economical quantities.
- Quality Consistency: Larger production runs allow manufacturers to maintain consistent quality through stable production parameters. Once machines are properly calibrated, longer runs produce more uniform results.
- Color and Material Minimums: For customized gloves, specialized colors for shells, TPR elements, or coating materials typically have minimum batch sizes from suppliers, often starting at 50-100kg depending on the material.
- Business Sustainability: Higher volume orders help manufacturers maintain profitable operations, invest in equipment, and sustain employment for skilled workers.
Typical MOQ Ranges by Manufacturer Type
MOQ requirements vary significantly based on the type of supplier and their business model:
Manufacturer Type | Typical MOQ Range | Best For | Lead Time Expectations |
---|---|---|---|
Direct Factory (e.g., Qingdao Snell) | 3,000-20,000 pairs per style | Large organizations, distributors, recurring needs | 30-45 days for production |
Trading Companies | 1,000-5,000 pairs per style | Medium-sized organizations | 45-60 days (includes sourcing time) |
Specialized Boutique Manufacturers | 500-2,000 pairs per style | Unique requirements, specialized protection | 30-45 days plus development time |
Wholesale Distributors | 100-500 pairs per style | Smaller organizations, mixed orders | 7-14 days from stock |
Retail Suppliers | 1-50 pairs | Immediate needs, trials | 1-5 days from stock |
Qingdao Snell, as a direct manufacturer with significant production capacity across their Gaomi and Nantong facilities, typically requires minimum orders of 3,000-20,000 pairs depending on the complexity of the impact resistant design. Their scale enables them to serve larger industrial clients while maintaining competitive pricing.
Strategies to Work Within MOQ Constraints
If manufacturer MOQs exceed your immediate needs, consider these approaches:
- Consolidate Orders Across Divisions: Combine requirements from multiple departments, facilities, or project sites to reach minimum thresholds.
- Develop Standardized Designs: Create impact glove specifications that work across multiple applications rather than highly specialized versions for each task, allowing higher volume of fewer styles.
- Scheduled Release Programs: Negotiate agreements where you commit to the full MOQ but receive deliveries in smaller quantities over time (often called blanket orders).
- Style Consolidation With Color Variation: Some manufacturers allow splitting an MOQ across different colors of the same design, providing some variety while maintaining production efficiency.
- Distribution Partnerships: Partner with distributors who can purchase manufacturer minimums and then supply smaller quantities as needed.
- Group Purchasing: Some industry associations or purchasing groups consolidate orders from multiple smaller companies to meet manufacturer minimums.
- MOQ Negotiation Strategies: Consider these approaches when discussing MOQs with manufacturers:
- Offer deposits or advanced payments for order security
- Commit to multiple orders over time
- Accept slightly longer lead times for smaller quantities
- Discuss simplified packaging to reduce costs
- Consider stock designs with custom labeling rather than fully custom products
Cost Implications of Order Quantity
Order volume directly impacts unit pricing through:
Order Volume | Typical Price Impact | Reasoning |
---|---|---|
Below MOQ | 15-30% premium (if accepted) | Setup costs distributed across fewer units |
At MOQ | Standard pricing | Manufacturer’s baseline efficiency point |
2-3× MOQ | 5-10% discount | Improved production efficiency |
5× MOQ | 10-15% discount | Significant material purchasing power |
10× MOQ | 15-20%+ discount | Maximum efficiency, optimized logistics |
Understanding this sliding scale helps organizations balance inventory carrying costs against volume discounts. For many medium to large organizations, ordering at 2-3× MOQ often represents the optimal balance between pricing advantages and inventory management.
MOQ Considerations for Customized Impact Resistant Gloves
Custom features significantly affect minimum order requirements:
Customization Type | MOQ Impact | Lead Time Effect |
---|---|---|
Custom TPR Colors | Increases MOQ by 30-50% | Adds 7-14 days |
Custom Shell Colors | Increases MOQ by 20-40% | Adds 5-10 days |
Custom TPR Patterns | Increases MOQ by 50-100% | Adds 14-30 days |
Custom Branding (Printing) | Minimal MOQ increase | Adds 3-7 days |
Custom Packaging | Moderate MOQ increase | Adds 7-14 days |
Full Custom Design | Increases MOQ by 100%+ | Adds 30-60 days |
For organizations requiring truly unique impact protection solutions, these higher minimums often prove worthwhile when amortized across a larger safety program. Manufacturers like Qingdao Snell have established development processes for custom impact gloves that guide clients from concept through prototyping to final production, though their minimum quantities for such specialized development typically start at the higher end of their range.
Managing Inventory Against MOQ Requirements
Balancing minimum order quantities with inventory management requires strategic planning:
- Safety Stock Calculations: Determine appropriate buffer inventory based on:
- Usage rate variability
- Lead time reliability
- Criticality of uninterrupted supply
- Storage constraints
- Consumption Tracking: Implement systems to monitor usage patterns, enabling more accurate forecasting for reorders.
- Supplier-Managed Inventory Programs: Some manufacturers offer programs where they maintain agreed inventory levels at their facility or in local warehouses, shipping against actual orders while the customer commits to eventually purchasing the full MOQ.
- Size Distribution Planning: Analyze your workforce’s glove size requirements to order appropriate quantities of each size, typically following distribution patterns such as:
- XS: 5-10%
- S: 10-15%
- M: 25-30%
- L: 30-35%
- XL: 15-20%
- XXL: 5-10%
- Product Lifecycle Management: For styles subject to updates or obsolescence, carefully balance MOQ requirements against product lifecycle to avoid excess obsolete inventory.
By developing a comprehensive understanding of MOQ dynamics and implementing strategic approaches to work within these constraints, procurement professionals can balance the economic advantages of larger orders with practical inventory management considerations. This balanced approach ensures both cost-effectiveness and continuous availability of critical safety equipment.
How to Customize Impact Resistant Gloves with Your Logo and Branding?
Customized impact resistant gloves do more than just protect your workforce—they reinforce your brand identity, promote safety culture, and can even help prevent loss or theft. Understanding the customization process ensures you’ll achieve professional results that enhance your corporate image while maintaining the protective integrity of these specialized safety products.
Strategic Benefits of Branded Impact Resistant Gloves
Before diving into the customization process, consider the strategic advantages of branded safety equipment:
- Corporate Identity Reinforcement: Branded PPE extends your visual identity to the worksite, creating consistency across all company touchpoints.
- Safety Culture Promotion: Custom safety messaging on gloves serves as a constant reminder of your organization’s commitment to worker protection.
- Theft Deterrence: Distinctively branded gloves are less likely to be removed from worksites, reducing replacement costs.
- Contractor/Department Differentiation: Unique color schemes or markings can distinguish between departments, contractors, or access authorizations.
- Professional Appearance: Consistent, branded PPE projects professionalism to clients, regulators, and visitors.
- Team Cohesion: Uniform branded equipment fosters team identity and belonging.
Customization Options for Impact Resistant Gloves
Modern manufacturing techniques offer numerous ways to incorporate branding into impact resistant gloves:
1. TPR (Thermoplastic Rubber) Customization
The protective impact elements provide excellent branding opportunities:
- Molded-in Logos: The manufacturer creates custom molds that incorporate your logo directly into the TPR material
- Custom Colors: TPR elements can be produced in your corporate colors (Pantone matching available)
- Debossed/Embossed Elements: Raised or recessed designs in the TPR surface
- Combined Protection Patterns: Impact elements arranged to subtly form logos or distinctive patterns
TPR customization typically requires the highest minimum order quantities (typically 5,000+ pairs) and involves tooling costs for custom molds, but delivers the most integrated and durable branding.
2. Shell Fabric Customization
The base glove material offers several branding approaches:
- Custom Dyed Fabric: Base material produced in corporate colors
- Printed Patterns: Repeated logos or patterns printed on the shell fabric
- High-visibility Options: Fluorescent colors with corporate elements
- Custom Yarn Combinations: Knitted patterns incorporating brand colors
Shell customization generally requires moderate order volumes (3,000+ pairs) and provides highly visible branding across the entire glove.
3. Direct Printing
Applied to finished gloves on suitable surfaces:
- Silicone Printing: Durable, slightly raised prints ideal for logos
- Heat Transfer: Detailed, colorful designs with good durability
- Pad Printing: Precise application of simpler designs
- Screen Printing: Cost-effective for larger, less detailed elements
Direct printing typically has the lowest minimum requirements (sometimes as low as 1,000 pairs) and offers excellent flexibility for updating designs between orders.
4. Cuff and Closure Customization
These areas provide additional branding opportunities:
- Woven Labels: Sewn onto cuffs with company information
- Custom Tags: Attached to gloves with sizing and branding
- Printed Cuffs: Highly visible branding on extended cuffs
- Colored Closure Systems: Hook-and-loop or elastic closures in corporate colors
Cuff customization can often be implemented at lower volumes (2,000+ pairs) and provides good visibility when gloves are stored or not being worn.
The Customization Process with OEM Manufacturers
Working with quality manufacturers like Qingdao Snell involves a structured development process:
- Initial Consultation and Design Brief:
- Determine customization objectives (brand visibility, department coding, etc.)
- Provide logo files in appropriate formats (vector files preferred: AI, EPS, PDF)
- Specify corporate colors (Pantone references ensure accuracy)
- Discuss placement and size requirements
- Clarify protection requirements and relevant standards
- Technical Feasibility Assessment:
- Manufacturer evaluates how customization affects protection integrity
- Material compatibility analysis for printing or dyeing
- Production process adjustments required
- Compliance implications assessment
- Prototype Development:
- Digital mockups for initial approval
- Physical samples of customized elements
- Prototype pairs for evaluation
- Testing to ensure customization doesn’t compromise protection
- Sample Testing and Approval:
- Wear testing in actual work environments
- Durability evaluation of branding elements
- Washing/cleaning impact on customization
- Final design adjustments
- Production Planning:
- Finalization of order quantities and size distribution
- Production timeline establishment
- Quality control criteria specific to customized elements
- Approval of pre-production samples
- Manufacturing and Quality Control:
- Regular production updates
- In-process quality checks for branding consistency
- Sample approval during production
- Final inspection before shipping
Design Considerations for Maximum Effectiveness
Creating effective branded impact gloves requires balancing visibility with practicality:
- Contrast and Visibility: Ensure logo colors provide sufficient contrast against base materials for easy recognition
- Placement Optimization: Position logos where they’ll remain visible despite wear patterns
- Size Appropriateness: Scale designs appropriately—too small becomes indiscernible, too large appears unprofessional
- Durability Considerations: Balance design complexity with durability requirements
- Regulatory Compliance: Ensure branding doesn’t obscure required certification markings
- Distortion Prevention: Account for how designs may stretch or distort on flexible materials
Cost Factors in Custom Branding
Several factors influence the cost impact of customization:
Customization Type | Typical Cost Premium | Setup/Tooling Costs | Minimum Order Impact |
---|---|---|---|
Custom TPR Colors | 5-10% | $300-800 | Significant increase |
Molded-in TPR Logos | 10-20% | $800-2,500 | Highest requirements |
Shell Fabric Coloring | 8-15% | $500-1,000 | Moderate increase |
Direct Printing (1-2 colors) | 3-8% | $200-400 | Minimal increase |
Direct Printing (multi-color) | 8-15% | $300-600 | Slight increase |
Custom Packaging | 5-15% | $400-1,200 | Moderate increase |
Woven Labels | 2-5% | $150-300 | Minimal increase |
Many manufacturers, including Qingdao Snell, offer package pricing that becomes more economical as order quantities increase, often absorbing setup costs entirely for orders exceeding certain thresholds (typically 10,000+ pairs).
Maintaining Consistency Across PPE Programs
For maximum brand impact, consider these integration strategies:
- Cross-Product Consistency: Align impact glove branding with other PPE items (helmets, eyewear, clothing)
- Documentation Integration: Reflect the same visual language in safety manuals and training materials
- Packaging Coordination: Extend branding to glove packaging, dispensers, and storage
- Safety Campaign Alignment: Coordinate glove branding with broader safety initiatives
- Contractor Requirements: Establish standards for contractor compliance with your PPE branding
Implementing a comprehensive branding approach across your entire safety program maximizes recognition and reinforces safety culture at every touchpoint.
By strategically approaching the customization process, organizations can transform standard impact resistant gloves into powerful brand assets that simultaneously protect workers and reinforce corporate identity. Working with experienced manufacturers like Qingdao Snell ensures that branding enhancements complement rather than compromise the primary protective function of these specialized safety products.
What Are the Most Durable Materials for Impact Resistant Gloves?
The durability and performance of impact resistant gloves depend critically on material selection. Understanding the properties, advantages, and limitations of different materials helps procurement specialists make informed decisions that balance protection, longevity, comfort, and cost-effectiveness.
Impact-Absorbing Materials: The Protective Core
The defining feature of impact resistant gloves is their specialized shock-absorbing materials, each offering distinct performance characteristics:
Thermoplastic Rubber (TPR)
TPR remains the most widely used impact protection material due to its versatility and effectiveness:
- Composition: Polymer blends that combine plastic and rubber properties
- Protection Mechanism: Absorbs impact energy through material deformation and slow rebound
- Durability Factors:
- Resistance to repeated impacts: Excellent
- Abrasion resistance: Very good
- Chemical resistance: Good (formulation dependent)
- UV stability: Moderate to good
- Temperature tolerance: -20°C to 80°C typical
- Advantages:
- Excellent moldability for anatomical designs
- Scalable hardness (Shore A 40-90) for application-specific protection
- Good flexibility-to-protection ratio
- Cost-effective for mass production
- Colorable for safety visibility or branding
- Limitations:
- Heavier than some alternatives
- May stiffen in extremely cold environments
- Quality varies significantly between formulations
- Lifespan Expectation: 3-6 months under heavy daily use; 6-12 months under moderate use
- Applications: General industrial protection, oil and gas, construction, mining
D3O® and Similar Smart Materials
These advanced materials represent the premium segment of impact protection:
- Composition: Non-Newtonian polymers that change behavior under stress
- Protection Mechanism: Molecules lock together upon impact, then return to flexible state
- Durability Factors:
- Resistance to repeated impacts: Exceptional
- Abrasion resistance: Good
- Chemical resistance: Good
- UV stability: Good
- Temperature tolerance: -20°C to 40°C (functional range)
- Advantages:
- Superior protection-to-weight ratio
- Extremely flexible during normal use
- Exceptional energy absorption
- Maintains performance through multiple impacts
- Thinner profiles possible
- Limitations:
- Significantly higher cost
- More complex integration into glove designs
- Limited temperature range for optimal performance
- Often requires proprietary manufacturing techniques
- Lifespan Expectation: 6-12 months under heavy use; 12-18 months under moderate use
- Applications: Precision work requiring maximum dexterity alongside protection, high-risk environments with severe impact hazards, premium safety programs
EVA and PU Foams
These lightweight foam materials provide cost-effective impact mitigation:
- Composition: Closed-cell ethylene vinyl acetate or polyurethane foams of varying densities
- Protection Mechanism: Compression of air-filled cells absorbs impact energy
- Durability Factors:
- Resistance to repeated impacts: Moderate
- Abrasion resistance: Fair to good
- Chemical resistance: Limited
- UV stability: Poor to moderate
- Temperature tolerance: -10°C to 70°C
- Advantages:
- Extremely lightweight
- Excellent comfort and flexibility
- Cost-effective
- Good breathability
- Easy to incorporate into designs
- Limitations:
- Compression set over time reduces protection
- Less effective against high-energy impacts
- Degrades faster than TPR or advanced materials
- Less resistant to oils and chemicals
- Lifespan Expectation: 1-3 months under heavy use; 3-6 months under moderate use
- Applications: Light-duty protection, areas requiring maximum dexterity, cost-sensitive applications, situations where weight is critical
Shell Materials: The Foundation of Durability
The base material of impact resistant gloves significantly affects overall durability and functionality:
High-Performance Synthetic Fibers
Engineered textiles provide superior durability for demanding applications:
Material | Durability Characteristics | Best Applications | Relative Cost |
---|---|---|---|
HPPE (High-Performance Polyethylene) | • Exceptional abrasion resistance• Cut resistant (levels vary by construction)• Good chemical resistance• Lightweight• Poor heat resistance | • Combined cut and impact hazards• Oily environments• Applications requiring dexterity | High |
Para-aramid (Kevlar®) | • Excellent cut resistance• Good heat resistance• Moderate abrasion resistance• UV sensitive• Maintains strength when wet | • High-cut-risk environments• Heat exposure areas• Heavy industry• Mining | High |
Meta-aramid (Nomex®) | • Exceptional heat resistance• Good abrasion resistance• Self-extinguishing• Maintains integrity at high temperatures | • Oil and gas• Firefighting support• Hot work environments• Welding support | High |
Composite Engineered Yarns | • Customized performance profiles• Balanced properties• Can incorporate multiple performance aspects | • Application-specific designs• Balanced hazard environments | Moderate to High |
Manufacturers like Qingdao Snell have developed significant expertise in selecting and combining these advanced fibers to achieve specific performance profiles tailored to different industry requirements.
Conventional Synthetic Fibers
More economical options that still provide good performance in less demanding applications:
Material | Durability Characteristics | Best Applications | Relative Cost |
---|---|---|---|
Nylon | • Good abrasion resistance• Moderate tensile strength• Fast drying• Low moisture absorption | • General purpose• Dry environments• Moderate abrasion risk | Low to Moderate |
Polyester | • Good dimensional stability• UV resistant• Moderate abrasion resistance• Hydrophobic | • Outdoor use• Wet environments• Where colorfastness matters | Low |
Spandex Blends | • Excellent flexibility• Good fit retention• Moderate durability• Enhances comfort | • Applications requiring dexterity• Precision work• User comfort priority | Moderate |
Natural Fibers and Blends
Traditional materials that offer specific advantages for certain applications:
Material | Durability Characteristics | Best Applications | Relative Cost |
---|---|---|---|
Cotton | • Good comfort• Moderate abrasion resistance• Poor wet performance• Limited strength | • Light duty• Comfort priority• Where breathability matters | Low |
Cotton/Synthetic Blends | • Balanced comfort/durability• Improved moisture management• Better dimensional stability | • General purpose• Moderate risk environments• Extended wear situations | Low to Moderate |
Palm Coatings: The Wear Interface
Palm coatings significantly impact both grip functionality and overall glove longevity:
Nitrile Coatings
- Durability Profile: Excellent abrasion resistance, good puncture resistance, exceptional oil resistance
- Lifespan Impact: Extends glove life by 30-50% in abrasive environments compared to uncoated
- Best Applications: Oil and gas, automotive, machine operation, general maintenance
- Limitations: Less breathable, moderate dry grip
Polyurethane (PU) Coatings
- Durability Profile: Good abrasion resistance, excellent dexterity, moderate chemical resistance
- Lifespan Impact: Extends glove life by 20-40% while maintaining flexibility
- Best Applications: Assembly, precision work, electronics, light oil exposure
- Limitations: Less effective in heavily oiled environments, moderate puncture resistance
Latex Coatings
- Durability Profile: Excellent grip in wet conditions, good elasticity, moderate abrasion resistance
- Lifespan Impact: Extends grip functionality but moderate impact on overall lifespan
- Best Applications: Construction, general handling, situations requiring excellent grip
- Limitations: Poor oil resistance, potential allergen concerns, moderate chemical resistance
Specialized Coatings
- Sandy/Foam Nitrile: Enhanced grip with good durability, ideal for oily part handling
- PVC Dots: Economic grip enhancement with minimal impact on breathability
- Dual-layer Systems: Combines durability of one material with grip properties of another
Longevity Enhancing Design Features
Beyond material selection, specific design elements can significantly extend the functional lifespan of impact resistant gloves:
- Reinforced High-Wear Areas: Additional material between thumb and forefinger, palm reinforcement patches
- Seamless Construction: Elimination of seams in high-stress areas reduces failure points
- Engineered Stress Point Protection: Strategic reinforcement at natural break points
- Dedicated Wear Indicators: Color-change systems that reveal when protection is compromised
- Washable Designs: Materials and construction methods that withstand regular cleaning
- Ventilation Systems: Moisture management features that prevent material degradation from sweat
Selecting Materials for Specific Industry Challenges
Different working environments place unique demands on impact resistant gloves:
Industry | Primary Durability Challenges | Recommended Material Combination |
---|---|---|
Oil & Gas | • Oil exposure• Abrasive surfaces• Chemical contact• Sustained heavy use | • HPPE or para-aramid shell• TPR or D3O impact protection• Sandy nitrile coating• Reinforced thumb crotch |
Construction | • Abrasion from rough materials• Varied impact risks• Wet/dry conditions• Cost sensitivity | • Synthetic/cotton blend shell• TPR impact protection• Latex or PU coating• Knuckle reinforcement |
Automotive Manufacturing | • Oil and grease exposure• Metal edge contacts• Precision requirements• Extended wear periods | • HPPE lightweight shell• Targeted TPR protection• Full nitrile coating• Enhanced thumb durability |
Mining | • Extreme abrasion• Heavy impact risks• Wet conditions• Extended shift wear | • Para-aramid shell• Heavy-duty TPR protection• Full double-dipped nitrile• Extended cuff protection |
Logistics & Warehousing | • Package handling abrasion• Moderate impact risks• Cost efficiency• Dexterity needs | • Polyester/spandex shell• Targeted TPR protection• Polyurethane coating• Breathable back design |
Qingdao Snell’s product development team specializes in analyzing specific workplace challenges and developing material combinations that address the particular wear patterns and protection needs of different industries. Their engineering approach ensures that material selection optimizes both protection and durability for the specific application.
By understanding the performance characteristics of these various materials, safety managers and procurement specialists can make informed decisions that balance initial investment against total cost of ownership, ultimately selecting impact resistant gloves that deliver both effective protection and economical service life.
How to Ensure Quality Control About Impact Resistant Gloves?
Implementing effective quality control for impact resistant gloves requires a comprehensive approach that spans from initial design verification through ongoing supplier management. This systematic framework ensures consistent protection that meets regulatory requirements and delivers reliable performance in demanding work environments.
Establishing Performance Requirements
Effective quality control begins with clearly defined performance specifications:
- Protection Standards Identification:
- Determine applicable regulatory standards (EN 388:2016, ANSI/ISEA 138-2019)
- Specify required protection levels (Impact Level 1, 2, or 3 under ANSI/ISEA 138)
- Document any industry-specific or company-specific requirements exceeding standard minimums
- Performance Criteria Development:
- Quantifiable impact protection metrics (force transmission limits)
- Durability requirements (cycle testing targets)
- Dexterity preservation standards (fine manipulation tests)
- Environmental resistance needs (temperature ranges, chemical exposures)
- Specification Documentation:
- Comprehensive technical specifications with measurable parameters
- Reference samples for subjective quality aspects
- Tolerance ranges for critical dimensions and features
- Detailed material requirements with acceptable alternatives
Pre-Production Qualification
Before approving production, implement these quality verification steps:
- Laboratory Testing Protocol:
- Impact resistance verification using standardized testing methods
- Material composition analysis to confirm specification compliance
- Mechanical property testing (tensile strength, tear resistance)
- Accelerated wear testing to predict field durability
- Sample Evaluation Process:
- Multiple sample iterations to refine design
- Production sample approval from both technical and user perspectives
- Documented approval process with sign-off requirements
- Retention of approved samples as reference standards
- Manufacturing Capability Assessment:
- Supplier quality management system verification
- Production capacity validation
- Process capability analysis for critical features
- Quality control infrastructure evaluation
In-Production Quality Control Measures
During manufacturing, implement these quality assurance processes:
- Raw Material Verification:
- Material certification review for each component
- Incoming inspection for critical materials
- Supplier material test reports validation
- Batch traceability system implementation
- In-Process Inspection Points:
- Critical control points at key production stages:
- Shell material knitting/cutting quality
- Impact protection element formation
- Protection attachment integrity
- Coating application consistency
- Stitching quality and placement
- Critical control points at key production stages:
- Statistical Process Control:
- Identification of key quality variables
- Establishment of control limits
- Regular measurement and charting
- Process adjustment protocols when variations occur
- End-Product Testing Regimen:
Test Type | Testing Frequency | Acceptance Criteria | Documentation |
---|---|---|---|
Visual Inspection | 100% of production | No visible defects, correct labeling, consistent appearance | Inspection records with defect categorization |
Dimensional Verification | Statistical sampling (AQL 2.5) | Within tolerance ranges for critical dimensions | Measurement records with statistical analysis |
Impact Resistance Testing | Batch sampling (1 per 500-1000 units) | Meets or exceeds standard requirements | Test reports with force transmission data |
Seam Strength | Statistical sampling | Meets minimum tensile requirements | Pull test results with pass/fail recording |
Coating Adhesion | Statistical sampling | No delamination under specified force | Adhesion test results with measurement data |
Functional Testing | Statistical sampling | Maintains dexterity for specified tasks | Dexterity test results with time measurements |
Supplier Quality Management
For organizations sourcing from manufacturers like Qingdao Snell, implementing these supplier quality management practices ensures consistent performance:
- Supplier Qualification Process:
- Initial capability assessment
- Quality management system certification verification
- Historical performance evaluation
- Financial stability consideration
- Ethics and compliance verification
- Quality Agreement Implementation:
- Documented quality expectations
- Testing responsibilities definition
- Non-conformance handling procedures
- Continuous improvement requirements
- Regular quality review meetings
- Audit Program Development:
- On-site audit schedule establishment
- Process-focused audit protocols
- Verification of corrective action effectiveness
- Documentation review requirements
- Unannounced audit provisions
- Performance Metrics Tracking:
- Key performance indicators establishment
- Regular supplier scorecard reviews
- Trend analysis for early problem detection
- Comparative performance evaluation
- Improvement target setting
Field Performance Monitoring
Quality control extends beyond manufacturing to actual workplace performance:
- User Feedback Collection System:
- Structured user surveys
- Wear and comfort evaluation forms
- Protection effectiveness reporting
- Durability assessment in specific applications
- Failure Analysis Protocol:
- Systematic examination of returned products
- Root cause determination
- Correlation with manufacturing data
- Corrective action implementation
- Design modification when necessary
- Wear Testing Program:
- Controlled field trials in actual work environments
- Comparative evaluation of different models/sources
- Documentation of performance under specific conditions
- Longevity assessment under regular use
- Continuous Improvement Process:
- Feedback integration into specifications
- Regular review of quality requirements
- Benchmark comparison with industry standards
- Implementation of technological advancements
Documentation and Traceability Systems
Comprehensive record-keeping supports effective quality management:
- Product Traceability Implementation:
- Lot coding systems
- Manufacturing date identification
- Material batch tracking
- Production line identification
- Link between quality records and specific production runs
- Technical File Maintenance:
- Complete design documentation
- Material specifications
- Test reports and certifications
- Production process documentation
- Quality control records
- Non-conformance Management System:
- Documented handling procedures
- Investigation requirements
- Corrective action tracking
- Preventive measure implementation
- Management review process
- Compliance Documentation:
- Regulatory submission records
- Certification maintenance
- Testing laboratory accreditation verification
- Updates for regulatory changes
- Record retention system
Advanced Quality Assurance Technologies
Leading organizations implement these advanced methods to enhance quality control:
- Automated Inspection Systems:
- Computer vision for visual defect detection
- Automated dimension verification
- Real-time process monitoring
- Production data analysis
- Enhanced Testing Methods:
- High-speed video impact analysis
- Thermal imaging for attachment integrity
- Microscopic examination of materials
- Chemical analysis for material verification
- Digital Quality Management Systems:
- Enterprise quality software implementation
- Real-time quality data collection
- Statistical analysis automation
- Integration with production planning systems
- Supplier quality portal access
- Predictive Quality Methodologies:
- Data mining for quality trend identification
- Correlation analysis between process variables and quality outcomes
- Early warning systems for potential quality issues
- Machine learning applications for defect pattern recognition
Training and Competency Programs
Human factors significantly impact quality outcomes:
- Quality Awareness Training:
- Function-specific quality responsibilities
- Impact of quality on worker safety
- Cost of quality concepts
- Individual role in quality assurance
- Technical Skills Development:
- Inspection method standardization
- Test equipment operation certification
- Measurement system analysis training
- Defect identification standardization
- Supplier Quality Management Skills:
- Audit techniques and protocols
- Corrective action verification methods
- Quality system evaluation
- Supplier development approaches
- Continuous Improvement Methodologies:
- Six Sigma or Lean applications to quality processes
- Root cause analysis techniques
- Process improvement tools
- Quality function deployment
By implementing this comprehensive quality control framework, organizations can ensure that their impact resistant gloves consistently deliver the expected protection, durability, and performance. This systematic approach minimizes safety risks, reduces costly rework or returns, and ultimately provides reliable protection for workers facing impact hazards in demanding industrial environments.
How to Find a Reliable OEM Impact Resistant Gloves Factory in China, Vietnam, or India?
Finding a dependable OEM impact resistant gloves manufacturer in Asia’s primary manufacturing regions requires a strategic approach that balances quality, capability, and cost considerations. Each region offers distinct advantages and challenges that procurement teams should carefully evaluate against their specific requirements.
Comparative Overview of Manufacturing Regions
Before initiating your search, understanding the strengths and limitations of each manufacturing hub will help focus your efforts:
Factor | China | Vietnam | India |
---|---|---|---|
Manufacturing Maturity | Highly developed with decades of experience in advanced safety products | Rapidly developing with growing technical capability | Established textile tradition with emerging technical capabilities |
Technical Expertise | Extensive experience with specialized materials and complex designs | Growing expertise, particularly in established processes | Strong in textile production with developing technical capabilities |
Quality Management Systems | Well-established, with many factories maintaining international certifications | Improving, with larger facilities achieving certification | Variable, with export-oriented facilities maintaining better systems |
Production Scale | From small workshops to massive facilities capable of millions of units | Mid-sized operations predominate, with growing capacity | Range from cottage industry to large export-oriented facilities |
Cost Structure | Higher than other regions but often offset by efficiency and quality | Competitive labor rates with moderate overhead costs | Generally lowest overall cost structure but often with productivity tradeoffs |
Supply Chain Integration | Comprehensive local supply chains for all components | Developing supply chains, often requiring some imported materials | Less integrated supply chains for technical components |
Intellectual Property Protection | Improving but still requires careful management | Generally good with proper agreements | Generally respected with established manufacturers |
Export Infrastructure | Excellent with efficient logistics and shipping options | Good and improving, with established trade routes | Adequate but sometimes less efficient than other regions |
Identification Strategies for Each Region
Different approaches prove most effective depending on the manufacturing region:
Finding Manufacturers in China
China remains the global leader in impact resistant glove manufacturing, with several approaches to identify qualified suppliers:
- Industry-Specific Trade Shows:
- China International Occupational Safety & Health Exhibition (COS+H)
- China (Shanghai) International Personal Protective Equipment Expo
- Canton Fair (China Import and Export Fair)
- Digital B2B Platforms with Verification:
- Made-in-China.com: Features verified suppliers with factory audits
- GlobalSources.com: Offers supplier verification and detailed company profiles
- Alibaba.com: Use Gold Suppliers with verification and Trade Assurance
- Verified suppliers with factory audits
- Those with relevant certifications (ISO 9001, CE mark capabilities)
- Minimum operating history (5+ years recommended)
- Export experience to your region
- Industry Association Resources:
- China Safety Protection Equipment Industry Association
- China National Textile and Apparel Council
- Local commerce departments in manufacturing centers like Zhejiang, Guangdong, and Shandong
- Regional Manufacturing Clusters:
China’s production tends to concentrate in specific regions:- Shandong Province (where Qingdao Snell is based): Known for technical work gloves
- Zhejiang Province: Specializes in advanced protective equipment
- Guangdong Province: Focus on export-oriented production
- Hebei Province: Emerging production center
Finding Manufacturers in Vietnam
Vietnam’s growing manufacturing sector requires somewhat different approaches:
- Industry Development Zones:
- Vietnam’s government has established specific industrial parks for safety equipment
- Focus on northern regions (around Hanoi) and southern regions (near Ho Chi Minh City)
- Contact zone administration offices for manufacturer listings
- Vietnamese Trade Promotion Agencies:
- Vietnam Trade Promotion Agency (Vietrade)
- Vietnam Textile and Apparel Association (VITAS)
- Local Departments of Industry and Trade
- International Contractor Networks:
- Many international brands have established production in Vietnam
- Industry networks can provide referrals to qualified subcontractors
- Foreign chambers of commerce in Vietnam maintain member directories
- Specialized Sourcing Agents:
- Local agents with industry-specific experience
- International sourcing companies with Vietnamese offices
- Quality control firms that can recommend reliable partners
Finding Manufacturers in India
India’s diverse manufacturing landscape requires targeted approaches:
- Regional Manufacturing Centers:
- Tamil Nadu: Textile manufacturing stronghold
- Maharashtra: Industrial production center
- Gujarat: Growing technical textile hub
- Indian Industry Associations:
- Safety Appliances Manufacturers Association of India
- Federation of Indian Chambers of Commerce and Industry
- Textile Machinery Manufacturers’ Association
- Government Export Promotion Councils:
- Federation of Indian Export Organizations
- Apparel Export Promotion Council
- Export Promotion Council for Handicrafts (includes technical textiles)
- Industrial Development Corporations:
- State-level industrial development corporations
- Special Economic Zone administrators
- National Small Industries Corporation
Qualification and Verification Process
Regardless of region, a structured qualification process is essential for identifying reliable partners:
- Initial Screening Criteria:
- Minimum operating history (5+ years recommended)
- Relevant certifications (ISO 9001, ISO 14001, OHSAS 18001/ISO 45001)
- Product certifications (CE mark, compliance with EN 388, ANSI/ISEA 138)
- Export experience to your target market
- Minimum production capacity aligned with your needs
- English communication capability (or translator availability)
- Documentation Review:
- Business licenses and registration verification
- Product certification documentation
- Test reports from accredited laboratories
- Client references (preferably in your region or industry)
- Banking references for financial stability
- Quality management system certification
- Communication Assessment:
- Response time to inquiries
- Comprehensiveness of information provided
- Technical knowledge demonstrated
- Transparency about capabilities and limitations
- Willingness to provide samples and references
- Sample Evaluation Process:
- Request both standard and custom samples
- Assess both product quality and packaging
- Conduct or commission laboratory testing
- Compare samples from multiple suppliers
- Evaluate consistency between samples
- On-Site Audit (or Third-Party Audit):
For final qualification, either conduct or commission:- Manufacturing capability assessment
- Quality management system verification
- Social compliance evaluation
- Environmental management review
- Production capacity confirmation
Key Questions to Ask Potential Suppliers
Specific inquiries help identify truly capable manufacturers:
Technical Capability Questions:
- “What impact protection standards can you certify to, and what documentation can you provide?”
- “Do you conduct in-house impact testing, or do you use third-party laboratories?”
- “What materials do you use for impact protection, and why have you selected these?”
- “Can you modify impact protection patterns for specific applications, and what is your design process?”
- “What is your experience with combined protection (impact + cut, chemical, etc.)?”
Manufacturing Process Questions:
- “What production processes are automated versus manual in your facility?”
- “How do you ensure consistency between production runs?”
- “What quality control points exist throughout your manufacturing process?”
- “What is your typical defect rate, and how do you address quality issues?”
- “What is your production capacity for impact resistant gloves specifically?”
Business Practice Questions:
- “What are your standard payment terms for new customers?”
- “What is your sample development process and timeframe?”
- “How do you handle intellectual property protection for custom designs?”
- “What are your minimum order quantities and how flexible are these?”
- “What is your typical lead time from order to shipment?”
Red Flags and Warning Signs
Watch for these indicators of potentially problematic suppliers:
- Reluctance to provide factory addresses or allow visits
- Unwillingness to sign NDA agreements
- Inability to provide test reports from recognized laboratories
- Substantially lower pricing than other qualified suppliers
- Claiming to manufacture everything (indicating trading company rather than factory)
- Delayed or incomplete responses to technical questions
- No established quality management system
- Unwillingness to provide client references
- Pressure to place orders without adequate samples or verification
- Discrepancies between company claims and verifiable information
Building Effective Supplier Relationships
Once you’ve identified promising manufacturers, these approaches help establish productive partnerships:
- Start with Smaller Test Orders:
- Begin with manageable quantities to evaluate performance
- Progressively increase volumes as confidence grows
- Clearly communicate this development path to suppliers
- Develop Detailed Specifications:
- Provide comprehensive technical requirements
- Establish clear quality standards and acceptance criteria
- Document all agreements in writing
- Translate critical documents into local language when necessary
- Implement Regular Communication:
- Establish consistent communication schedules
- Use video conferences for technical discussions
- Document key decisions and agreements
- Address issues promptly and directly
- Conduct Periodic Assessments:
- Schedule regular supplier evaluations
- Provide constructive feedback
- Acknowledge improvements and successes
- Develop improvement plans collaboratively
- Consider Local Representation:
- Engage local quality representatives for regular oversight
- Utilize third-party inspection services
- Develop relationships with local support resources
- Consider establishing a local office for significant volumes
Regional-Specific Considerations
Each manufacturing region presents unique considerations for successful partnerships:
China-Specific Factors:
- Relationships (guanxi) remain important despite business modernization
- Lunar New Year production disruptions require advanced planning
- Intellectual property protection requires explicit agreements
- Regional government relationships often influence factory operations
- Tier 1 manufacturers like Qingdao Snell typically offer more stability and consistency
Vietnam-Specific Factors:
- Rapidly developing regulatory environment requires monitoring
- Strong relationship focus with emphasis on trust building
- Growing but still developing technical capabilities
- Strong work ethic and commitment to agreements
- Increasing focus on environmental and social responsibility
India-Specific Factors:
- Significant regional variations in business practices
- Complex regulatory environment that may affect timelines
- Strong English language capabilities facilitate communication
- Relationship-oriented business culture values personal connections
- May require more detailed specifications and oversight
By implementing these structured approaches to manufacturer identification, qualification, and relationship development, procurement teams can identify reliable OEM impact resistant glove factories that meet their specific requirements for quality, capacity, and cost-effectiveness. This systematic process minimizes risk while establishing sustainable supply partnerships with manufacturers capable of supporting your safety equipment needs.
Compliance and Certifications Required for Impact Resistant Gloves in Different Markets
Navigating the complex landscape of international safety standards and certifications is crucial when sourcing impact resistant gloves. Different regions maintain distinct regulatory frameworks, and meeting these requirements is essential for both legal compliance and effective worker protection. This comprehensive overview will guide procurement specialists through the certification maze across major global markets.
North American Certification Requirements
The United States and Canada have established specific standards for impact resistant hand protection:
ANSI/ISEA 138-2019 (United States)
This relatively new American National Standards Institute standard specifically addresses impact protection:
- Testing Methodology: Measures transmitted force when a standardized weight is dropped on specific locations of the glove
- Protection Levels: Level Maximum Transmitted Force Typical Applications Level 1 ≤ 9 kN Light duty, moderate impact hazards Level 2 ≤ 6.5 kN Medium duty, significant impact risks Level 3 ≤ 4 kN Heavy duty, severe impact hazards
- Testing Areas: Back of hand, fingers, and thumb are tested separately with the lowest performance area determining the overall rating
- Documentation Requirements:
- Test reports from accredited laboratories
- Product marking showing compliance level
- User information regarding protection limitations
- Regulatory Status: Not legally mandated but increasingly specified by employers and safety professionals; often referenced in OSHA compliance programs
Other Relevant US Standards:
- ANSI/ISEA 105-2016: Complementary standard addressing cut, puncture, and abrasion resistance
- NFPA 2112: For flame-resistant gloves in certain applications
- OSHA Requirements: While OSHA doesn’t mandate specific certifications, employers must provide appropriate PPE for identified hazards, making standards like ANSI/ISEA 138 effectively required in many workplaces
Canadian Requirements:
- CSA Z96-15: Canadian Standards Association standard for hand protection
- Provincial Regulations: Individual provinces may have specific requirements through their occupational health and safety regulations
- Harmonization: Increasingly aligned with US standards, with ANSI/ISEA standards widely accepted
European Union Certification Framework
The EU maintains one of the most comprehensive regulatory systems for personal protective equipment:
EN 388:2016+A1:2018 (European Standard)
The fundamental standard for protective gloves against mechanical risks, recently updated to include impact protection:
- Testing Methodology: Incorporates multiple tests for different protection aspects:
- Abrasion resistance (0-4 scale)
- Blade cut resistance (0-5 scale)
- Tear resistance (0-4 scale)
- Puncture resistance (0-4 scale)
- ISO cut resistance (A-F scale)
- Impact protection (P for pass, no marking for fail)
- Impact Testing: To achieve the “P” marking, transmitted force must be less than 7 kN with no single result above 9 kN
- Marking Requirements: Results displayed as pictogram with 6 digits/letters (e.g., EN 388:2016 4544EP)
CE Marking and PPE Regulation
The overarching European regulatory framework for all personal protective equipment:
- Regulation (EU) 2016/425: Governs all personal protective equipment including impact resistant gloves
- Classification: Impact gloves typically fall under Category II (intermediate risk) requiring:
- EU type examination by notified body
- Declaration of Conformity
- CE marking on product
- User instructions in appropriate languages
- Technical File Requirements:
- Comprehensive product description
- Risk assessment
- Essential health and safety requirements checklist
- Test reports from accredited laboratories
- User information content
- Quality assurance documentation
- Authorized Representative: Non-EU manufacturers must designate an EU representative responsible for compliance
Asia-Pacific Regional Requirements
Major markets in the Asia-Pacific region have established their own certification systems:
Australia and New Zealand:
- AS/NZS 2161.3:2005: Largely harmonized with earlier versions of EN 388
- Updates Pending: Expected to align with current EN 388:2016 including impact requirements
- Regulatory Framework: Operates under Work Health and Safety Regulations
Japan:
- JIS T8116: Japanese Industrial Standard for protective gloves
- PSC Mark: Product Safety Consumer mark required for certain categories
- Acceptance of International Standards: Often recognizes EN and ISO certifications
China:
- GB/T 12624: National standard for protective gloves against mechanical risks
- CCC Certification: May be required for certain categories of safety equipment
- Trend Toward Harmonization: Increasingly aligning with ISO and EN standards
International Standards
Global standards provide harmonized approaches that are increasingly recognized across multiple jurisdictions:
ISO 21420:2020:
- General requirements for protective gloves (successor to EN 420)
- Covers ergonomics, construction, sizing, marking, and information for users
- Serves as the foundation standard for all protective gloves
ISO 11999-3:2015:
- Specific requirements for firefighters’ gloves with impact protection elements
- More specialized than general industrial impact protection standards
Industry-Specific Requirements
Certain industries maintain additional certification requirements beyond general standards:
Industry | Additional Certifications | Special Requirements |
---|---|---|
Oil & Gas | NORSOK S-002 (Norway)Operator-specific standards | Enhanced impact protectionHydrocarbon resistanceFlame retardancy |
Mining | AS/NZS 2161.3 (Australia)Mine Safety and Health Administration (US) | Heavy-duty impact protectionEnhanced visibilityExtended coverage |
Construction | EN 388 + Safety Scheme in Procurement (UK)OSHA Construction regulations (US) | Combined cut + impactWeather resistanceMaterial compatibility |
Automotive | Company-specific standardsAutomotive Industry Action Group guidelines | Precision dexterityOil resistanceCustomized impact zones |
Testing and Certification Process
Understanding the certification pathway helps procurement teams evaluate supplier capabilities:
- Pre-Certification Development:
- Design optimization for standard compliance
- Material selection for performance requirements
- Prototype development and internal testing
- Design modifications based on preliminary results
- Laboratory Selection:
- Accredited for relevant standards
- Recognized by target market authorities
- Experienced with impact protection testing
- Independent from manufacturer
- Testing Submission Requirements:
- Sample quantities (typically 3-12 pairs depending on standard)
- Technical documentation
- Test specification identification
- Pre-conditioning requirements
- Testing Process:
- Sample conditioning according to standard
- Performance testing per specified methods
- Documentation of results
- Comparison against standard requirements
- Certification Documentation:
- Test reports
- Certificates of conformity
- Technical files
- Declarations of compliance
- Ongoing Compliance:
- Production sample testing
- Quality assurance documentation
- Periodic recertification
- Monitoring of regulatory changes
Verification of Supplier Certification Claims
Procurement teams should implement these verification practices:
- Document Authentication:
- Verify testing laboratory accreditation
- Confirm certificate authenticity with issuing bodies
- Check certificate date validity
- Ensure test reports match claimed performance levels
- Sample Verification Testing:
- Commission independent testing of production samples
- Compare results to supplier claims
- Verify consistency between batches
- Test against specific standards for target markets
- Regulatory Database Checks:
- EU NANDO database for notified bodies
- OSHA-accepted testing laboratory verification
- Certification body registries
- Common Red Flags:
- Certificates without specific product identification
- Test reports without detailed methodology description
- Claims of certification to obsolete standards
- Discrepancies between certificate scope and product claims
Maintaining Certification Compliance
After initial certification, ongoing compliance requires:
- Change Management:
- Recertification when materials or designs change
- Impact assessment of manufacturing process modifications
- Documentation updates for product revisions
- Communication of changes to certification bodies
- Regulatory Monitoring:
- Tracking standard revisions and updates
- Monitoring transition periods for new requirements
- Preparing for upcoming regulatory changes
- Participating in industry associations for advance notice
- Quality Assurance Integration:
- Incorporating certification requirements into QA procedures
- Regular verification of production against certified specifications
- Documented compliance checks in production
- Traceability between certified samples and production
- Documentation Management:
- Maintaining current certificates and test reports
- Organizing technical files by market and product
- Ensuring accessibility of compliance documentation
- Regular review of documentation validity
Strategic Approaches to Multi-Market Certification
For organizations operating across multiple regions, these strategies optimize certification efficiency:
- Hierarchical Certification Strategy:
- Certify to the most stringent applicable standard
- Leverage mutual recognition agreements where available
- Use modular certification approaches for market-specific requirements
- Maintain core documentation adaptable to multiple markets
- Certification Portfolio Management:
- Map certification requirements against target markets
- Prioritize certifications based on market importance
- Schedule coordinated testing for multiple certifications
- Leverage relationships with multinational certification bodies
- Supplier Selection Based on Certification Capabilities:
- Evaluate supplier experience with target market certifications
- Assess in-house regulatory expertise
- Verify relationships with accredited testing laboratories
- Review history of successful certifications
- Cost Optimization Approaches:
- Combined testing programs for multiple standards
- Staged certification approach prioritizing key markets
- Internal pre-testing to ensure first-time certification success
- Long-term relationships with testing laboratories for preferred pricing
Leading manufacturers like Qingdao Snell maintain comprehensive certification programs supporting multiple international markets, with dedicated regulatory specialists ensuring ongoing compliance across evolving standards. Their established relationships with accredited testing laboratories and experience with multiple certification pathways provide significant advantages for multinational procurement programs requiring consistent compliance across diverse regulatory environments.
By thoroughly understanding the certification landscape for impact resistant gloves, procurement teams can ensure their selected products meet all applicable regulatory requirements while providing appropriate protection for their specific workplace hazards. This knowledge also enables more effective supplier evaluation and risk management throughout the procurement process.