Ultimate Guide to Cut Resistant Gloves OEM Manufacturing in 2025
April 12, 2025
Share This Article
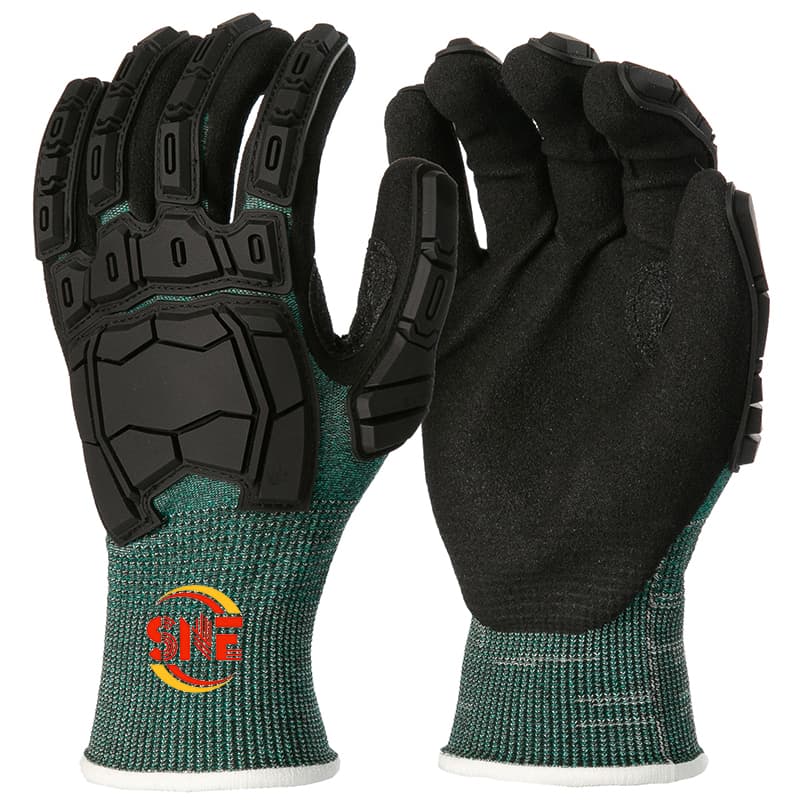
In today’s industrial landscape, worker safety has become a paramount concern for businesses across various sectors. Among the essential personal protective equipment (PPE), cut resistant gloves stand out as critical components that shield workers from potential hand injuries. As we move into 2025, the market for custom-manufactured cut resistant gloves continues to evolve with innovative materials, manufacturing techniques, and design considerations. This comprehensive guide explores everything you need to know about navigating the world of Cut Resistant Gloves OEM (Original Equipment Manufacturing) partnerships.
What Are Cut Resistant Gloves and Why Do You Need an OEM Partner?
Cut resistant gloves are specialized hand protection designed to prevent lacerations and cuts when handling sharp objects or materials. Unlike standard work gloves, these incorporate specialized fibers and materials engineered to resist slicing, cutting, and puncturing forces. The technology behind these protective garments has advanced significantly, with modern gloves offering various levels of cut resistance while maintaining dexterity and comfort.
Working with an OEM manufacturer allows your business to create customized cut resistant gloves tailored to your specific industry requirements. Whether you’re in food processing, automotive manufacturing, glass handling, or construction, partnering with the right OEM factory ensures your workers receive optimal protection with gloves designed specifically for their applications.
The key advantages of partnering with a cut resistant gloves OEM include:
- Customization options – from materials and cut resistance levels to sizing and ergonomic features
- Brand identity integration – incorporating your logo, colors, and packaging requirements
- Quality control according to your specifications
- Cost efficiency through direct manufacturing relationships
- Innovative materials access not available in off-the-shelf options
- Compliance with industry-specific regulatory requirements
As workplace safety standards become increasingly stringent in 2025, having a reliable OEM partner has become essential for companies serious about worker protection and regulatory compliance.
How to Choose the Best Cut Resistant Gloves OEM for Your Business?
Selecting the right manufacturing partner for your cut resistant gloves is a critical decision that impacts product quality, worker safety, and your bottom line. Here are the key factors to consider when evaluating potential OEM partners:
Manufacturing Capabilities and Expertise
Look for manufacturers with specific experience in producing cut resistant gloves rather than general workwear factories. Experienced OEMs understand the technical requirements of different cut resistance levels and can advise on the most appropriate materials and constructions for your application.
Qingdao Snell Protective Products Co., Ltd. stands out with over 10 years of expertise specifically in protective gloves manufacturing. Their specialized production facilities in Gaomi and Nantong feature six dedicated production lines for various types of cut resistant gloves, ensuring they have the technical capacity to meet diverse requirements.
Quality Certification and Standards Compliance
Verify that the manufacturer holds relevant certifications such as:
- ISO 9001 quality management systems
- CE certification for European markets
- ANSI/ISEA 105 compliance for cut resistance testing and classification
- Oeko-Tex Standard 100 for environmentally friendly materials
The best OEMs maintain rigorous testing facilities to ensure consistent compliance with these standards. Their quality control processes should include regular testing of cut resistance levels, material durability, and overall glove performance.
Production Capacity and Minimum Order Quantities
Assess whether the manufacturer can handle your volume requirements, both for initial orders and potential scaling:
- What is their monthly production capacity?
- Can they accommodate seasonal fluctuations in demand?
- What are their minimum order quantities (MOQ)?
- What is their lead time from order to delivery?
For example, Qingdao Snell has a MOQ range of 3,000-20,000 pieces, making them suitable for medium to large-scale operations. Their six production lines provide substantial capacity for meeting varied demand levels.
Communication and Collaboration
Effective communication is critical for successful OEM relationships. Consider:
- Language capabilities of their sales and technical teams
- Responsiveness to inquiries and change requests
- Willingness to provide samples and prototypes
- Transparency regarding production challenges
- Technical support for product development
Cost Structure and Pricing Transparency
While price shouldn’t be the only consideration, understanding the manufacturer’s pricing structure is important:
- Request detailed breakdowns of costs
- Understand how material choices affect pricing
- Inquire about volume discounts
- Clarify payment terms and conditions
- Evaluate the overall value proposition rather than just the per-unit cost
By thoroughly evaluating these factors, you can identify an OEM partner capable of producing cut resistant gloves that meet your quality standards, technical requirements, and business objectives.
What Are the Most Durable Materials for Cut Resistant Gloves?
The effectiveness of cut resistant gloves depends significantly on the materials used in their construction. In 2025, several high-performance materials dominate the market, each offering unique properties and protection levels.
High-Performance Engineered Fibers
HPPE (High-Performance Polyethylene)
HPPE, including brands like Dyneema® and Spectra®, offers exceptional cut resistance with lightweight comfort. These fibers are:
- 15 times stronger than steel on a weight-for-weight basis
- Highly resistant to moisture, chemicals, and UV radiation
- Extremely lightweight and comfortable for extended wear
- Washable and maintain performance after multiple cleaning cycles
HPPE has become increasingly popular in food processing, automotive assembly, and light manufacturing applications where both dexterity and cut protection are priorities.
Para-aramid Fibers
Kevlar® and similar para-aramid fibers provide excellent cut and heat resistance:
- Exceptional strength-to-weight ratio
- Temperature resistance up to 800°F (427°C)
- Good abrasion resistance
- Medium dexterity depending on construction
These materials excel in applications involving heat exposure alongside cut hazards, such as metal stamping, glass handling, and automotive manufacturing.
UHMWPE (Ultra-High-Molecular-Weight Polyethylene)
This advanced polymer offers:
- Superior cut resistance
- Excellent abrasion protection
- High chemical resistance
- Good comfort and flexibility
UHMWPE is ideal for precision work in hazardous environments, particularly in chemical processing and pharmaceutical manufacturing.
Composite Materials and Blends
Modern cut resistant gloves often utilize composite constructions that blend multiple materials:
Steel/Fiberglass Core Wrapping
Combining steel or fiberglass filaments with engineered fibers creates gloves with:
- Enhanced cut resistance at critical areas
- Improved puncture protection
- Targeted reinforcement where needed most
- Different performance zones within the same glove
Nylon/Lycra® Blends
Adding these materials to cut-resistant fibers provides:
- Improved fit and comfort
- Better dexterity and tactile sensitivity
- Enhanced breathability
- Reduced hand fatigue during extended wear
Coating Technologies
The outer coating on cut resistant gloves significantly affects grip, durability, and application suitability:
Polyurethane (PU) Coatings
- Excellent dexterity and tactile sensitivity
- Good dry and light oil grip
- Breathable characteristics
- Moderate abrasion resistance
Nitrile Coatings
- Superior oil and grease resistance
- Excellent puncture resistance
- Good durability in abrasive environments
- Moderate chemical protection
Latex/Rubber Coatings
- Exceptional grip in wet conditions
- Good elasticity and comfort
- Moderate chemical resistance
- Natural comfort and flexibility
When working with an OEM manufacturer, discussing these material options in relation to your specific application requirements is essential. The best manufacturing partners can recommend optimal material combinations based on your industry’s specific hazards, environmental conditions, and user comfort needs.
How to Customize Cut Resistant Gloves with Your Logo and Branding?
Customizing cut resistant gloves with your company’s branding creates a professional appearance, promotes brand recognition, and can help with inventory management. In 2025, OEM manufacturers offer several effective methods for incorporating your branding into cut resistant gloves.
Branding Techniques for Cut Resistant Gloves
Screen Printing
Screen printing remains the most common method for applying logos to the back of gloves or cuffs:
- Ideal for simple designs with limited colors
- Durable for industrial applications
- Cost-effective for large production runs
- Works well on flat surfaces of the glove
For best results, provide your OEM partner with vector file formats (AI, EPS, PDF) of your logo in pantone color codes to ensure accurate color matching.
Heat Transfer
Heat transfer technology allows for more detailed designs and photographic elements:
- Higher resolution than screen printing
- Good for complex, multi-colored logos
- Effective on various substrate materials
- More expensive than screen printing for large runs
Embroidery
For premium cut resistant gloves, embroidered logos on cuffs provide a high-end appearance:
- Exceptional durability through multiple washing cycles
- Three-dimensional quality adds perceived value
- Limited in detail level for small logos
- Generally more expensive than printing methods
Silicone Patches
Flexible silicone logo patches can be applied to gloves for a distinctive branding approach:
- Three-dimensional appearance
- Excellent durability in harsh environments
- Resistant to chemicals and cleaning procedures
- Premium appearance with tactile quality
Strategic Placement Considerations
When customizing cut resistant gloves, consider these strategic placement options:
- Back of Hand – The most visible area during use, ideal for primary branding
- Cuff Area – Excellent for company name, model number, or secondary branding
- Palm Area – Usually reserved for grip pattern branding or subtle logos
- Fingertips – Can incorporate small identifying marks or color coding for size/model identification
Additional Customization Options
Beyond logos, comprehensive branding can include:
- Custom Packaging – Branded boxes, polybags, or hang tags
- Color Customization – Glove liners in company colors
- Cuff Style – Customized lengths, materials, or closures
- Size Indicators – Custom sizing system with your branding guidelines
- Specialized Labels – Including QR codes linking to training videos or specification sheets
Working with Your OEM Partner on Branding
To ensure successful branding implementation:
- Provide clear brand guidelines, including Pantone color codes and minimum size requirements
- Request physical samples before full production to verify appearance and durability
- Discuss durability requirements based on the working environment and cleaning procedures
- Consider the impact of branding on glove performance and comfort
- Evaluate cost implications for different branding options against your budget
How to Ensure Quality Control for Cut Resistant Gloves?
Quality control is a critical aspect of OEM cut resistant glove manufacturing that ensures consistent protection levels, durability, and performance. As workplace safety standards become stricter in 2025, implementing robust quality assurance measures has become increasingly important for both manufacturers and businesses sourcing these protective products.
Comprehensive Testing Protocols
Effective quality control begins with standardized testing procedures that evaluate all critical performance aspects:
Cut Resistance Testing
Cut resistance testing should comply with international standards such as:
- ANSI/ISEA 105-2016 – The American National Standard that classifies cut resistance on a scale from A1 (lowest) to A9 (highest)
- EN 388:2016 – The European standard that measures cut resistance from Level A to Level F
- ISO 13997 – International standard measuring cut resistance in Newtons
Reliable OEM partners maintain in-house testing facilities for regular batch testing rather than relying solely on third-party certification of initial samples.
Abrasion Resistance Testing
Since cut resistant gloves often operate in harsh environments, abrasion testing evaluates durability:
- Taber Abrasion testing measures material wear under controlled conditions
- Results should be compared against minimum performance requirements for specific applications
- Multiple areas of the glove should be tested, particularly high-wear regions
Tear and Puncture Resistance
Complementary to cut resistance, these properties ensure comprehensive protection:
- Tear strength measured in Newtons indicates resistance to ripping
- Puncture resistance tests using standardized probes evaluate protection against sharp objects
- Combined results provide a complete protection profile
Manufacturing Process Controls
Beyond final product testing, quality control extends throughout the manufacturing process:
Raw Material Verification
- Incoming material certification and verification
- Fiber composition testing to ensure correct engineered fiber content
- Material performance batch testing before production
- Storage and handling protocols to prevent material degradation
In-Process Inspection Points
- Yarn and liner production quality checks
- Coating application consistency monitoring
- Stitch quality and seam strength verification
- Dimensional stability checks during production
Final Product Inspection
- Visual inspection for defects (100% inspection for premium products)
- Statistical sampling based on AQL (Acceptable Quality Level) standards
- Functional testing of finished gloves
- Packaging and labeling verification
Documentation and Traceability Systems
Modern quality control extends beyond physical testing to include comprehensive documentation:
- Batch Tracking – Each production batch should be traceable from raw materials through to finished product
- Test Certificates – Documentation of test results for each production run
- Manufacturing Records – Detailed production parameters and quality check results
- Compliance Documentation – Records demonstrating adherence to relevant standards
Third-Party Verification
While in-house testing forms the foundation of quality control, third-party verification adds credibility:
- Independent laboratory testing of production samples
- Certification body audits of manufacturing processes
- Customer feedback integration into quality improvement processes
- Benchmark testing against competitor products
Qingdao Snell implements a rigorous quality management system certified to ISO 9001 standards. Their dedication to quality control includes comprehensive testing facilities for cut resistance, abrasion resistance, and grip performance. Each production batch undergoes multiple inspection points, with both in-process checks and final verification before shipping. This systematic approach ensures consistent performance across all their cut resistant glove products.
Compliance and Certifications Required for Cut Resistant Gloves in Different Markets
Navigating the complex landscape of safety standards and certifications is essential when sourcing cut resistant gloves through OEM manufacturing. Different regions have established specific requirements that manufacturers must meet to legally sell and distribute protective gloves. Understanding these requirements ensures your products will be compliant in your target markets.
North American Standards and Certifications
United States Requirements
In the US market, the primary standards governing cut resistant gloves include:
- ANSI/ISEA 105-2016: This standard classifies cut resistance on a scale from A1 (lowest) to A9 (highest) using the ASTM F2992-15 test method. The test measures the weight needed to cut through material with a standardized blade traveling a fixed distance.
- OSHA Compliance: While OSHA doesn’t certify products directly, employers must provide appropriate PPE meeting relevant standards under 29 CFR 1910.138 for hand protection.
- FDA Regulations: For cut resistant gloves used in food processing, compliance with FDA 21 CFR 177 regarding materials safe for food contact is required.
Canadian Requirements
- CSA Z96.1: The Canadian standards for hand protection, which align substantially with ANSI standards but may have specific additional requirements.
- Health Canada Regulations: Similar to FDA requirements for food processing applications.
European Standards and CE Marking
The European market requires adherence to specific standards under the PPE Regulation (EU) 2016/425:
- EN 388:2016: The primary standard for protective gloves against mechanical risks, which evaluates gloves on four or five criteria:
- Abrasion resistance (0-4)
- Blade cut resistance (0-5)
- Tear resistance (0-4)
- Puncture resistance (0-4)
- ISO cut resistance (A-F) – added in the 2016 revision
- CE Marking: Mandatory for all PPE sold in the European Economic Area. The certification process varies depending on the risk category:
- Category I (simple design/minimal risk): Self-certification
- Category II (intermediate risk): Type examination by a notified body
- Category III (complex design/serious risk): Type examination plus ongoing surveillance
- EU Declaration of Conformity: Documentation that must accompany each glove model, confirming compliance with relevant requirements.
Asia-Pacific Standards
Australia and New Zealand
- AS/NZS 2161.3: Based on EN 388 but with some regional modifications for local conditions.
Japan
- JIS T8116: The Japanese Industrial Standard for protective gloves, with testing methodologies similar to international standards but with some specific requirements.
China
- GB/T 23462: The Chinese national standard for protective gloves against mechanical risks, which has similarities to EN 388.
Industry-Specific Certifications
Beyond geographical certifications, specific industries may require additional standards:
- ASTM F2878: For cut resistance in food service applications
- EN 13034: For gloves providing protection against liquid chemicals
- NFPA 2112: For flame-resistant gloves in certain applications
Documentation Requirements for Global Compliance
To ensure global marketability, OEM manufacturers should provide:
- Technical Files: Comprehensive documentation of design, materials, and test results
- User Instructions: Multi-language instructions for proper use and limitations
- Traceability Information: Lot numbers, production dates, and origin information
- Regular Testing Reports: Updated certification as standards evolve
Emerging Standards and Future Trends for 2025
As we progress through 2025, several trends in certification are emerging:
- Harmonization Efforts: Increased alignment between different regional standards
- Sustainability Certifications: New standards addressing environmental impact and ethical manufacturing
- Digital Compliance Passports: Electronic systems for tracking and verifying certification status
- Enhanced Testing Methods: More sophisticated cut resistance tests that better replicate real-world hazards
Qingdao Snell maintains comprehensive certification for their cut resistant gloves, including CE certification and ISO 9001 quality management systems. Their technical team stays abreast of evolving standards across global markets, ensuring their OEM customers receive products that meet all relevant compliance requirements. Their dedicated compliance department can provide guidance on specific market requirements and prepare the necessary documentation for different regional markets.
How to Find a Reliable Cut Resistant Gloves OEM Factory?
Finding the right manufacturing partner for cut resistant gloves requires a systematic approach to ensure quality, reliability, and value. As the global manufacturing landscape continues to evolve in 2025, businesses have more options than ever, but also face greater challenges in vetting potential suppliers. Here’s a comprehensive strategy for identifying and selecting the ideal OEM factory for your cut resistant gloves.
Research and Initial Screening Methods
Begin your search through multiple channels to develop a comprehensive list of potential manufacturing partners:
Online B2B Platforms
- Alibaba, Global Sources, Made-in-China: These platforms provide access to thousands of manufacturers with filtering capabilities for certification, capacity, and location.
- Industry-Specific Directories: Specialized directories like ThomasNet or EC21 focus on industrial suppliers.
- LinkedIn: Professional networks can provide connections to manufacturer representatives and industry insiders.
Trade Shows and Industry Events
Despite the rise of digital sourcing, trade shows remain valuable for in-person evaluation:
- A+A (Germany): The leading international trade fair for safety, security, and health at work
- National Safety Council Expo (USA): Major safety equipment exhibition in North America
- China International Occupational Safety & Health Exhibition: Largest PPE expo in Asia
These events allow you to examine products firsthand, meet manufacturer representatives, and compare multiple suppliers efficiently.
Industry Associations and Referrals
- International Glove Association (IGA): Organization dedicated to glove manufacturers
- Industrial Fabrics Association International (IFAI): Network of technical textile manufacturers
- Referrals from related industry partners: Often the most reliable source of pre-vetted suppliers
Evaluation Criteria for Cut Resistant Glove Manufacturers
Once you’ve identified potential partners, evaluate them based on these critical factors:
Manufacturing Capabilities and Specialization
- Production Focus: Does the manufacturer specialize in cut resistant gloves, or are they a general textile producer?
- Technical Expertise: Do they have specific knowledge about cut resistance technologies and testing?
- R&D Capabilities: Can they assist with product development and innovation?
- Equipment Profile: Do they have modern machinery specifically designed for engineered fiber processing?
Quality Management Systems
- Certification Status: ISO 9001, ISO 14001, OHSAS 18001/ISO 45001
- Testing Facilities: In-house capabilities for cut resistance, abrasion, and performance testing
- Quality Control Processes: Statistical process control, inspection protocols, defect rates
- Corrective Action Procedures: Systems for addressing quality issues when they arise
Production Capacity and Flexibility
- Minimum Order Quantities (MOQ): Do they align with your volume requirements?
- Production Lead Times: Typical timeframes from order to delivery
- Capacity Utilization: Current production load and ability to accommodate new customers
- Seasonal Flexibility: Ability to adjust production during peak demand periods
Verification and Due Diligence
Before finalizing your selection, conduct thorough verification:
Factory Audits and Site Visits
If possible, arrange a factory visit to assess:
- Production facilities and equipment condition
- Worker skills and training
- Material storage and handling
- Quality control implementation
- General factory organization and cleanliness
If direct visits aren’t feasible, consider third-party audit services that can provide objective assessments.
Sample Evaluation Process
Request multiple rounds of samples to verify capabilities:
- Initial Samples: Assess general quality and capabilities
- Customized Samples: Test ability to meet your specific requirements
- Production Samples: Taken from actual production runs to ensure consistency
Subject samples to independent testing for cut resistance, durability, and performance.
Reference Checks and Background Verification
- Contact current or former clients for feedback on reliability and quality
- Verify business registration and legal standing
- Check financial stability through credit reports when possible
- Research online reputation and customer reviews
Key Recommendations for OEM Selection
Based on extensive industry analysis, consider these recommendations when making your final selection:
- Prioritize Specialized Expertise: Manufacturers focused specifically on cut resistant gloves typically deliver better quality and innovation than general glove factories.
- Value Direct Communication: Select partners who provide direct access to technical staff, not just sales representatives.
- Balance Cost with Quality: The lowest price often results in compromise on materials or construction that affects protection levels.
- Consider Geographic Advantages: Different manufacturing regions offer distinct advantages:
- China: Advanced machinery, established supply chains, comprehensive capabilities
- Vietnam/Indonesia: Emerging manufacturing hubs with competitive labor costs
- Europe/North America: Proximity to Western markets, specialized technology
- Evaluate Long-term Partnership Potential: The best OEM relationships develop over time, so consider future growth compatibility.
Qingdao Snell Protective Products Co., Ltd. exemplifies many of these ideal characteristics as a specialized manufacturer of protective gloves. With their direct factory model eliminating middlemen, they offer a balance of quality, customization capabilities, and value. Their two manufacturing facilities in Gaomi and Nantong provide significant production capacity with six dedicated production lines, while their ten-plus years of manufacturing expertise ensures technical competence in producing high-performance cut resistant gloves.
Minimum Order Quantity (MOQ) Considerations When Ordering Cut Resistant Gloves
Understanding and navigating minimum order quantities (MOQ) is crucial when establishing relationships with cut resistant glove OEM manufacturers. MOQs significantly impact your purchasing strategy, inventory management, and overall cost structure. Here’s a comprehensive analysis of MOQ considerations to help you make informed decisions.
Understanding MOQ Structures in Cut Resistant Glove Manufacturing
MOQs for cut resistant gloves typically vary based on several factors:
Standard MOQ Ranges by Manufacturer Type
Manufacturer Category | Typical MOQ Range | Best Suited For |
---|---|---|
Large-Scale Factories | 10,000-50,000 pairs | National distributors, large retailers |
Mid-Size Manufacturers | 3,000-10,000 pairs | Regional distributors, medium businesses |
Small Specialty Producers | 500-3,000 pairs | Local suppliers, specialized applications |
Direct-to-Consumer Brands | 50-500 pairs | End-users, small businesses |
MOQ Variations by Product Type
Glove Specification | MOQ Impact | Reasoning |
---|---|---|
Standard Models | Lower MOQs | Existing patterns and materials |
Custom Designs | Higher MOQs | Setup costs and material sourcing |
Special Cut Resistance Levels | Higher MOQs | Specialized materials and testing |
Multiple Size Assortments | Higher Total MOQ | Production efficiency considerations |
Color and Branding Impacts on MOQ
Customization Level | MOQ Effect | Notes |
---|---|---|
Standard Colors | Lowest MOQ | Uses existing materials |
Custom Colors | 20-30% Higher MOQ | Yarn/material dyeing requirements |
Simple Logo Printing | Minimal MOQ Impact | Standard printing setup |
Complex Multi-Color Branding | Significant MOQ Increase | Setup costs and production adjustments |
Strategies for Managing MOQ Requirements
For businesses facing challenging MOQ requirements, consider these practical approaches:
Phased Ordering Approaches
- Blanket Orders: Place a large order with scheduled deliveries over time
- Conditional Volume Commitments: Negotiate lower initial MOQs with committed future orders
- Development Partnerships: Work with manufacturers on gradual scaling of volumes as your market develops
MOQ Negotiation Tactics
- Standardization Leverage: Use standard materials and designs with custom branding
- Multi-Product Bundling: Combine different product orders to reach total MOQ requirements
- Premium Pricing Acceptance: Offer higher per-unit pricing for lower initial quantities
- Seasonal Planning: Align larger orders with manufacturer’s slower production periods
- Sample Order Upgrades: Convert extensive sample testing into partial production orders
Inventory Management Strategies
- Forecasting Systems: Implement demand forecasting to better plan order volumes
- Safety Stock Calculations: Determine optimal inventory levels to balance MOQ with carrying costs
- Consortium Buying: Partner with complementary businesses to share large MOQ orders
- Distributor Relationships: Work through distributors who can manage larger volumes
Cost Implications of MOQ Decisions
Understanding the financial impact of MOQ choices helps optimize your purchasing strategy:
Price Breaks and Volume Discounts
Order Volume (% of Standard MOQ) | Typical Price Premium |
---|---|
25% of Standard MOQ | +30-40% per unit |
50% of Standard MOQ | +15-20% per unit |
100% of Standard MOQ | Base price |
200% of Standard MOQ | -5-10% per unit |
500% of Standard MOQ | -10-20% per unit |
Hidden Costs Analysis
When evaluating MOQ requirements, consider these additional cost factors:
- Inventory Carrying Costs: Typically 15-30% of inventory value annually
- Obsolescence Risk: Product updates or specification changes may devalue existing stock
- Cash Flow Impact: Capital tied up in inventory versus other business investments
- Storage Requirements: Physical space and handling costs for larger inventories
- Currency Fluctuation Exposure: Longer inventory periods increase currency risk
Working with Qingdao Snell’s MOQ Requirements
Qingdao Snell Protective Products Co., Ltd. has established MOQ requirements ranging from 3,000 to 20,000 pieces, positioning them as an ideal partner for medium to large distributors, safety equipment companies, and industrial suppliers. Their flexible approach to MOQ management includes:
- Mixed-Model Orders: Combining different models to reach total MOQ thresholds
- Phased Delivery Scheduling: Allowing blanket orders with staggered shipments
- Gradual Customization: Starting with standard models and transitioning to fully customized products as volumes increase
- Sample Development Programs: Comprehensive sampling before full production commitment
For businesses concerned about meeting Qingdao Snell’s standard MOQs, their sales team can work with you to develop appropriate strategies based on your specific market needs and growth projections. Their direct factory model eliminates middlemen markups, often offsetting any premium associated with lower initial volumes.
When contacting Qingdao Snell about your cut resistant glove requirements, be prepared to discuss your annual volume projections, seasonal fluctuations, and growth expectations to develop the most advantageous MOQ arrangement.
Latest Innovations in Cut Resistant Gloves Manufacturing for Industrial Use
The cut resistant gloves industry is undergoing rapid technological advancement in 2025, with innovations improving protection levels, comfort, functionality, and sustainability. Understanding these developments is crucial for businesses seeking cutting-edge OEM manufacturing partners. Here’s an overview of the most significant innovations reshaping the industry.
Advanced Material Technologies
Nano-Engineered Fibers
Nanotechnology has revolutionized cut resistant materials through:
- Nano-particle Infusion: Incorporating ceramic or metal nano-particles into fiber structures to enhance cut resistance without adding weight
- Molecular Alignment Techniques: Optimizing fiber structures at the molecular level for maximum strength
- Self-Healing Polymers: Experimental materials that can repair minor damage automatically, extending glove lifespan
Hybrid Composite Materials
New composite approaches combine different materials for synergistic protection:
- Multi-layer Composites: Strategically layered materials providing different protection properties
- Gradient Protection Systems: Varying cut resistance levels in different glove areas based on injury risk analysis
- Fiber Blending Optimization: Computer-modeled blends that maximize protection while minimizing cost and weight
Bio-based Cut Resistant Materials
Sustainable alternatives to petroleum-based fibers are emerging:
- Cellulose Nanofiber Reinforcement: Plant-based nanofibers that enhance cut resistance in eco-friendly compositions
- Chitin-derived Fibers: Utilizing shellfish waste to create biodegradable cut resistant materials
- Agricultural Waste Utilization: Converting crop residues into high-performance protective fibers
Manufacturing Process Innovations
Advanced Knitting Technologies
New manufacturing techniques are enhancing glove performance and efficiency:
- Variable Gauge Knitting: Single-process production of gloves with different thicknesses in different areas
- Seamless 3D Knitting: Eliminating seams for enhanced comfort and reduced failure points
- Digital Knitting Control Systems: Computer-optimized knitting patterns for maximum cut resistance with minimum material
Coating Application Advances
Coating technologies have progressed significantly:
- Micro-porous Coatings: Enhanced breathability while maintaining grip and protection
- Gradient Application Systems: Varying coating thickness in different areas for optimized performance
- Water-based Environmentally Friendly Formulations: Reducing chemical exposure and environmental impact
Smart Manufacturing Systems
Industry 4.0 approaches are transforming production facilities:
- IoT-enabled Quality Monitoring: Real-time testing and adjustment during production
- AI-optimized Production Planning: Reducing waste and improving efficiency
- Digital Twin Simulation: Virtual testing of design changes before physical implementation
Performance-Enhancing Features
Ergonomic Innovations
User comfort and productivity are driving significant innovations:
- Anatomical Mapping Technology: Designing gloves based on hand movement studies for reduced fatigue
- Targeted Flexibility Zones: Strategic placement of more flexible materials for dexterity
- Anti-vibration Integration: Combining cut resistance with vibration dampening for power tool users
Sensory Enhancement Technologies
Maintaining tactile sensitivity while providing protection:
- Thin-film Touch Compatibility: Ultra-thin coatings compatible with touchscreens
- Pressure-Point Optimization: Enhanced sensitivity at fingertips while maintaining protection
- Thermal Regulation Systems: Materials that adapt to temperature changes for all-weather comfort
Extended Functionality Integration
Modern cut resistant gloves increasingly incorporate additional features:
- Antimicrobial Treatments: Preventing odor and contamination in food processing and healthcare
- Chemical Resistance Layers: Combining cut and chemical protection for hazardous materials handling
- Impact Protection Zones: Integrating TPR padding for knuckle and back-of-hand protection
Industry Case Study: Qingdao Snell’s Innovation Leadership
Qingdao Snell demonstrates several cutting-edge approaches in their manufacturing processes. Their R&D department continuously evaluates new materials and manufacturing techniques to enhance their cut resistant glove offerings. Some of their notable innovations include:
- Advanced Composite Liners: Proprietary blends of HPPE, glass fiber, and other engineered materials optimized for different cut resistance levels
- Ergonomic Coating Technology: Precision application systems that maintain breathability while enhancing grip performance
- Customized Protection Mapping: Designing gloves with varying protection levels based on specific industry risk assessments
- Sustainable Manufacturing Processes: Water-based coatings and energy-efficient production systems that reduce environmental impact
These innovations allow Qingdao Snell to offer OEM customers cutting-edge products that address specific industrial challenges. Their commitment to continuous improvement ensures their manufacturing capabilities remain at the forefront of the industry.
Future Trends on the Horizon
Looking beyond 2025, several emerging technologies show promise for the next generation of cut resistant gloves:
- Active Protection Systems: Materials that stiffen instantly upon impact with sharp objects
- Integrated Sensing Capabilities: Smart gloves that detect proximity to dangerous equipment
- Biodegradable High-Performance Materials: Fully compostable gloves that maintain ANSI/ISEA A4+ cut resistance
- Energy-Harvesting Elements: Utilizing worker movement to power integrated safety features
By partnering with forward-thinking OEM manufacturers who invest in these innovations, businesses can provide their workforce with the most advanced protection available while potentially reducing long-term costs through improved durability and functionality.
Frequently Asked Questions About Cut Resistant Gloves OEM Manufacturing
General OEM Manufacturing Questions
Q: What is the typical lead time for OEM cut resistant gloves?
A: Standard lead times vary by manufacturer but typically range from 30-60 days after order confirmation and sample approval. For more complex custom designs or during peak seasons, lead times may extend to 60-90 days. Qingdao Snell maintains efficient production schedules, with typical lead times of 30-45 days for most orders.
Q: How do cut resistance levels compare between different standards?
A: Cut resistance standards vary by region, with the primary systems being the ANSI/ISEA 105 (A1-A9) used in North America and EN 388 (A-F) used in Europe. The following table provides an approximate correlation:
ANSI/ISEA 105 Level | Cut Resistance (grams) | EN 388:2016 Level | Cut Resistance (Newtons) |
---|---|---|---|
A1 | 200-499 | A | 2 |
A2 | 500-999 | B | 5 |
A3 | 1000-1499 | C | 10 |
A4 | 1500-2199 | D | 15 |
A5 | 2200-2999 | E | 22 |
A6-A9 | 3000+ | F | 30+ |
Q: Can I get samples before placing a full production order?
A: Most reputable OEM manufacturers provide sampling options before full production. These typically include:
- Standard product samples (often with nominal fees)
- Customized pre-production samples (usually charged but may be credited against full orders)
- Production validation samples from your actual production run
Q: What information should I provide when requesting an OEM quote?
A: To receive an accurate quote, provide:
- Cut resistance level required
- Glove style and coating type
- Size range and distribution
- Quantity per order
- Customization requirements (colors, logo, packaging)
- Target markets (for compliance requirements)
- Delivery location and preferred shipping method
Customization and Branding Questions
Q: What are the minimum quantities for different levels of customization?
A: Customization minimums vary by complexity:
Customization Level | Typical Minimum Quantity |
---|---|
Standard gloves with printed logo | 1,000-3,000 pairs |
Custom color liner with logo | 3,000-5,000 pairs |
Fully custom design and materials | 5,000-10,000 pairs |
Custom packaging only | 1,000-2,000 pairs |
Qingdao Snell’s MOQ ranges from 3,000-20,000 pieces depending on the complexity of customization required.
Q: Can OEM manufacturers help with design and specification development?
A: Many established manufacturers offer design assistance services including:
- Material selection guidance based on application requirements
- Prototype development and testing
- Compliance advisory for target markets
- Cost optimization suggestions
- Performance enhancement recommendations
Q: How many colors can be included in logo printing on cut resistant gloves?
A: Most manufacturers offer:
- 1-2 colors as standard options
- 3-4 colors with potential additional setup costs
- Full-color printing for certain glove types and larger orders
- Special options like reflective printing for high-visibility requirements
Quality and Compliance Questions
Q: How do OEM manufacturers ensure consistent quality across production runs?
A: Reliable manufacturers implement multi-level quality control processes:
- Raw material testing and certification
- In-process quality checks at critical production points
- Finished product testing based on statistical sampling
- Regular calibration of testing equipment
- Documentary traceability systems for each production batch
Q: What certifications should I require from my OEM manufacturer?
A: Key certifications to verify include:
- Quality management: ISO 9001
- Environmental management: ISO 14001
- Testing laboratory accreditation: ISO 17025
- Product-specific certifications: CE, ANSI/ISEA 105 compliance
- Social compliance for export to certain markets: BSCI, SEDEX, etc.
Q: How often should cut resistant gloves be re-tested for compliance?
A: Best practices include:
- Initial certification before market introduction
- Re-testing with any material or construction changes
- Periodic verification testing (typically annually)
- Batch testing for high-risk applications or large volume orders
Business and Logistics Questions
Q: What payment terms are standard in the OEM glove manufacturing industry?
A: Typical payment structures include:
- 30% deposit with order, 70% before shipment (most common)
- Letter of Credit (L/C) for larger orders
- 100% payment in advance for small orders or new relationships
- Graduated terms for established relationships (e.g., 30/70 moving to net 30 after history)
Q: How are intellectual property rights protected in OEM manufacturing?
A: Protect your designs and innovations through:
- Non-disclosure agreements (NDAs) before sharing specifications
- Clearly defined IP ownership clauses in manufacturing agreements
- Limiting technical details to what’s necessary for production
- Working with manufacturers with established ethics and reputation
- Considering patent or trademark protection for unique innovations
Q: What shipping and logistics options are available for international orders?
A: Common shipping methods include:
- Sea freight (most economical for large orders, 30-45 days transit)
- Air freight (faster but more expensive, 5-10 days transit)
- Express courier (fastest option for samples or urgent small shipments)
- Combined methods (split shipments by priority)
Q: Does Qingdao Snell offer private labeling services?
A: Yes, Qingdao Snell provides comprehensive private labeling options including custom logo printing, packaging design, product inserts, and brand identity integration. Their in-house design team can assist with creating brand-consistent visual elements while ensuring all regulatory information is properly displayed. With their MOQ of 3,000-20,000 pieces, they can accommodate both growing brands and established distributors.
For additional questions about cut resistant glove OEM manufacturing, contact Qingdao Snell’s technical team directly for application-specific guidance and customized solutions for your industry requirements.