OEM Work Gloves Factory: Ultimate Guide to Cut Resistant Sleeves Exporter in 2025
May 10, 2025
Share This Article
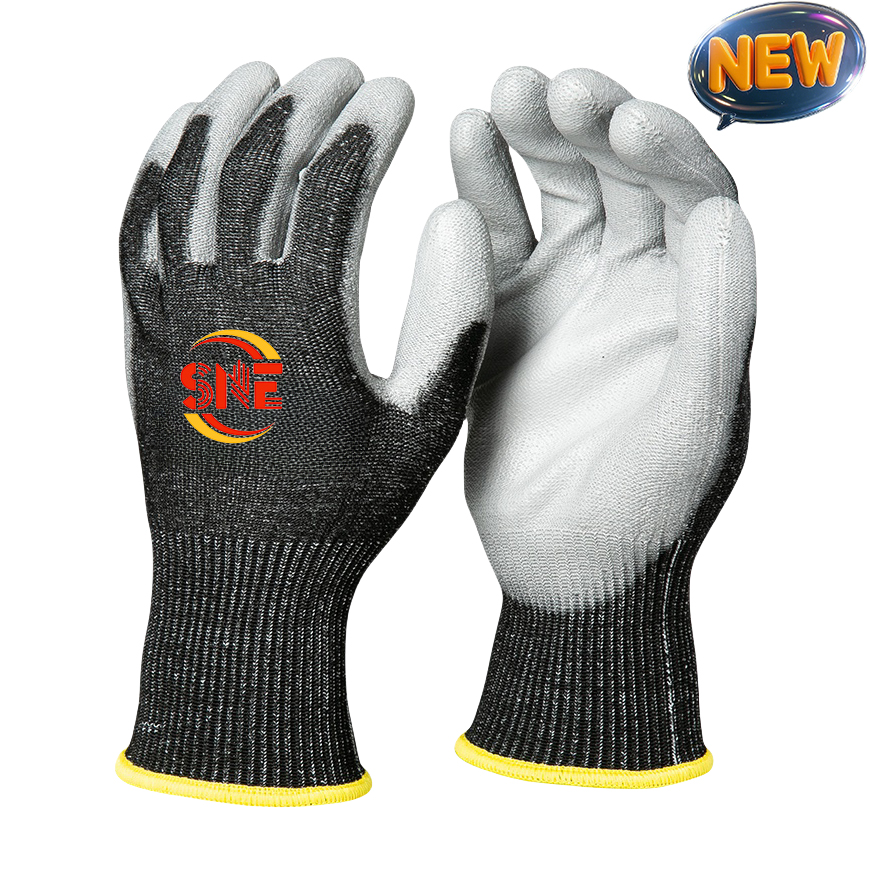
In today’s industrial landscape, worker safety remains a paramount concern for businesses across various sectors. As the demand for specialized protective equipment continues to rise, cut resistant sleeves have emerged as essential safety gear in industries ranging from manufacturing to food processing. This comprehensive guide explores everything you need to know about finding and working with a reliable cut resistant sleeves exporter in 2025.
What Are Cut Resistant Sleeves?
Cut resistant sleeves are specialized protective armwear designed to shield the wearer’s arms and forearms from cuts, abrasions, and punctures in hazardous work environments. Unlike traditional work gloves that only protect the hands, these sleeves extend protection from the wrist to the upper arm or even the shoulder, depending on the design.
These protective sleeves are engineered using advanced materials such as high-performance polyethylene (HPPE), Kevlar, fiberglass, and steel or metal fibers. By combining these materials through innovative knitting techniques, manufacturers create sleeves that offer varying levels of cut resistance while maintaining comfort and dexterity for the wearer.
Cut resistant sleeves typically feature an ANSI/ISEA or EN 388 rating that indicates their level of protection against cuts. The higher the rating, the greater the cut resistance. These ratings help businesses select the appropriate sleeves based on the specific hazards present in their work environment.
Modern cut resistant sleeves often incorporate additional features such as:
- Antimicrobial treatments to prevent odor and bacterial growth
- Moisture-wicking properties to keep arms dry and comfortable
- Heat-resistant materials for protection in high-temperature environments
- Thumb holes or elastic cuffs to prevent the sleeve from riding up during use
- Adjustable fasteners for a secure fit
- UV protection for outdoor applications
The versatility and specialized protection of cut resistant sleeves make them indispensable in industries that involve handling sharp objects, machinery with moving parts, glass, metal, or any materials that pose cutting hazards to workers’ arms.
How to Choose the Best Cut Resistant Sleeves for Your Business?
Selecting the right cut resistant sleeves for your specific business needs requires careful consideration of several factors. Making an informed decision can significantly impact worker safety, productivity, and your company’s bottom line.
Assess Your Risk Level
Begin by conducting a thorough risk assessment of your workplace. Identify the specific hazards that workers face:
- What types of sharp objects or materials are being handled?
- What is the likelihood of contact with these hazards?
- What is the potential severity of injuries that could occur?
This assessment will help determine the required cut resistance level for your sleeves.
Understand Cut Resistance Ratings
Cut resistant sleeves are rated according to standardized testing methods:
- ANSI/ISEA 105: The American standard rates cut resistance on a scale from A1 (lowest) to A9 (highest).
- EN 388: The European standard uses a scale from 1 (lowest) to 5 (highest) for cut resistance.
For high-risk environments involving sharp metals or glass, you’ll want to consider sleeves with ANSI A4-A7 ratings or EN 388 level 5. For medium-risk tasks like packaging or assembly, A2-A3 or EN 388 level 3-4 might suffice.
Consider Material Composition
Different materials offer varying benefits:
- HPPE (High-Performance Polyethylene): Lightweight, comfortable, and offers excellent cut resistance
- Kevlar: Strong heat resistance along with cut protection
- Fiberglass: Enhances cut resistance but can cause skin irritation for some users
- Steel/Metal Fibers: Provide maximum protection but add weight and reduce flexibility
Many modern cut resistant sleeves feature blended materials to optimize both protection and comfort.
Evaluate Comfort and Fit
Even the most protective sleeves won’t be effective if workers find them uncomfortable and remove them. Consider:
- Length requirements (wrist to upper arm or full arm)
- Breathability and temperature regulation
- Flexibility and range of motion
- Elastic or adjustable features for secure fit
- Weight and overall comfort during extended wear
Check for Additional Features
Depending on your workplace conditions, you might need sleeves with:
- UV protection for outdoor work
- Antimicrobial properties for food processing
- Chemical resistance for handling hazardous substances
- Heat resistance for high-temperature environments
- Visibility features like high-visibility colors or reflective strips
Test Before Bulk Purchasing
Request samples from potential suppliers and have your workers test them in real working conditions before committing to a large order. This practical evaluation will reveal any issues with comfort, durability, or protection that might not be apparent from specifications alone.
By carefully evaluating these factors, you can select cut resistant sleeves that provide the optimal balance of protection, comfort, and value for your specific business needs.
Where to Buy Cut Resistant Sleeves in 2025?
Finding reliable sources for high-quality cut resistant sleeves is crucial for maintaining workplace safety standards. In 2025, businesses have multiple procurement options, each with distinct advantages.
Direct from Manufacturers
Purchasing directly from manufacturers offers several benefits:
- Competitive pricing through elimination of middlemen
- Direct communication with technical experts
- Customization options for specific requirements
- More reliable quality assurance
Leading manufacturers like Qingdao Snell Protective Products Co., Ltd. have established themselves as trusted sources for cut resistant sleeves. With over a decade of expertise in protective equipment manufacturing, Snell offers competitive pricing and customizable solutions tailored to various industries.
Online B2B Marketplaces
Global B2B platforms have transformed how businesses source safety equipment:
- Alibaba: Offers access to thousands of global suppliers with detailed product specifications
- Global Sources: Features verified suppliers with third-party quality assessments
- Made-in-China: Specializes in connecting international buyers with Chinese manufacturers
- ThomasNet: Focuses on North American industrial suppliers with detailed vetting
These platforms typically offer supplier verification systems, secure payment options, and dispute resolution mechanisms to minimize procurement risks.
Specialized Safety Equipment Distributors
Distributors focusing exclusively on safety equipment provide:
- Expert guidance on product selection
- Consolidated sourcing for various safety products
- Value-added services like safety audits and training
- Faster delivery for urgent requirements
Major safety equipment distributors like Grainger, MSC Industrial, and Fastenal maintain extensive inventories of cut resistant sleeves from multiple manufacturers.
Regional Trade Shows and Exhibitions
Industry-specific trade shows remain valuable sourcing venues where you can:
- Physically examine product samples
- Compare multiple suppliers side-by-side
- Negotiate deals directly with vendor representatives
- Stay updated on the latest safety technology innovations
Notable safety equipment exhibitions include:
- A+A Safety in Düsseldorf, Germany
- National Safety Council Congress & Expo in the US
- China International Occupational Safety & Health Exhibition
Industry-Specific Cooperative Purchasing
Many industry associations offer cooperative purchasing programs that:
- Leverage the collective buying power of members
- Pre-vet suppliers for quality and reliability
- Negotiate advantageous terms and pricing
- Simplify the procurement process
Before finalizing your purchase, consider requesting samples from potential suppliers. Testing cut resistant sleeves in your specific work environment provides valuable insights about their performance, comfort, and durability that specifications alone cannot convey.
Cut Resistant Sleeves Manufacturers in China
China stands as the global manufacturing powerhouse for personal protective equipment, including cut resistant sleeves. The country’s manufacturing landscape offers a unique combination of competitive pricing, production capacity, and increasingly sophisticated quality management systems.
Leading Chinese Manufacturers
Chinese manufacturers range from large-scale factories with international certifications to smaller specialized workshops. Here’s an overview of some notable players:
Qingdao Snell Protective Products Co., Ltd. has established itself as a premier manufacturer of cut resistant sleeves and other protective gloves. Founded in 2024, Snell operates two advanced manufacturing facilities in Gaomi and Nantong, featuring six production lines dedicated to creating high-performance protective gear. The company’s products are CE certified and ISO 9001 compliant, ensuring consistent quality and safety standards.
Snell specializes in cut-resistant sleeves using advanced materials like HPPE, Kevlar, and proprietary blends that offer superior protection while maintaining comfort and dexterity. With their factory-direct supply model, Snell eliminates middlemen to provide competitive pricing without compromising on quality. Their minimum order quantity ranges from 3,000 to 20,000 units, making them accessible to both medium and large-scale businesses.
Other notable Chinese manufacturers include:
- Shanghai Safety Products: Specializes in high-performance cut resistant sleeves with ANSI A7-A9 ratings, catering primarily to heavy industrial applications
- Guangzhou Protective Gear: Known for their cost-effective options with innovative cooling technologies for comfort in hot working conditions
- Hebei Safeguard Equipment: Produces sleeves with integrated antimicrobial treatments, popular in food processing industries
Manufacturing Capabilities and Technology
Chinese manufacturers have made significant technological advancements in recent years:
- Implementation of automated knitting machines that ensure consistent fiber distribution and cut resistance
- Advanced testing laboratories for in-house verification of cut resistance levels
- Innovative material blending technologies that optimize protection, comfort, and cost
- Enhanced quality control systems using computer vision and AI for defect detection
Certification and Compliance Standards
Reputable Chinese manufacturers maintain rigorous certification protocols:
- ISO 9001 quality management systems
- CE certification for European market access
- Compliance with ANSI/ISEA 105 and EN 388 testing standards
- REACH and OEKO-TEX certifications for chemical safety
- FDA compliance for food-contact applications
Sourcing Considerations
When working with Chinese manufacturers, consider these factors:
- Request detailed documentation of testing results and certifications
- Evaluate their export experience and understanding of your market’s regulatory requirements
- Consider time zone differences and communication protocols
- Understand lead times, including production and shipping durations
- Assess their willingness to provide samples and small trial orders before committing to larger quantities
Production Capacity and Flexibility
Many Chinese manufacturers offer considerable flexibility in production capabilities:
- Ability to scale production from several thousand to millions of units
- Customization options for sleeve length, materials, and additional features
- Private labeling and packaging services
- Seasonal production planning for industries with fluctuating demand
The combination of advanced manufacturing capabilities, competitive pricing, and increasing quality focus makes Chinese manufacturers compelling partners for businesses seeking reliable cut resistant sleeve suppliers in 2025.
What to Look for in a Reliable Cut Resistant Sleeves Exporter?
Selecting the right cut resistant sleeves exporter is crucial for ensuring consistent product quality, regulatory compliance, and supply chain reliability. Here’s what to prioritize when evaluating potential export partners:
Proven Quality Management Systems
A reputable exporter should demonstrate robust quality management through:
- ISO 9001 certification or equivalent quality management system
- Dedicated quality control departments with trained personnel
- Systematic inspection procedures at multiple production stages
- Statistical process control methods to maintain consistent quality
- Regular calibration of testing equipment
- Comprehensive documentation of quality testing results
Quality assurance becomes particularly critical with safety equipment like cut resistant sleeves, where product failure could result in serious injuries.
Regulatory Compliance Expertise
Your exporter should possess thorough knowledge of international safety standards and regulations:
- Familiarity with ANSI/ISEA 105 and EN 388 cut resistance testing methods
- Understanding of region-specific certification requirements
- Experience with documentation needed for customs clearance
- Compliance with chemical safety regulations like REACH in Europe
- Knowledge of labeling requirements in target markets
This expertise ensures that imported products will meet all legal requirements in your region, preventing costly delays or rejections at customs.
Manufacturing Capabilities Assessment
Evaluate the exporter’s production capacity and technological capabilities:
- Production equipment type and age
- Technical expertise of engineering and production staff
- Research and development investments
- Material sourcing relationships and quality control
- Production capacity and flexibility
Manufacturers with advanced capabilities like Qingdao Snell typically produce more consistent and innovative products. With their six dedicated production lines and specialized expertise in protective gear manufacturing, Snell exemplifies the manufacturing prowess businesses should seek in an export partner.
Track Record and Reputation
Investigate the exporter’s history and standing in the industry:
- Years in business and export experience
- Client testimonials and references
- Industry certifications and awards
- Presence at major trade shows
- Membership in relevant industry associations
A company with a solid reputation has typically earned it through consistent performance and reliability.
Communication and Responsiveness
Effective communication is essential for successful international business relationships:
- Response time to inquiries and issues
- English proficiency of key personnel
- Availability during your business hours
- Transparency about production challenges or delays
- Willingness to provide regular production updates
Clear, prompt communication prevents misunderstandings and helps address issues before they become problems.
Financial Stability
Verify the financial health of potential export partners:
- Business registration and legal status
- Bank references and credit reports
- Payment terms flexibility
- Export insurance coverage
- Business continuity planning
Financial stability reduces the risk of supply disruptions due to business failures or cash flow problems.
Sample Assessment Process
Always request and thoroughly evaluate product samples:
- Testing for compliance with specified cut resistance ratings
- Comfort and ergonomics evaluation
- Durability through accelerated wear testing
- Consistency between samples and specifications
- Packaging quality and labeling accuracy
Comprehensive sample testing provides tangible evidence of the exporter’s capabilities and product quality.
By methodically evaluating exporters against these criteria, you can identify reliable partners who will consistently deliver high-quality cut resistant sleeves that meet your safety requirements and business needs.
MOQ Considerations When Ordering Cut Resistant Sleeves
Understanding minimum order quantity (MOQ) requirements is crucial when sourcing cut resistant sleeves from manufacturers. This aspect of procurement significantly impacts cost efficiency, inventory management, and supplier relationships.
Understanding Standard MOQ Requirements
MOQ requirements can vary substantially based on several factors:
- Manufacturer Size: Larger manufacturers typically set higher MOQs than smaller operations
- Production Technology: Advanced automated production often requires larger batch sizes for efficiency
- Material Specialization: Sleeves made with specialized or premium materials may have higher MOQs
- Customization Level: Custom designs, colors, or features generally increase minimum quantities
- Geographic Location: Manufacturers in different regions operate with different economies of scale
For context, Qingdao Snell Protective Products Co., Ltd. sets MOQs ranging from 3,000 to 20,000 units, which aligns with industry standards for quality manufacturers. This range accommodates both medium-sized businesses and large industrial clients with varying volume needs.
Negotiating Favorable MOQ Terms
Even when faced with high MOQs, experienced procurement professionals can often negotiate more favorable terms:
- Mixed Product Orders: Combine different product types to reach the total MOQ while ordering smaller quantities of each specific item
- Blanket Purchase Agreements: Commit to purchasing a large quantity over time with scheduled deliveries
- Staged Production Runs: Arrange for production in phases with conditional agreements for subsequent batches
- Sample Orders: Request a smaller initial order at a premium price to test product quality and market acceptance
- Cooperative Purchasing: Partner with other businesses to place combined orders that meet MOQ requirements
Cost Implications of MOQ Decisions
Understanding the relationship between order quantity and unit pricing helps optimize procurement decisions:
Order Quantity | Typical Price Discount | Setup Cost Amortization | Shipping Cost per Unit | Inventory Carrying Cost |
---|---|---|---|---|
Below MOQ (if available) | None (often premium) | High | High | Low |
At MOQ | Standard pricing | Moderate | Moderate | Moderate |
2-3× MOQ | 5-10% discount | Low | Lower | Higher |
5× MOQ | 10-15% discount | Very low | Lowest | Highest |
These figures illustrate why manufacturers establish MOQs – the setup costs, material preparation, and production line configuration make small runs economically unfeasible without significant price premiums.
Balancing MOQ with Inventory Management
When evaluating MOQ requirements, consider these inventory management factors:
- Storage Capacity: Ensure sufficient warehouse space for larger orders
- Product Shelf Life: Even cut resistant sleeves can degrade over time, particularly those with elastic components
- Cash Flow Impact: Larger orders require more upfront capital but may reduce long-term costs
- Demand Forecasting: Assess whether your usage rate justifies meeting higher MOQs
- Obsolescence Risk: Consider the likelihood of product redesigns or safety standard changes that could make inventory obsolete
MOQ Strategies for Different Business Sizes
Your approach to MOQ should align with your organization’s scale and needs:
For Small Businesses:
- Consider working with distributors who purchase in bulk and resell in smaller quantities
- Explore manufacturer sample programs or trial orders
- Focus on standard products rather than customized solutions
- Join industry purchasing groups to leverage collective buying power
For Medium-Sized Operations:
- Negotiate phased delivery schedules to meet MOQs while spreading payments
- Balance inventory levels with order frequency
- Consider slight compromises on customization to reduce MOQs
- Develop relationships with manufacturers like Qingdao Snell that offer flexible MOQ options between 3,000-20,000 units
For Large Enterprises:
- Leverage volume for substantial price negotiations beyond standard MOQ discounts
- Implement vendor-managed inventory systems with key suppliers
- Establish long-term supply agreements with scheduled production runs
- Invest in direct relationships with manufacturers to eliminate middleman markups
By strategically approaching MOQ requirements, businesses of all sizes can secure quality cut resistant sleeves while optimizing their supply chain costs and inventory efficiency.
How to Customize Cut Resistant Sleeves with Your Logo and Branding?
Customized cut resistant sleeves offer dual benefits: enhancing workplace safety while reinforcing company identity. Proper branding transforms standard safety equipment into powerful marketing tools that promote safety culture and brand recognition simultaneously.
Branding Options for Cut Resistant Sleeves
Modern manufacturing techniques have expanded the range of customization possibilities:
Screen Printing
- Most cost-effective method for simple logos and designs
- Durable for industrial washing and regular use
- Best for single or limited color designs
- Works well on most sleeve materials
- Becomes more economical at higher quantities
Heat Transfer
- Allows for more detailed and multi-color designs
- Provides excellent color reproduction
- Suitable for photographic images or complex graphics
- Generally durable but may show wear after numerous wash cycles
- Cost-effective for medium-sized orders
Embroidery
- Creates a premium, professional appearance
- Exceptional durability that often outlasts the sleeve itself
- Allows for dimensional branding that stands out
- More expensive than printing methods
- May slightly reduce flexibility in the embroidered area
- Limited color transitions and detail in very small designs
Woven-In Branding
- Integrates your branding directly into the fabric during manufacturing
- Seamless appearance with no added layers
- Superior durability that doesn’t fade or wear off
- Requires higher minimum orders and longer lead times
- Limited color options depending on sleeve materials
Strategic Placement Considerations
The positioning of your branding elements impacts both visibility and durability:
- Forearm Placement: Most visible during work activities but experiences more abrasion
- Upper Arm: Better visibility when arms are lowered, less wear during use
- Cuff Area: Highly visible and experiences minimal abrasion
- Length-wise Placement: Creates a striking visual on extended sleeves
- Reflective Elements: Can incorporate branding while enhancing safety visibility
Customization Process with Manufacturers
Understanding the typical customization workflow helps set realistic expectations:
- Design Submission: Provide vector files (AI, EPS, PDF) of your logo with precise color specifications
- Material Selection: Choose sleeve material, color, and cut resistance level
- Customization Method: Select branding technique based on design complexity and budget
- Sample Approval: Review and approve physical samples before full production
- Production Timeline: Allow for additional lead time (typically 2-4 weeks) beyond standard production
Qingdao Snell Protective Products offers comprehensive customization services with their cut resistant sleeves. Their experienced design team works with clients to optimize logo placement and select appropriate branding methods based on specific industry requirements and usage patterns.
Compliance Considerations for Customized Sleeves
When adding branding elements, ensure they don’t compromise safety features:
- Verify that customization methods don’t affect cut resistance ratings
- Ensure ink compounds comply with skin contact safety regulations
- Confirm that branding doesn’t interfere with mobility or comfort
- Check that custom colors meet any industry visibility requirements
- Maintain all required safety certifications and labeling
Cost-Optimization Strategies for Custom Orders
Maximize your customization budget with these approaches:
- Simplify designs to reduce color count and production complexity
- Consolidate orders to meet higher MOQs for better pricing
- Consider standardized designs across multiple PPE items for visual consistency
- Balance premium branding methods with practical durability needs
- Evaluate the marketing value against incremental customization costs
Beyond Logo Placement: Advanced Customization
Forward-thinking companies are exploring additional customization options:
- Color-coded sleeves to indicate department or role
- QR codes linking to training materials or safety protocols
- Departmental or personal identification markings
- Motivational safety messages or company values
- Commemorative designs for safety milestones or company anniversaries
By thoughtfully approaching cut resistant sleeve customization, organizations can transform necessary safety equipment into valuable tools that simultaneously protect workers and reinforce brand identity.
What Are the Most Durable Materials for Cut Resistant Sleeves?
The durability and protective capacity of cut resistant sleeves are directly tied to their material composition. Understanding the properties of these materials helps businesses select the most appropriate options for their specific applications and work environments.
High-Performance Engineered Fibers
Modern cut resistant sleeves utilize several advanced materials, each with distinct properties:
High-Performance Polyethylene (HPPE)
- Offers excellent cut resistance at lighter weights
- Up to 15 times stronger than steel on an equal-weight basis
- Highly resistant to moisture, chemicals, and UV radiation
- Maintains flexibility and comfort even in extreme temperatures
- Excellent abrasion resistance for extended service life
- Non-irritating for sensitive skin
- Typical applications: Glass handling, sheet metal work, automotive assembly
Aramid Fibers (including Kevlar®)
- Outstanding cut and abrasion resistance
- Exceptional heat resistance (doesn’t melt, but chars at ~932°F/500°C)
- Natural flame-retardant properties
- High strength-to-weight ratio
- Moderate chemical resistance
- May degrade with prolonged UV exposure
- Typical applications: Metal stamping, hot glass handling, automotive manufacturing
UHMWPE (Ultra-High-Molecular-Weight Polyethylene)
- Superior cut resistance combined with exceptional comfort
- Extremely lightweight and flexible
- Excellent resistance to chemicals and moisture
- Naturally cool to the touch
- Not suitable for high-temperature applications
- Excellent durability and wash resistance
- Typical applications: Food processing, precision assembly, packaging
Composite and Blended Materials
Most high-performance cut resistant sleeves utilize material blends to optimize performance:
Steel/Fiberglass Reinforced Composites
- Incorporate stainless steel or fiberglass strands for enhanced cut resistance
- Steel adds significant protection against direct cutting forces
- Fiberglass improves cut resistance without adding substantial weight
- Often combined with HPPE or aramid for comfort
- Can include spandex or elastane for flexibility and fit
- May cause irritation for some users if fibers are exposed
- Typical applications: Meat processing, metal fabrication, glass manufacturing
Engineered Yarn Combinations
- Proprietary blends that optimize protection, comfort, and cost
- Often combine multiple high-performance fibers
- Can incorporate specialized coatings for grip or chemical resistance
- Designed for specific industry applications
- Provide balanced performance characteristics
- Typical applications: Varied based on specific formulation
Comparative Material Performance
This table illustrates the relative performance of common cut resistant sleeve materials:
Material Type | Cut Resistance | Abrasion Resistance | Heat Resistance | Comfort | Chemical Resistance | Relative Cost | Durability |
---|---|---|---|---|---|---|---|
100% HPPE | High | Very High | Moderate | Excellent | Good | Moderate | Excellent |
Aramid (Kevlar) | High | High | Excellent | Good | Moderate | Higher | Very Good |
UHMWPE | Very High | High | Poor | Excellent | Excellent | Higher | Excellent |
HPPE/Steel Blend | Very High | High | Moderate | Good | Good | Moderate | Good |
HPPE/Glass Fiber | High | High | Moderate | Good | Good | Moderate | Good |
Engineered Composites | Very High | Very High | Varies | Very Good | Very Good | Higher | Excellent |
Material Selection Based on Industry Requirements
Different industries have specific material requirements for optimal protection:
Food Processing
- Food-safe materials free of contaminants
- Detectable fibers incorporating metal for food safety
- Materials that withstand frequent washing and sanitization
- Often UHMWPE or specialized blends that maintain performance when wet
Automotive Manufacturing
- Highly cut-resistant materials for handling sharp metal edges
- Oil-resistant compositions
- Comfort-focused blends for all-day wear
- Typically HPPE/glass fiber blends or engineered composites
Glass Handling
- Maximum cut resistance for protection against sharp edges
- Heat-resistant fibers for hot glass processing
- Often aramid blends or specialized engineered composites
Metal Fabrication
- Highest cut resistance ratings (ANSI A7-A9)
- Puncture-resistant compositions
- Heat-resistant materials for welding proximity
- Usually steel-reinforced composites or specialized aramid blends
By matching material properties to specific workplace hazards, businesses can provide optimal protection while ensuring comfort and durability—key factors in worker compliance with safety equipment requirements.
How to Ensure Quality Control About Cut Resistant Sleeves?
Implementing effective quality control measures is essential for businesses that rely on cut resistant sleeves to protect their workforce. A comprehensive quality assurance approach encompasses everything from initial supplier selection to ongoing performance evaluation.
Pre-Purchase Quality Verification
Before committing to a supplier, conduct thorough due diligence:
Certification Verification
- Request and validate all relevant certifications:
- ISO 9001 (Quality Management Systems)
- ISO 45001 (Occupational Health and Safety)
- Product-specific certifications (ANSI/ISEA 105, EN 388)
- Verify certification authenticity through accreditation bodies
- Check certification scope to ensure it covers the specific products being purchased
Laboratory Testing Documentation
- Request detailed testing reports showing:
- Cut resistance test methods and results
- Abrasion resistance performance
- Tear strength measurements
- Tensile strength data
- Wash/cleaning durability results
Manufacturing Facility Assessment
- If possible, arrange factory inspections to evaluate:
- Production environment cleanliness
- Quality control systems and testing equipment
- Staff training and expertise
- Material handling and storage practices
- In-process inspection procedures
Incoming Quality Inspection Protocols
Establish systematic inspection procedures for all received shipments:
Sampling Methods
- Implement statistical sampling based on AQL (Acceptable Quality Level) standards
- For critical safety items, consider increasing sampling rates above standard levels
- Document sampling procedures for consistency and accountability
Physical Inspection Checklist
- Visual examination for:
- Correct material composition
- Consistent coloration
- Proper sizing
- Even seams and stitching
- Accurate labeling
- Correct packaging
- Dimensional verification against specifications
- Weight verification to confirm material density
Performance Testing
- Conduct verification testing on samples from each lot:
- Basic cut resistance testing
- Fit and comfort evaluation
- Material integrity assessment
- Functionality of features (thumb holes, elastics, fasteners)
Ongoing Quality Monitoring
Quality control continues throughout the product lifecycle:
Usage Feedback System
- Implement structured feedback collection from users
- Track wear patterns, durability issues, and comfort concerns
- Document any protection failures or near-misses
- Create improvement recommendation loops with suppliers
Periodic Re-Testing
- Schedule regular re-testing of inventory samples
- Verify that stored products maintain their protective properties
- Assess performance after cleaning or environmental exposure
- Compare against original specifications to identify degradation
Supplier Performance Metrics
- Track key supplier quality indicators:
- Defect rates over time
- On-time delivery performance
- Consistency between production runs
- Responsiveness to quality concerns
- Transparency in addressing issues
Quality Assurance Partnerships with Manufacturers
Develop collaborative quality relationships with key suppliers:
Joint Quality Planning
- Establish shared quality objectives and metrics
- Develop specific quality specifications for your application
- Create mutual understanding of critical-to-quality characteristics
Continuous Improvement Initiatives
- Work with suppliers on targeted improvements
- Share field performance data to guide product enhancements
- Collaborate on testing new materials or designs
- Provide constructive feedback on quality issues
Transparent Communication Channels
- Establish direct contacts with supplier quality teams
- Create standardized quality report formats
- Define escalation procedures for serious quality concerns
- Schedule regular quality review meetings
Qingdao Snell Protective Products Co., Ltd. exemplifies best practices in quality control with their comprehensive quality management system. Their CE and ISO 9001 certified processes ensure consistent quality across all their cut resistant sleeves and other protective products. Their quality control includes multi-stage inspections, regular third-party testing, and continuous improvement initiatives based on customer feedback.
By implementing these quality control measures, businesses can ensure that the cut resistant sleeves they provide to their workforce deliver consistent protection and performance, minimizing safety risks and optimizing the return on their safety equipment investment.
How to Find a Reliable Cut Resistant Sleeves OEM Factory in Asia?
The search for a dependable OEM factory in Asia requires a methodical approach to navigate the diverse manufacturing landscape. Countries like China, Vietnam, and India offer distinct advantages, but finding the right partner demands careful research and evaluation.
Effective Research Strategies
Begin your search with these proven research methods:
Industry-Specific B2B Platforms
- Utilize specialized platforms focused on safety equipment
- Filter searches by manufacturing capabilities and certifications
- Look for verified supplier status and third-party assessments
- Evaluate detailed company profiles and product specifications
Trade Show Reconnaissance
- Attend major safety equipment exhibitions:
- A+A Safety (Germany)
- China International Occupational Safety & Health Exhibition
- National Safety Council Congress & Expo (USA)
- Safety & Health Expo (UK)
- Use these events to meet multiple potential suppliers efficiently
- Evaluate product quality firsthand and assess technical knowledge
Industry Association Resources
- Contact safety equipment manufacturing associations
- Request member directories with manufacturing specializations
- Leverage association vetting processes for quality assurance
- Utilize association translators or liaison services when necessary
Government Trade Resources
- Connect with commercial services at your country’s embassies
- Utilize export promotion agencies in target manufacturing countries
- Access government-vetted supplier databases
- Benefit from official translation and cultural navigation support
Comparative Evaluation of Manufacturing Regions
Asian manufacturing hubs offer different advantages for cut resistant sleeve production:
Manufacturing Region | Strengths | Considerations | Best For |
---|---|---|---|
Eastern China (Qingdao, Shanghai) | Advanced manufacturing technology, established quality systems, extensive experience with export regulations | Higher labor costs than other regions, longer lead times for customization | High-performance technical sleeves, complex designs, comprehensive certification requirements |
Southern China (Guangdong) | Strong supply chain integration, faster turnaround times, experienced with Western markets | Increasingly focused on higher-value products, rising costs | Mid to high-range products, designs requiring multiple specialized materials |
Vietnam | Competitive labor costs, growing technical capabilities, favorable trade agreements with many Western countries | Developing supply chains, potential capacity limitations for very large orders | Cost-effective standard designs, companies seeking alternatives to Chinese manufacturing |
India | Strong textile manufacturing tradition, competitive pricing, English language advantage | Variable quality systems, potentially longer lead times | Budget-conscious projects, standard designs with basic requirements |
Essential Vetting Criteria
Apply these criteria when evaluating potential manufacturing partners:
Manufacturing Capabilities Assessment
- Production capacity aligned with your volume requirements
- Equipment age and technological sophistication
- Material sourcing capabilities and relationships
- In-house testing facilities and equipment
- Research and development capacity for future innovations
Quality Management Systems
- Formal certification to ISO 9001 or equivalent standards
- Documented quality control procedures at each production stage
- Statistical process control implementation
- Traceability systems for materials and production batches
- Defect tracking and continuous improvement processes
Business Stability Indicators
- Years in operation and manufacturing history
- Factory ownership structure and financial stability
- Major client relationships and longevity
- Export experience to your specific market
- Investment in facilities and equipment
Compliance and Ethical Standards
- Workplace safety conditions and employee treatment
- Environmental management practices
- Transparency in material sourcing and production
- Adherence to local labor laws and regulations
- Willingness to accommodate third-party audits
Practical Evaluation Steps
Follow this sequential process to narrow your options efficiently:
- Initial Screening: Create a shortlist based on stated capabilities and certifications
- Documentation Review: Request and analyze product specifications, testing reports, and certifications
- Sample Evaluation: Order samples for hands-on assessment of quality and performance
- Video Factory Tours: If in-person visits aren’t feasible, request comprehensive video tours
- Reference Checks: Contact existing clients about reliability and quality consistency
- Trial Order: Place a small initial order to evaluate the entire process from production to delivery
Building Long-Term Manufacturing Partnerships
Once you’ve identified promising candidates, focus on relationship development:
- Clearly communicate your quality expectations and requirements
- Develop detailed product specifications and quality standards
- Establish regular communication protocols and key contacts
- Create mutually beneficial ordering patterns and forecasts
- Invest time in understanding cultural differences in business practices
- Consider periodic in-person visits to strengthen relationships
Among the reputable manufacturers in Asia, Qingdao Snell Protective Products Co., Ltd. stands out with their specialized focus on high-performance protective gear. Their extensive experience in manufacturing cut resistant sleeves, combined with their ISO 9001 and CE certifications, makes them a reliable partner for businesses seeking quality protection solutions. Their two manufacturing facilities in Gaomi and Nantong demonstrate their commitment to production capacity and quality control.
By applying these systematic evaluation processes, businesses can identify reliable OEM partners in Asia who provide consistent quality, competitive pricing, and dependable delivery of cut resistant sleeves.
Frequently Asked Questions About Cut Resistant Sleeves
General Questions About Cut Resistant Sleeves
Q: What exactly do cut resistant sleeves protect against?
A: Cut resistant sleeves are designed to protect the arms and forearms from cuts, abrasions, and punctures. They create a barrier between sharp objects (like metal edges, glass, blades) and the skin, reducing the risk of lacerations and other injuries. However, they are not completely cut-proof and have different levels of protection based on their rating.
Q: How do cut resistance ratings work?
A: Cut resistance is typically measured using either the ANSI/ISEA 105 standard (American) or the EN 388 standard (European). The ANSI standard ranges from A1 (lowest) to A9 (highest), while EN 388 rates cut resistance from 1-5. These ratings are determined through standardized testing that measures how much force is required to cut through the material with a specified testing apparatus.
Q: Can cut resistant sleeves be worn with gloves?
A: Yes, cut resistant sleeves are designed to complement cut resistant gloves. Many models feature thumb holes or other design elements specifically to ensure proper coverage when worn with gloves, eliminating the gap that might otherwise exist between sleeve and glove.
Material and Performance Questions
Q: Do cut resistant sleeves protect against heat as well as cuts?
A: Some cut resistant sleeves offer heat resistance, but it varies by material. Aramid fiber (Kevlar) sleeves provide good heat resistance, while HPPE sleeves offer minimal heat protection. For environments with both cutting and heat hazards, look for sleeves specifically rated for both cut and heat resistance.
Q: How long do cut resistant sleeves typically last?
A: The lifespan depends on material quality, frequency of use, and work conditions. High-quality sleeves made with engineered fibers like those from Qingdao Snell typically last 3-6 months with daily use in industrial environments. Lighter-duty applications may see 6-12 months of service life. Always replace sleeves that show signs of significant wear, cuts, or tears.
Q: Are cut resistant sleeves uncomfortable or hot to wear?
A: Modern cut resistant sleeves are engineered for comfort as well as protection. Many use breathable knit constructions that allow air circulation while maintaining protection. Some incorporate cooling technologies or moisture-wicking properties to enhance comfort. The perception of comfort varies by individual and application, which is why testing samples in your specific work environment is recommended.
Care and Maintenance Questions
Q: How should cut resistant sleeves be cleaned?
A: Cleaning instructions vary by material composition:
- Most HPPE and blended material sleeves can be machine washed in cold water with mild detergent
- Aramid fiber sleeves typically require gentle washing to maintain protection levels
- Air drying is generally recommended over machine drying
- Always follow the manufacturer’s specific care instructions
- Industrial environments may require specialized cleaning protocols
Q: Do cut resistant sleeves lose their protective properties after washing?
A: Quality cut resistant sleeves maintain their protective properties through multiple wash cycles when properly cleaned. However, improper washing (using bleach, hot water, or harsh chemicals) can degrade performance. Some reduction in cut resistance may occur gradually over many wash cycles. For critical safety applications, consider implementing a testing schedule to verify ongoing protection levels.
Purchasing and Business Considerations
Q: What is the typical price range for quality cut resistant sleeves?
A: Pricing varies based on materials, performance ratings, and quantities:
Protection Level | Small Order Price (per pair) | Bulk Order Price (1,000+ pairs) |
---|---|---|
Basic (ANSI A1-A2) | $8-15 | $5-10 |
Medium (ANSI A3-A4) | $12-20 | $8-15 |
High (ANSI A5-A7) | $18-30 | $12-22 |
Maximum (ANSI A8-A9) | $25-40 | $18-30 |
These ranges are approximate and may vary based on customization, additional features, and market conditions.
Q: What information should I provide when requesting a quote from a manufacturer?
A: To receive accurate quotes, provide:
- Required cut resistance level or specific hazard protection
- Quantity needed (including future order projections)
- Sleeve length and sizing requirements
- Any specific material preferences or restrictions
- Customization requirements (color, branding, special features)
- Delivery location and timeline
- Certification or testing documentation needs
- Any special packaging requirements
Q: How can I verify that the sleeves I receive match the cut resistance level claimed?
A: Consider these verification approaches:
- Request test certificates from accredited laboratories
- Conduct third-party testing through independent labs
- Use in-house testing equipment if available
- Check for proper labeling of ratings on the product
- Verify certification marks are properly displayed
Regulatory and Safety Questions
Q: Are there specific industries that require cut resistant sleeves by regulation?
A: Several industries have regulations or strong recommendations regarding cut protection:
- Food processing (particularly meat and poultry)
- Glass manufacturing and handling
- Metal fabrication and stamping
- Automotive manufacturing
- Pulp and paper production
- Recycling operations
Specific requirements vary by country, region, and industry. Always consult current regulations and conduct appropriate risk assessments.
Q: What liability considerations should companies be aware of when selecting cut resistant sleeves?
A: Important liability considerations include:
- Ensuring sleeves meet all relevant safety standards for your industry
- Providing appropriate protection levels based on hazard assessments
- Maintaining documentation of safety training for proper use
- Keeping records of product specifications and certifications
- Implementing regular inspection procedures for worn or damaged sleeves
- Having clear policies for replacement of damaged or worn protection equipment
Always consult with safety professionals and legal advisors to ensure compliance with regulations and appropriate risk management.
Latest Innovations in Work Gloves Manufacturing for Industrial Use
The cut resistant sleeves industry is continuously evolving, with manufacturers investing heavily in research and development to create more effective, comfortable, and specialized protective gear. These innovations are transforming workplace safety while addressing longstanding challenges in industrial environments.
Advanced Material Science Breakthroughs
Material science advancements have revolutionized cut resistant sleeve performance:
Nano-Fiber Technology
- Incorporates microscopic fibers that create extremely dense protective layers
- Achieves higher cut resistance with significantly less material weight
- Improves flexibility and reduces hand fatigue
- Enhances breathability while maintaining protection
- Allows for thinner profiles with equal or superior protection
Graphene-Enhanced Composites
- Integrates graphene into traditional fiber blends
- Provides exceptional strength-to-weight ratio
- Offers improved cut and puncture resistance
- Adds antimicrobial properties to reduce odor
- Enhances durability and extends service life
Bio-Based Sustainable Materials
- Utilizes renewable resources like bamboo and eucalyptus fibers
- Reduces environmental impact while maintaining protection
- Offers natural antimicrobial properties
- Provides enhanced moisture management
- Addresses growing demand for sustainable safety equipment
Qingdao Snell Protective Products has been at the forefront of implementing these material innovations, particularly in their high-performance cut resistant sleeve lines. Their research team continuously evaluates and incorporates advanced materials to enhance both protection and comfort for workers across various industries.
Ergonomic Design Innovations
Manufacturers are increasingly focusing on the human factors of protective equipment:
Anatomical Mapping Technology
- Uses 3D modeling to create sleeves that match natural arm contours
- Reduces bunching and pressure points during movement
- Minimizes fatigue during extended wear
- Maintains protection throughout full range of motion
- Improves worker compliance through enhanced comfort
Zone-Specific Protection Engineering
- Varies protection levels across different areas of the arm
- Concentrates cut resistance at high-risk areas
- Enhances flexibility at joint areas
- Optimizes material use for cost-effectiveness
- Customizes protection based on industry-specific hazards
Dynamic Fit Systems
- Incorporates targeted elasticity for secure positioning
- Prevents sleeve migration during work activities
- Eliminates the need for frequent adjustment
- Reduces irritation from movement
- Accommodates different arm sizes while maintaining protection
Smart Technology Integration
The integration of electronics and digital technologies is creating new possibilities:
Embedded Sensors for Hazard Detection
- Incorporates microsensors that detect proximity to dangerous equipment
- Provides haptic feedback when entering high-risk areas
- Monitors environmental conditions (temperature, chemical exposure)
- Tracks impact and cut events for safety analysis
- Enables real-time safety monitoring and feedback
Connected Safety Ecosystems
- Links protective equipment to workplace safety systems
- Enables automatic machine shutdown when protection is compromised
- Facilitates location tracking in emergency situations
- Allows safety managers to monitor PPE compliance
- Integrates with broader workplace safety analytics
Performance Monitoring Technology
- Tracks protection degradation over time
- Alerts workers when replacement is needed
- Logs exposure to hazardous conditions
- Documents compliance with safety protocols
- Provides data for continuous improvement
Manufacturing Process Innovations
Advanced production technologies are transforming how cut resistant sleeves are made:
Automated Precision Knitting
- Utilizes computer-controlled knitting machines for consistent protection
- Eliminates variations between production runs
- Creates seamless constructions that reduce irritation
- Enables complex material combinations previously impossible
- Increases production efficiency while improving quality
Digital Quality Control Systems
- Implements computer vision for 100% inspection
- Detects subtle defects invisible to human inspectors
- Ensures consistent cut resistance across entire production
- Documents quality metrics for continuous improvement
- Reduces quality variations between manufacturing facilities
Customization Technologies
- Offers rapid prototyping capabilities for specific workplace needs
- Enables cost-effective small-batch production
- Provides digital design tools for customer collaboration
- Facilitates quick adaptation to new workplace hazards
- Allows for personalized fit and protection levels
Industry-Specific Innovation Focus
Manufacturers are developing specialized solutions for different sectors:
Food Processing Advancements
- Metal-detectable fibers for food safety compliance
- Enhanced grip patterns for handling slippery products
- Antimicrobial treatments to prevent contamination
- Easy sanitization features for hygiene requirements
- Color-coding systems for HACCP compliance
Heavy Manufacturing Solutions
- Impact-resistant reinforcements combined with cut protection
- Heat-resistant panels for proximity to thermal processes
- Extended coverage options for comprehensive protection
- Integration with other PPE systems (gloves, aprons)
- Reinforced zones for high-wear areas
Fine Assembly Applications
- Ultra-thin profiles for precision work
- Enhanced tactile sensitivity while maintaining protection
- Static-dissipative properties for electronics assembly
- Fingertip-free designs for detailed manipulation
- Integration with clean room protocols
Environmental Sustainability Initiatives
Progressive manufacturers are prioritizing ecological responsibility:
Circular Economy Approaches
- Developing recyclable and biodegradable materials
- Implementing take-back programs for end-of-life products
- Reducing production waste through optimized cutting
- Using water-based dyes and treatments to reduce chemical impact
- Designing for disassembly and material recovery
Energy-Efficient Manufacturing
- Investing in solar and renewable energy for production facilities
- Implementing heat recovery systems in yarn production
- Utilizing low-energy knitting and forming equipment
- Optimizing supply chains to reduce transportation emissions
- Developing low-temperature washing processes for maintenance
These innovations collectively represent a fundamental shift in how protective equipment is conceptualized and manufactured. As companies like Qingdao Snell continue to invest in research and development, we can expect even more significant advancements in the performance, comfort, and sustainability of cut resistant sleeves in the coming years.
Comparison of Cut Resistant Sleeve Manufacturers in Different Countries
The global market for cut resistant sleeves features manufacturers from diverse regions, each with distinct advantages and specializations. Understanding these differences helps businesses make informed sourcing decisions based on their specific requirements and priorities.
Manufacturing Capabilities Comparison
This detailed comparison examines key operational aspects across major manufacturing regions:
Manufacturing Aspect | Chinese Manufacturers | US Manufacturers | European Manufacturers | Southeast Asian Manufacturers |
---|---|---|---|---|
Production Volume Capacity | Very high; capable of fulfilling large orders (100,000+ units) | Moderate; typically optimized for medium runs | Moderate; focus on specialized production | Growing; variable depending on facility age |
Customization Flexibility | High; willing to accommodate various requirements | Moderate; standardized options with some customization | High; specializes in bespoke solutions | Moderate; improving with technology adoption |
Technology Integration | Rapidly advancing; major investments in automation | Advanced; emphasis on proprietary technologies | Very advanced; leader in technical innovations | Developing; focusing on basic automation first |
Quality Control Systems | Improving significantly; ISO certification common | Comprehensive; rigorous testing protocols | Extremely thorough; multiple testing stages | Variable; facility-dependent with improving standards |
R&D Investment | Growing; focused on manufacturing efficiency | Substantial; emphasis on material science | Extensive; focuses on ergonomics and performance | Limited but increasing in technical capabilities |
Typical Lead Times | 20-40 days for standard orders; 30-60 for custom | 7-21 days for standard; 30-45 for custom | 14-30 days for standard; 30-60 for custom | 30-60 days standard; 45-90 for custom |
Minimum Order Quantities | Wide range (1,000-20,000) based on customization | Higher for custom (500-1,000); lower for standard | Lower thresholds for specialized items | Often higher (5,000+) for basic products |
Cost Structure Analysis
Understanding cost factors helps explain pricing differences between regions:
Cost Component | Chinese Manufacturers | US Manufacturers | European Manufacturers | Southeast Asian Manufacturers |
---|---|---|---|---|
Labor Costs | Moderate and rising (~15-20% of product cost) | High (~35-45% of product cost) | Very high (~40-50% of product cost) | Low to moderate (~10-15% of product cost) |
Raw Material Costs | Competitive due to supply chain integration | Higher due to import duties on some materials | Higher with emphasis on premium materials | Variable depending on import requirements |
Overhead Costs | Lower but increasing with modernization | High due to regulatory compliance | Very high due to extensive regulations | Lower but variable by country |
Energy Costs | Moderate and stabilizing | Moderate with regional variations | High with focus on renewable sources | Low to moderate depending on country |
Shipping Costs to North America | Moderate with longer transit times | Very low for domestic shipments | High with moderate transit times | High with longer transit times |
Shipping Costs to Europe | Moderate with medium transit times | High with medium transit times | Very low for local shipments | Moderate with long transit times |
Total Cost Impact | Most cost-competitive for volume production | Premium pricing focused on domestic market | Highest pricing with emphasis on quality | Emerging value option for basic products |
Quality and Compliance Comparison
Regulatory standards and quality assurance capabilities vary significantly:
Quality Aspect | Chinese Manufacturers | US Manufacturers | European Manufacturers | Southeast Asian Manufacturers |
---|---|---|---|---|
Regulatory Compliance | Improving rapidly; major facilities meet international standards | Comprehensive compliance with domestic and international standards | Extensive compliance with stringent EU regulations | Variable; improving with export-focused facilities |
Quality Consistency | Improving; larger manufacturers like Qingdao Snell maintain high standards | Very consistent with mature quality systems | Extremely consistent with multiple verification stages | Variable between facilities and countries |
Material Traceability | Developing; improving with export requirements | Comprehensive documentation throughout process | Extensive with full supply chain visibility | Limited but developing in export-oriented facilities |
Testing Frequency | Periodic based on production volumes | Regular throughout production process | Continuous with statistical process control | Typically end-of-run verification |
Certification Capabilities | Increasing; major manufacturers hold multiple certifications | Comprehensive domestic and international certifications | Extensive certification with specialized standards | Growing capability among larger manufacturers |
Quality Documentation | Standardized for export requirements | Comprehensive with detailed reporting | Extensive with multi-stage verification | Improving to meet international requirements |
Specialization and Industry Focus
Manufacturers in different regions have developed distinct specializations:
Industry Application | Top Manufacturing Region | Notable Strengths | Typical Material Innovations |
---|---|---|---|
Food Processing | China/US (specialized facilities) | Food-safe materials, metal detectability, antimicrobial treatments | Specialized FDA-compliant coatings, detectable fiber blends |
Automotive Manufacturing | China/Germany | Comprehensive protection packages, oil-resistant formulations | Composite materials with multiple hazard protection |
Metal Fabrication | US/Germany | Highest cut resistance levels, integrated impact protection | Advanced engineered yarns with multiple reinforcement types |
Electronics Assembly | Japan/China | Anti-static properties, fingertip sensitivity, clean room compatibility | Ultra-fine engineered fibers with ESD protection |
Glass Handling | China/Italy | Balanced cut and heat resistance, extended coverage options | Specialized thermal-resistant composite materials |
Construction | US/China | Durability in harsh conditions, multi-hazard protection | Weather-resistant treatments, reinforced wear zones |
Sustainability and Ethical Manufacturing
Environmental and ethical considerations are increasingly important in sourcing decisions:
Sustainability Aspect | Chinese Manufacturers | US Manufacturers | European Manufacturers | Southeast Asian Manufacturers |
---|---|---|---|---|
Renewable Energy Adoption | Growing; government incentives driving implementation | Moderate with regional variations | Advanced; often exceeding regulatory requirements | Limited but developing in newer facilities |
Waste Reduction Initiatives | Improving with modernization; varied implementation | Established programs with measured targets | Comprehensive programs with circular economy focus | Developing with export market pressure |
Water Conservation | Developing with regulatory pressure | Established but varied by region | Advanced with strict regulatory frameworks | Variable depending on local regulations |
Chemical Management | Improving to meet export requirements | Comprehensive with regulatory compliance | Extensive with precautionary approaches | Variable with improving export standards |
Worker Welfare Programs | Developing; significant variations between facilities | Comprehensive with regulatory compliance | Extensive with additional voluntary standards | Developing with international pressure |
Transparency in Reporting | Limited but improving for export-focused companies | Moderate with some public disclosure | Extensive public reporting and verification | Limited with exceptions for multinational operations |
Qingdao Snell Protective Products exemplifies the strengths of modern Chinese manufacturing with their comprehensive quality management systems, advanced production facilities, and strong focus on international certifications. Their CE and ISO 9001 certifications demonstrate a commitment to meeting global standards while maintaining the cost advantages of Chinese manufacturing.
This comparative analysis highlights that each manufacturing region offers distinct advantages. The optimal sourcing strategy often involves balancing these factors based on specific business priorities, whether they be cost efficiency, quality assurance, specialized protection features, or sustainability concerns.
Compliance and Certifications Required for Cut Resistant Sleeves in Different Markets
Navigating the complex landscape of safety standards and certifications is crucial for businesses sourcing cut resistant sleeves globally. Each major market has specific regulatory requirements that impact product selection, importing processes, and legal compliance.
Global Certification Framework
Cut resistant sleeves are subject to various standards and testing methodologies worldwide:
Cut Resistance Testing Standards
- ANSI/ISEA 105 (North America): Uses ASTM F2992-15 test method with TDM-100 machine
- EN 388 (Europe): Employs both Coup Test and ISO 13997 TDM test methods
- ISO 13997 (International): Measures force required to cut through material at 20mm of blade travel
- JIS T8116 (Japan): Japanese Industrial Standard with specific methodologies
- AS/NZS 2161.3 (Australia/New Zealand): Adopts EN 388 methodology with regional variations
Performance Rating Systems
- ANSI/ISEA 105: A1-A9 scale (higher numbers indicate greater protection)
- EN 388:2016: Cut resistance reported on a scale of A-F (alongside abrasion, tear, and puncture ratings)
- EN 388:2003: Older European standard using 1-5 scale for cut resistance
Market-Specific Requirements
Different geographic markets maintain distinct regulatory frameworks:
North American Market Requirements
United States
- OSHA Compliance: While OSHA doesn’t specify cut resistance levels, it requires appropriate PPE based on hazard assessments (29 CFR 1910.132)
- ANSI/ISEA 105-2016: The primary standard for cut resistance classification
- FDA Compliance: Required for food processing applications
- Documentation Requirements:
- Product specification sheets with ANSI ratings
- Test certificates from accredited laboratories
- Technical data files
- Country of origin labeling
Canada
- CSA Z96.1: Canadian Standards Association requirements
- Health Canada Regulations: For food processing applications
- Provincial Workplace Safety Regulations: Vary by province but typically reference ANSI/ISEA standards
European Union Requirements
CE Marking
- Mandatory for all PPE sold in European markets
- Requires conformity with the PPE Regulation (EU) 2016/425
- Products categorized by risk level (Category I, II, or III)
- Cut resistant sleeves typically fall under Category II (intermediate risk)
Certification Process
- EU Type-Examination: Conducted by Notified Body
- Technical Documentation: Comprehensive file including:
- Detailed product descriptions and materials
- EN 388 test reports from accredited labs
- Risk assessment documentation
- User instructions in all relevant languages
- Declaration of Conformity
REACH Compliance
- Registration, Evaluation, Authorization and Restriction of Chemicals
- Limits harmful substances in products sold in EU
- Requires documentation of chemical composition
Asia-Pacific Requirements
Australia/New Zealand
- AS/NZS 2161.3: Harmonized standard for protective gloves
- Work Health and Safety Regulations: Require appropriate risk assessment and PPE selection
Japan
- JIS T8116: Japanese Industrial Standard for protective gloves
- MHLW Approval: Ministry of Health, Labour and Welfare certification
China
- GB/T 23462: National standard for mechanical protective gloves
- CCC Mark: Required for certain protective equipment categories
Industry-Specific Certifications
Beyond geographical requirements, certain industries have additional standards:
Food Processing
- FDA Compliance: Materials must be food-safe
- HACCP Compatibility: Supports hazard analysis critical control points
- Metal Detectability: Often required in food manufacturing
- EU Food Contact Materials Regulation: Compliance with EC 1935/2004
Oil and Gas Industry
- NFPA 2112: For flame-resistant properties
- API Requirements: American Petroleum Institute standards
- ATEX Certification: For potentially explosive atmospheres (EU)
Electrical Work
- ASTM D120: Dielectric testing for electrical workers
- IEC 61482-1-2: Protection against thermal hazards of electric arc
Documentation and Labeling Requirements
Proper documentation and labeling are essential for compliance:
Required Product Markings
- Manufacturer identification
- Model or product code
- Size information
- Applicable performance standards and ratings
- Care instructions
- Date of manufacture or lot number
- CE marking (for European market)
Supporting Documentation
- Technical data sheets
- Material safety data sheets (MSDS)
- Test certificates from accredited laboratories
- User instructions in appropriate languages
- Declaration of Conformity (for EU market)
- Certificate of Origin for customs purposes
Navigating Compliance Challenges
Working with experienced manufacturers can simplify compliance challenges:
Compliance Strategies
- Partner with manufacturers experienced in your target markets
- Request pre-compliance testing before full certification
- Consider third-party compliance consultants for complex markets
- Develop standardized compliance documentation packages
- Implement regular compliance audits and updates
Qingdao Snell Protective Products has established comprehensive certification processes for major global markets. Their cut resistant sleeves are manufactured to meet CE requirements for European markets and ANSI/ISEA standards for North American distribution. Their quality management system is ISO 9001 certified, ensuring consistent compliance with regulatory requirements across all production runs.
Emerging Compliance Trends
Several trends are shaping future compliance requirements:
Sustainability Documentation
- Carbon footprint reporting
- Recycled content verification
- End-of-life disposal instructions
- Chemical reduction certifications
Digital Compliance Tools
- Blockchain verification of certification authenticity
- QR codes linking to current compliance documentation
- Online verification databases for regulatory checking
- Real-time compliance updates for changing regulations
Harmonization Efforts
- Increasing alignment between international standards
- Mutual recognition agreements between testing bodies
- Simplified testing requirements through standardization
- Global product identification systems
Navigating this complex regulatory landscape requires dedicated attention to compliance details. Working with manufacturers who maintain robust certification programs helps ensure that cut resistant sleeves meet all applicable requirements for legal sale and use in target markets.
How to Negotiate Pricing with a Cut Resistant Sleeves Factory
Effective negotiation with cut resistant sleeve manufacturers requires a strategic approach that balances cost considerations with quality, performance, and relationship building. Understanding the factors that influence pricing and employing proven negotiation tactics can result in significant cost savings without compromising worker safety.
Understanding the Cost Structure
Before entering negotiations, gain a thorough understanding of what drives pricing:
Material Cost Factors
- Raw material types and grades (HPPE, aramid, steel, fiberglass)
- Material market fluctuations and commodity pricing
- Blending ratios of performance fibers
- Special treatments or coatings (antimicrobial, moisture-wicking)
- Material wastage in production
Production Cost Elements
- Labor rates in the manufacturing region
- Production efficiency and automation level
- Energy costs for manufacturing processes
- Setup and changeover costs for different production runs
- Quality control and testing expenses
Overhead and Operating Costs
- Facility costs and depreciation
- Regulatory compliance expenses
- Research and development allocation
- Management and administration
- Profit margin requirements
Additional Cost Considerations
- Packaging specifications and materials
- Shipping and logistics arrangements
- Import duties and tariffs
- Currency exchange fluctuations
- Certification and testing costs
Preparation Strategies for Effective Negotiation
Thorough preparation significantly improves negotiation outcomes:
Market Research and Benchmarking
- Obtain quotes from multiple suppliers for comparable products
- Research current market prices for similar cut resistant sleeves
- Understand regional pricing variations and advantages
- Identify standard industry discounts for volume purchases
- Recognize seasonal factors that might affect pricing
Requirement Specification Optimization
- Review technical specifications for cost-saving opportunities
- Consider whether performance requirements could be met with alternative materials
- Evaluate whether all features are necessary or if some could be optional
- Determine if standardization across product lines could increase volume
- Assess whether your specifications are unnecessarily restrictive
Volume Planning and Forecasting
- Calculate annual usage requirements accurately
- Consider consolidating orders for greater volume leverage
- Develop reliable forecasts to share with manufacturers
- Evaluate inventory carrying costs versus volume discount benefits
- Identify opportunities for scheduled delivery programs
Total Cost of Ownership Analysis
- Calculate the lifespan of different cut resistant sleeve options
- Determine replacement frequency based on wear patterns
- Consider laundry and maintenance costs over product lifecycle
- Evaluate productivity impacts of different sleeve designs
- Assess administrative costs associated with different suppliers
Effective Negotiation Tactics and Approaches
Apply these proven negotiation strategies when discussing pricing:
Volume Commitment Strategies
- Offer guaranteed minimum purchase volumes for price concessions
- Propose blanket purchase orders with scheduled releases
- Consider multi-year agreements with volume guarantees
- Discuss volume-based rebate programs as alternatives to upfront discounts
- Explore shared risk arrangements for inventory management
Specification Flexibility
- Offer flexibility on non-critical features in exchange for price concessions
- Discuss material alternatives that might offer cost advantages
- Consider slight modifications to standard products rather than full customization
- Propose simplified packaging for cost reduction
- Evaluate whether longer lead times might enable better pricing
Relationship-Building Approaches
- Emphasize potential for long-term partnership and growth
- Discuss opportunity to become a reference customer
- Offer to participate in product testing or development
- Consider exclusivity arrangements in exchange for preferential pricing
- Propose joint marketing or case study opportunities
Payment and Terms Negotiations
- Offer accelerated payment terms for price reductions
- Discuss currency options that might benefit both parties
- Consider advance deposits to secure preferred pricing
- Negotiate favorable freight terms and responsibilities
- Discuss warranty and return policies that balance risk appropriately
Special Considerations for International Negotiations
When negotiating with overseas manufacturers, consider these additional factors:
Cultural Awareness
- Research negotiation customs and expectations in the manufacturer’s culture
- Understand appropriate pace and relationship-building requirements
- Recognize that direct negotiation styles may not be effective in all cultures
- Be aware of face-saving considerations in some Asian business contexts
- Invest time in relationship development before hard negotiations
Communication Strategies
- Use clear, simple language free of idioms or colloquialisms
- Confirm understanding with written summaries after discussions
- Consider using local representatives who understand cultural nuances
- Allow extra time for translation and clarification
- Establish regular communication protocols that accommodate time zones
International Payment Considerations
- Understand currency exchange risks and hedging options
- Evaluate international payment methods (letter of credit, wire transfer)
- Consider escrow services for initial transactions
- Discuss who bears currency fluctuation risks
- Understand tax implications of international purchasing
Sample Negotiation Scenario Framework
This structured approach provides a template for negotiation preparation:
- Initial Assessment
- Current price per unit: $XX.XX
- Target price reduction: XX%
- Annual purchase volume: XX,XXX units
- Primary negotiation leverage: [volume, long-term commitment, simplified specifications]
- Opening Position Development
- Request for initial price reduction based on market research
- Offer of increased volume commitment in exchange for tiered pricing
- Proposal for specification adjustments to reduce costs
- Discussion of payment terms flexibility
- Compromise Positions
- Fallback volume commitments with modified discount expectations
- Alternative specification modifications
- Secondary term adjustments (delivery schedule, packaging)
- Payment term flexibility options
- Agreement Framework
- Pricing structure with volume tiers
- Specification finalization
- Delivery and logistics arrangements
- Quality assurance requirements
- Performance review mechanisms
Working with established manufacturers like Qingdao Snell Protective Products often provides negotiation advantages. Their factory-direct model eliminates middleman markups, and their efficient production capabilities enable competitive pricing while maintaining high quality standards. Their flexibility in MOQ requirements (3,000-20,000 units) also allows for tailored ordering arrangements that can benefit both small and large volume purchasers.
By approaching negotiations with thorough preparation, cultural sensitivity, and a focus on mutual benefit, businesses can secure advantageous pricing for cut resistant sleeves while building valuable long-term supplier relationships.
Conclusion: Finding Your Ideal OEM Work Gloves Factory Partner
Selecting the right cut resistant sleeves exporter represents a critical business decision that impacts worker safety, operational efficiency, and financial performance. As we’ve explored throughout this comprehensive guide, multiple factors must be carefully weighed to find the optimal manufacturing partner for your specific needs.
Key Considerations for Final Selection
When making your final decision on an OEM work gloves factory, prioritize these essential factors:
Quality and Protection Assurance
The primary function of cut resistant sleeves is protecting workers from injury. Never compromise on protection levels that match your specific hazard assessment. Look for manufacturers with robust quality management systems, comprehensive testing protocols, and appropriate certifications for your market. Consistent quality across production runs is particularly critical for safety equipment.
Total Value Assessment
While initial purchase price is important, the true value of cut resistant sleeves encompasses durability, performance, worker acceptance, and administrative costs. Calculate the total cost of ownership over the product lifecycle, considering replacement frequency, productivity impacts, and potential injury costs. The lowest priced option rarely delivers the best overall value.
Partnership Potential
The most successful supplier relationships evolve into true partnerships characterized by open communication, mutual problem-solving, and collaborative improvement. Evaluate potential manufacturers for their willingness to invest in understanding your business needs, responsiveness to concerns, and ability to grow with your changing requirements. A partner invested in your success will deliver value beyond the transaction.
Supply Chain Reliability
In today’s volatile global environment, supply chain resilience is more critical than ever. Assess manufacturers for production capacity, material sourcing stability, contingency planning, and logistical capabilities. Consider geographical diversification of suppliers to mitigate regional disruption risks. Reliable access to safety equipment is non-negotiable for maintaining operations.
Innovative Capability
The protective equipment industry continues to evolve rapidly, with new materials, technologies, and designs constantly emerging. Select manufacturing partners with demonstrated commitment to research and development, willingness to embrace new technologies, and ability to adapt to changing safety requirements. Forward-thinking suppliers help keep your safety program at the cutting edge.
Building Successful Long-Term Relationships
Once you’ve selected a manufacturing partner, focus on these strategies for relationship development:
Structured Communication
- Establish regular review meetings and performance assessments
- Create clear escalation paths for issue resolution
- Share forecasts and business plans to enable better planning
- Provide constructive feedback on product performance
- Maintain open dialogue about changing requirements
Collaborative Improvement
- Work together on product enhancements based on field experience
- Share worker feedback to drive comfort and acceptance improvements
- Explore joint cost-reduction initiatives that benefit both parties
- Pursue continuous improvement in quality and consistency
- Engage in collaborative problem-solving for emerging challenges
Strategic Alignment
- Ensure mutual understanding of long-term objectives
- Align on quality expectations and performance metrics
- Create shared success definitions and recognition
- Develop mutual growth and development plans
- Build executive-level relationships to support partnership
The Qingdao Snell Advantage
Among the many OEM work gloves factories available globally, Qingdao Snell Protective Products Co., Ltd. stands out as an exemplary manufacturing partner for cut resistant sleeves. With over a decade of specialized expertise in protective equipment manufacturing, Snell combines advanced production capabilities with rigorous quality management systems certified to ISO 9001 and CE standards.
Their comprehensive product range includes cut resistant sleeves engineered for various industries and hazard levels, with customization capabilities to meet specific workplace requirements. Snell’s factory-direct business model eliminates middleman markups while providing personalized service and technical expertise. Their flexible MOQ requirements (3,000-20,000 units) accommodate both growing businesses and established operations with higher volume needs.
Final Recommendations
As you proceed with selecting your cut resistant sleeves supplier, consider these final recommendations:
- Test Before Committing: Always request and thoroughly evaluate samples before placing large orders
- Start Conservatively: Begin with smaller orders to assess quality consistency and relationship dynamics
- Document Everything: Maintain detailed specifications, quality requirements, and performance expectations
- Visit When Possible: Nothing replaces the insights gained from in-person facility visits
- Build Relationships at Multiple Levels: Develop connections with sales, technical, quality, and management contacts
- Stay Informed: Keep current on material innovations and safety standard developments
- Regularly Reassess: Periodically evaluate whether your supplier relationships continue to meet your evolving needs
By applying the knowledge and strategies outlined in this guide, you can confidently select an OEM work gloves factory that will provide high-quality cut resistant sleeves to protect your workforce while delivering exceptional value to your business.
Frequently Asked Questions About OEM Work Gloves Factory
General Questions About Work Glove Manufacturing
Q: What is an OEM work gloves factory?
A: An Original Equipment Manufacturer (OEM) work gloves factory produces protective gloves and sleeves according to client specifications, often allowing for customization of design, materials, features, and branding. These factories typically handle the entire production process from material sourcing to final packaging and can produce items under the client’s brand name rather than their own.
Q: How long does it typically take to manufacture a custom order of cut resistant sleeves?
A: Production timelines vary based on order volume, customization requirements, and the manufacturer’s current capacity. Typical production times range from 20-45 days after design approval and sample confirmation. Larger orders or highly customized products may require additional time. Shipping adds another 5-30 days depending on the transportation method and destination.
Q: Can manufacturers produce small test orders before committing to large quantities?
A: Many manufacturers offer sample programs or small test orders, though these typically come at a premium price compared to regular production runs. Established manufacturers like Qingdao Snell often provide prototype or sample services to verify design, fit, and performance before full production. These samples allow clients to test products in their actual work environments before committing to larger quantities.
Technical and Material Questions
Q: What are the most common materials used in manufacturing cut resistant sleeves?
A: The most commonly used materials include:
- High-Performance Polyethylene (HPPE)
- Aramid fibers (including Kevlar®)
- UHMWPE (Ultra-High-Molecular-Weight Polyethylene)
- Glass fiber and steel fiber blends
- Nylon and polyester as base materials
- Spandex or elastane for flexibility and fit
These materials are often blended in proprietary combinations to achieve specific performance characteristics.
Q: How do manufacturers test cut resistance levels?
A: Manufacturers use standardized testing methods specified by regulations:
- ANSI/ISEA 105: Uses the ASTM F2992-15 test method with a TDM-100 machine that measures the force required to cut through material
- EN 388: Employs both the Coup Test (rotating circular blade) and ISO 13997 TDM test
Testing is performed either in-house with certified equipment or through independent, accredited testing laboratories. Results determine the official cut resistance rating assigned to the product.
Q: Can cut resistant sleeves be made in custom colors to match company branding?
A: Yes, most manufacturers offer color customization options, though minimum order quantities are typically higher for custom colors. Standard colors (white, gray, black, blue) are usually available with lower MOQs, while custom colors may require larger orders to justify the dyeing process setup. Some high-visibility colors may also affect pricing due to specialized dye costs.
Business and Ordering Questions
Q: What information should be provided when requesting a quote for custom cut resistant sleeves?
A: To receive accurate quotes, provide:
- Required protection level (cut resistance rating)
- Sleeve length and sizing requirements
- Material preferences or specific performance requirements
- Anticipated order quantity and frequency
- Customization needs (colors, logos, special features)
- Target markets and required certifications
- Delivery location and preferred shipping method
- Timeline requirements
The more detailed your specifications, the more accurate the quote will be.
Q: How do payment terms typically work with international manufacturers?
A: Common payment structures include:
- 30% deposit upon order confirmation, 70% before shipment
- Letter of Credit (L/C) for larger orders with established companies
- Full prepayment for initial orders or smaller quantities
- T/T (wire transfer) is the most common payment method
Established relationships may lead to more favorable terms such as net 30 or 60 payment options for repeat customers.
Q: What are typical warranty or guarantee policies for cut resistant sleeves?
A: Most quality manufacturers offer warranties covering:
- Manufacturing defects
- Material quality issues
- Compliance with agreed specifications
These warranties typically do not cover normal wear and tear, improper use, or damage from improper cleaning. The standard warranty period ranges from 30 days to 6 months depending on the manufacturer and product type.
Customization and Branding Questions
Q: What are the minimum quantities for adding custom logos to cut resistant sleeves?
A: Minimum quantities for custom branding typically range from:
- 500-1,000 pieces for basic screen printing
- 1,000-3,000 pieces for heat transfer applications
- 3,000-5,000 pieces for embroidered logos
- 5,000+ pieces for woven-in branding
Qingdao Snell requires minimum orders between 3,000-20,000 units for custom branded items, with specific minimums depending on the customization complexity and production requirements.
Q: Besides logos, what other customization options are available?
A: Common customization options include:
- Custom length and sizing
- Special cuff designs (elastic, velcro, extended coverage)
- Thumb holes or hand coverage options
- Color-coding for size or department identification
- High-visibility stripes or reflective elements
- Packaging customization (individual packets, bulk boxes, retail display)
- Hangtags and product information inserts
- QR codes linking to training or safety information
Q: How durable are logos and branding on cut resistant sleeves?
A: Durability varies by application method:
- Screen printing: Generally lasts 30-50 industrial wash cycles
- Heat transfer: Typically maintains quality for 40-60 wash cycles
- Embroidery: Extremely durable, often outlasting the sleeve itself
- Woven-in branding: Permanent part of the fabric structure
Manufacturers should provide care instructions specific to the branding method used to maximize longevity.
Compliance and Quality Questions
Q: How can I verify that a manufacturer’s quality certifications are legitimate?
A: Verify certifications through these methods:
- Request certification documents with issuing body information
- Confirm certification status through the issuing organization’s website
- Look for certification numbers and expiration dates
- Ask for recent test reports from accredited laboratories
- Consider third-party inspection services for initial orders
- Request references from existing clients in similar industries
Q: What quality control measures should a reputable manufacturer have in place?
A: Look for manufacturers with:
- ISO 9001 certified quality management systems
- Written quality control procedures for each production phase
- Incoming material inspection protocols
- In-process quality checks with documented acceptance criteria
- Final product testing for performance verification
- Statistical process control methods
- Traceability systems for materials and production lots
- Retention samples from production runs
Q: How do manufacturers ensure consistency across multiple production runs?
A: Quality manufacturers maintain consistency through:
- Detailed product specifications and manufacturing standards
- Material sourcing from consistent suppliers
- Regular calibration of production equipment
- Standardized operator training programs
- Statistical monitoring of quality metrics
- Retention of production records and samples
- Comparison testing between production runs
- Regular auditing of production processes
These answers address common questions that arise when working with OEM work gloves factories and can help businesses navigate the supplier selection and ordering process more effectively.
Qingdao Snell’s research and development team actively monitors these trends, incorporating promising innovations into their product development pipeline. Their commitment to continuous improvement ensures they stay at the forefront of gardening glove technology while maintaining practical, cost-effective solutions for everyday use.