OEM Anti-Impact Gloves Factory: Complete Guide for Buyers in 2025
April 13, 2025
Share This Article
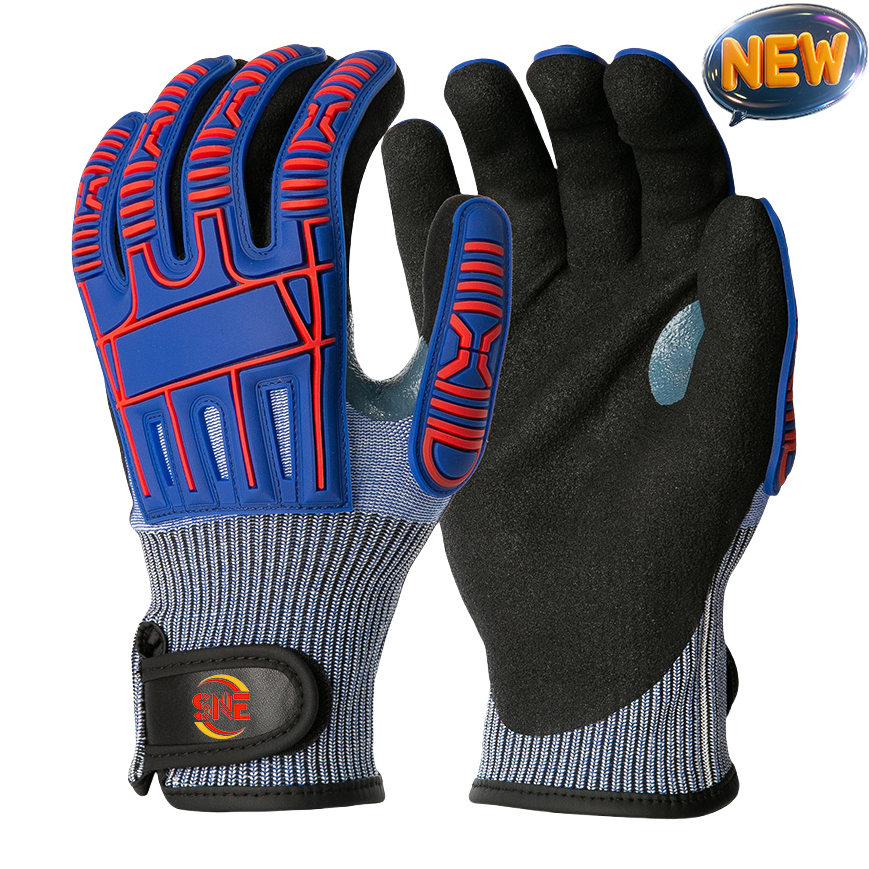
In today’s industrial landscape, worker safety remains a paramount concern for businesses across all sectors. Among the critical personal protective equipment (PPE) needed to ensure workplace safety, anti-impact gloves stand out as essential gear for protecting hands against severe impacts, crushes, and pinches. As we move through 2025, the demand for high-quality anti-impact gloves continues to rise, with companies seeking reliable OEM manufacturers to provide customized solutions that meet their specific industry requirements.
What Are Anti-Impact Gloves and Why Are They Essential?
Anti-impact gloves are specialized hand protection designed with reinforced padding, typically made of TPR (Thermoplastic Rubber), TPU (Thermoplastic Polyurethane), or other impact-resistant materials strategically placed on the back of the hand and fingers. These reinforcements absorb and dissipate impact energy, protecting the wearer’s hands from blunt force trauma, crushes, and pinches that commonly occur in industries like oil and gas, construction, mining, and heavy manufacturing.
Unlike standard work gloves, anti-impact gloves feature distinctive dorsal protection systems with flexible, segmented padding that follows the natural movement of the hand while providing substantial impact resistance. This specialized design addresses a critical gap in hand protection that regular gloves cannot fulfill.
The importance of anti-impact gloves cannot be overstated, particularly when we consider that hand injuries constitute approximately 20% of all workplace injuries globally. According to recent industry reports, proper impact-resistant gloves can reduce the severity of hand injuries by up to 60%, representing significant savings in terms of worker compensation, lost productivity, and medical expenses.
Industries that particularly benefit from anti-impact gloves include:
- Oil and gas extraction
- Mining and quarrying
- Construction and demolition
- Heavy manufacturing
- Automotive assembly
- Material handling
- Logging and forestry
- Offshore operations
- Railroad operations
- Waste management
These specialized gloves have evolved significantly over the past decade, with modern versions offering not just impact protection but also cut resistance, oil grip, waterproofing, touchscreen compatibility, and enhanced comfort features—all while maintaining the dexterity workers need to perform precise tasks.
How to Choose the Best Anti-Impact Gloves for Your Business?
Selecting the right anti-impact gloves for your specific business needs requires careful consideration of several crucial factors. Making the wrong choice could compromise worker safety, reduce productivity, or result in unnecessary expenses. Here’s a comprehensive approach to finding the perfect anti-impact gloves for your operation:
1. Identify Your Specific Industry Requirements
Different industries present different hazards. For instance, oil and gas operations typically require gloves with excellent oil resistance alongside impact protection, while construction may prioritize grip in various weather conditions. Mining operations might need additional cut protection, and automotive assembly could require enhanced dexterity for handling small parts.
Begin by conducting a thorough hazard assessment of your workplace to identify all potential hand injury risks. This assessment should document the types of impacts, chemicals, temperatures, and other hazards workers’ hands are exposed to during regular operations.
2. Understand Impact Protection Standards
When evaluating anti-impact gloves, familiarize yourself with relevant protection standards:
- EN 388:2016 – The European standard that includes impact protection testing (marked with “P” for pass)
- ANSI/ISEA 138-2019 – American standard specifically for impact-resistant gloves, rating protection from Level 1 (lowest) to Level 3 (highest)
- AS/NZS 2161.3 – Australia/New Zealand standard similar to EN 388
Look for gloves that meet or exceed the standards relevant to your region and industry. Remember that higher levels of certification generally indicate better protection, but might come with trade-offs in dexterity or comfort.
3. Consider Material and Construction Quality
The effectiveness of anti-impact gloves depends heavily on their construction and materials:
Back-of-Hand Protection:
- TPR (Thermoplastic Rubber) – Flexible, durable, and offers good impact resistance
- TPU (Thermoplastic Polyurethane) – Typically lighter and more flexible than TPR
- D3O® – Advanced impact-absorbing material that stiffens upon impact
- EVA foam – Lightweight but offers less protection than other materials
Palm Materials:
- Synthetic leather (microfiber) – Durable and provides good dexterity
- Genuine leather – Excellent abrasion resistance and durability
- Nitrile or PVC coatings – Enhanced grip in oily conditions
- Technical fabrics – May offer additional features like cut resistance
The quality of stitching, seams, and overall construction significantly affects the glove’s durability and protection level. Premium gloves often feature reinforced stitching and seamless designs in critical areas.
4. Balance Protection with Dexterity and Comfort
One of the biggest challenges in selecting anti-impact gloves is finding the right balance between protection and usability. Overly bulky gloves might offer excellent protection but can reduce productivity if workers cannot perform their tasks efficiently or are tempted to remove gloves that are uncomfortable.
Consider these factors affecting comfort and dexterity:
- Glove weight and flexibility
- Breathability and moisture management
- Ergonomic design that follows hand contours
- Liner materials and internal seam construction
- Wrist closure systems for secure fit without restriction
Qingdao Snell Protective Products has developed innovative anti-impact gloves that provide excellent protection while maintaining remarkable dexterity through strategic padding placement and flexible joint designs.
5. Evaluate Additional Protection Features
Modern anti-impact gloves often incorporate multiple protection features beyond impact resistance:
- Cut Resistance – Measured on scales like ANSI A1-A9 or EN 388 (A-F)
- Puncture Resistance – Essential for industries with sharp object hazards
- Chemical Resistance – Important for oil, gas, and chemical processing
- Heat/Cold Resistance – Critical for extreme temperature environments
- Vibration Dampening – Beneficial for tools that produce significant vibration
- Waterproofing – Essential for outdoor or wet environment applications
6. Consider Cost vs. Longevity
While premium anti-impact gloves may have higher upfront costs, they typically offer better protection and longer service life, resulting in lower cost per wear. Calculate the total ownership cost by considering:
- Initial purchase price
- Expected lifespan based on work conditions
- Replacement frequency
- Potential reduction in workplace injuries
- Worker satisfaction and compliance with safety protocols
Investing in higher-quality gloves often results in better overall value, even at premium price points. However, this calculation varies by industry and usage intensity.
Where to Buy High-Quality Anti-Impact Gloves?
Finding reliable sources for anti-impact gloves is crucial for ensuring worker safety and product consistency. Here are the primary channels through which businesses can purchase quality anti-impact gloves in 2025:
Direct from OEM Manufacturers
Working directly with OEM (Original Equipment Manufacturer) glove factories provides several advantages, particularly for companies requiring large quantities or customized specifications:
Benefits:
- Customization options for materials, designs, and branding
- Potentially lower per-unit costs when ordering in bulk
- Direct communication with production teams
- Quality control oversight opportunities
- Ability to develop proprietary designs
Considerations:
- Typically requires larger minimum order quantities (MOQs)
- Longer lead times for production and shipping
- May require more hands-on management of the procurement process
Established manufacturers like Qingdao Snell have streamlined their direct procurement processes, offering online consultations and sample programs to simplify the ordering process for international clients.
Industrial Safety Distributors
Safety equipment distributors serve as intermediaries between manufacturers and end-users, often providing additional services:
Benefits:
- Local inventory and faster delivery
- Technical advice and product selection assistance
- Opportunity to purchase smaller quantities
- Consolidated purchasing from multiple manufacturers
- Value-added services like training and fitting
Considerations:
- Higher per-unit costs compared to direct manufacturer purchasing
- Limited customization options
- Possible stock limitations for specialized models
Major industrial distributors have expanded their anti-impact glove selections significantly in recent years, recognizing the growing demand for this specialized protection.
Online B2B Marketplaces
Digital procurement platforms have become increasingly important channels for sourcing anti-impact gloves:
Benefits:
- Easy comparison between multiple suppliers
- User reviews and ratings
- Convenient ordering process
- Often lower minimum order requirements
- Global manufacturer access
Considerations:
- Variable quality control and verification processes
- Potential communication challenges with international suppliers
- Limited ability to inspect products before purchasing
When using online marketplaces, look for verified suppliers with robust certification documentation and be wary of products with pricing significantly below market averages, as these may involve quality compromises.
Industry-Specific Equipment Suppliers
Some industries have specialized equipment suppliers that offer PPE tailored to their specific needs:
Benefits:
- Deep understanding of industry-specific requirements
- Pre-selected gloves that meet relevant standards
- Often provide technical support and training
- May offer industry-specific customizations
Considerations:
- Potentially higher pricing due to specialization
- More limited selection compared to general suppliers
- May not carry the latest innovations from all manufacturers
These suppliers are particularly valuable for industries with unique hazards or regulatory requirements, such as mining, electrical work, or chemical processing.
Anti-Impact Gloves Manufacturer in China
China has emerged as a global leader in the production of anti-impact gloves, combining cost efficiency with increasingly advanced manufacturing capabilities. The Chinese anti-impact glove manufacturing landscape has evolved significantly, with many factories transitioning from basic work gloves to sophisticated protective equipment incorporating the latest materials and technologies.
Key Manufacturing Regions
China’s production of anti-impact gloves is concentrated in several industrial clusters:
- Shandong Province – Particularly around Qingdao, Gaomi, and Yantai, this region specializes in industrial gloves with advanced protection features. Companies like Qingdao Snell operate modern production facilities here.
- Zhejiang Province – Known for technical textiles and innovative materials, manufacturers in this region often focus on high-end, specialized gloves incorporating advanced impact-absorbing technologies.
- Guangdong Province – This manufacturing hub specializes in gloves with electronic assembly applications, offering impact protection alongside ESD (electrostatic discharge) protection and high dexterity.
- Hebei Province – Traditional strength in leather processing has evolved into expertise in combination gloves featuring leather palms with synthetic impact protection.
Advantages of Chinese Manufacturers
Chinese anti-impact glove factories offer several distinct advantages:
- Integrated Supply Chains – Many manufacturers maintain close relationships with material suppliers, allowing for innovation and cost efficiencies. Complete vertical integration is increasingly common.
- Scale and Production Capacity – The largest factories operate multiple production lines with capacity reaching millions of pairs annually, enabling them to fulfill large orders efficiently.
- Competitive Pricing – While prices have increased in recent years, Chinese manufacturers generally maintain cost advantages due to efficient production systems and established supply chains.
- Improving Quality Standards – Leading manufacturers have implemented rigorous quality control systems, with many now certified to international standards including ISO 9001, ISO 14001, and specific PPE testing standards.
- Manufacturing Flexibility – Chinese factories often demonstrate remarkable adaptability in adjusting production specifications to meet client requirements.
Notable Chinese Anti-Impact Glove Manufacturers
Several Chinese manufacturers have established strong reputations in the anti-impact glove sector:
Qingdao Snell Protective Products Co., Ltd.
Founded in 2024 but built on over a decade of production expertise, Qingdao Snell operates advanced production facilities in Gaomi and Nantong with six specialized production lines. The company has earned ISO 9001 and CE certifications, specializing in PU, latex, and nitrile-coated gloves with impact protection. Their anti-impact gloves are particularly known for maintaining excellent dexterity while providing comprehensive dorsal protection.
Qingdao Snell’s impact gloves feature innovative designs for automotive, construction, and oil/gas applications, with MOQs ranging from 3,000 to 20,000 pairs depending on customization requirements. Their direct factory supply model eliminates middlemen, resulting in competitive pricing without compromising quality.
Other Notable Manufacturers
- Several large-scale manufacturers in Shandong and Zhejiang provinces have developed specialized anti-impact lines
- Multiple factories offering various price/quality combinations to meet different market segments
- Emerging manufacturers focused exclusively on high-tech impact protection solutions
Challenges and Considerations
When working with Chinese anti-impact glove manufacturers, buyers should be aware of several factors:
- Quality Variation – Significant differences exist between manufacturers; thorough vetting through samples, factory audits, and certification verification is essential.
- Communication – While improving rapidly, language barriers and time zone differences can complicate project management. Many leading manufacturers now employ international sales teams to address this.
- Shipping Logistics – Production lead times typically range from 25-45 days, with shipping adding 30-45 days for sea freight. Air shipping is available but significantly increases costs.
- Intellectual Property Considerations – Buyers with proprietary designs should implement appropriate protections through contracts and selective disclosure of technologies.
- Minimum Order Quantities – Most manufacturers require MOQs starting at 1,000-3,000 pairs for standard models and 3,000-10,000 pairs for customized designs. Some premium manufacturers like Qingdao Snell can accommodate flexible ordering terms for established clients.
Anti-Impact Gloves Manufacturers in the USA
The United States maintains a significant presence in the anti-impact glove manufacturing sector, with a focus on innovation, specialized applications, and premium market segments. American manufacturers generally emphasize advanced technologies, strict quality control, and comprehensive compliance with domestic and international standards.
Characteristics of US Manufacturing
American anti-impact glove production is distinguished by several key features:
- Innovation Focus – US manufacturers frequently lead in developing new impact-absorbing technologies and materials, often partnering with research institutions and material scientists.
- Specialized Applications – Many US manufacturers concentrate on niche markets with specific requirements, such as military applications, extreme environments, or specialized industries with unique hazards.
- Vertical Integration – Leading US manufacturers maintain control over critical aspects of production, from material development to final testing, ensuring consistent quality.
- Regulatory Compliance – American producers typically maintain comprehensive compliance with ANSI, OSHA, and industry-specific regulations, often exceeding minimum requirements.
- Domestic Supply Chain Emphasis – In response to recent supply chain disruptions, many US manufacturers have prioritized domestic material sourcing and production.
Regional Manufacturing Centers
US anti-impact glove production is distributed across several manufacturing hubs:
- Northeast – Traditional manufacturing centers in Pennsylvania, New York, and Massachusetts focus on specialized industrial applications.
- Southeast – North Carolina, Georgia, and Tennessee host manufacturers emphasizing cost-effective production for mass-market applications.
- Midwest – Ohio, Michigan, and Illinois have manufacturers specializing in automotive and heavy industry applications, often with close ties to those industrial bases.
- West Coast – California and Washington state producers frequently emphasize technological innovation and specialty applications for aerospace and advanced manufacturing.
Market Position and Production Scale
US manufacturers generally operate with different scale and market positioning compared to their Asian counterparts:
- Production Volume – Typically smaller production runs with higher degrees of customization
- Price Positioning – Generally premium pricing reflecting higher labor costs and specialized features
- Market Focus – Strong emphasis on domestic market and specialized export niches
- Response Time – Shorter lead times for domestic orders, ability to rapidly prototype and modify designs
- Customization – Extensive customization options, including specialized features for specific workplaces
Advantages of US Manufacturers
American anti-impact glove producers offer several distinct advantages:
- Quality Assurance – Rigorous testing and quality control systems, often with batch-level traceability
- Technical Support – Extensive pre-sale consultation and post-sale support
- Product Development Collaboration – Willingness to work closely with clients on developing solutions for specific applications
- Regulatory Expertise – Deep understanding of US safety standards and compliance requirements
- Rapid Delivery – Shorter supply chains for domestic customers with expedited production capabilities
- Made in USA Marketing Value – For some customers, domestically produced PPE carries marketing and procurement advantages
Challenges Facing US Manufacturers
American anti-impact glove production faces several ongoing challenges:
- Production Costs – Higher labor, compliance, and facility costs compared to overseas manufacturers
- Scale Limitations – Smaller production capacity compared to large Asian factories
- Material Supply Chain – Some specialized materials still require international sourcing
- Price Competition – Constant pressure from lower-cost imports, particularly in less specialized segments
- Labor Availability – Ongoing challenges in recruiting skilled manufacturing workforce
Despite these challenges, American anti-impact glove manufacturing remains viable through specialization, innovation, and focus on market segments that value their particular advantages.
Anti-Impact Gloves Suppliers in Europe
Europe maintains a distinguished position in the anti-impact gloves market, with manufacturers focusing on innovation, strict compliance with regional regulations, and exceptional quality standards. European suppliers typically emphasize sustainability, ergonomic design, and comprehensive worker protection that often exceeds minimum safety requirements.
European Manufacturing Landscape
The European anti-impact glove industry is characterized by:
- Regulatory Excellence – European manufacturers design products around the continent’s stringent safety standards, particularly EN 388:2016 (which includes specific impact testing) and the broader PPE Regulation (EU) 2016/425.
- Research-Driven Innovation – Strong connections between manufacturers and research institutions lead to advanced materials and protection technologies, with European companies frequently holding key patents.
- Regional Specialization – Different European countries have developed unique areas of expertise:
- Germany: Engineering-focused designs with precision manufacturing
- UK: Oil and gas industry specialization and offshore applications
- France: High-fashion influences even in industrial designs
- Nordic countries: Cold-weather performance and ergonomics
- Italy: Premium materials and craftsmanship with aesthetic consideration
- Sustainability Focus – European manufacturers increasingly emphasize environmental considerations, including:
- Biodegradable and recycled materials
- Energy-efficient production processes
- Extended product lifecycles
- Take-back and recycling programs
- Reduced chemical usage and water consumption
Advantages of European Suppliers
European anti-impact glove suppliers offer several distinct benefits:
- Comprehensive Certifications – Products typically undergo extensive testing and certification processes, with detailed documentation available to buyers.
- Ergonomic Design – European manufacturers place particular emphasis on user comfort, fit, and reducing hand fatigue through advanced ergonomic principles.
- Material Innovation – Development of proprietary impact-absorbing materials that often provide better protection with less bulk than conventional options.
- Quality Consistency – Rigorous quality control systems ensure product uniformity across production runs.
- Customization Capabilities – Many European manufacturers offer sophisticated customization options, including specialized protection zones for specific industry hazards.
- After-Sales Support – Comprehensive technical support, training resources, and warranty programs typically accompany products.
Market Positioning
European suppliers generally position themselves in the premium and specialized segments of the anti-impact glove market:
- Price Point – Higher pricing reflecting advanced materials, greater R&D investment, and higher production costs.
- Target Industries – Particular focus on high-risk, highly regulated industries such as:
- Offshore oil and gas
- Railway maintenance
- Advanced manufacturing
- Chemical processing
- Aerospace
- Mining and tunneling
- Emergency services
- Distribution Strategy – Most European manufacturers utilize specialized distribution networks with technical expertise rather than mass-market channels.
Challenges for European Manufacturers
European anti-impact glove producers face several ongoing challenges:
- Production Costs – Higher labor, energy, and compliance costs compared to manufacturers in other regions.
- Global Competition – Increasing pressure from international manufacturers adopting European standards but with lower cost structures.
- Market Fragmentation – Despite EU harmonization, different national preferences and procurement systems create complexity.
- Raw Material Dependencies – Some specialized materials require global sourcing, creating supply chain vulnerabilities.
- Labor Market Pressures – Challenges in recruiting skilled manufacturing workers in many European countries.
Despite these challenges, European manufacturers maintain significant market share through technical leadership, quality reputation, and regulatory expertise.
Comparison of Anti-Impact Glove Manufacturers in Different Countries
When sourcing anti-impact gloves for your business, understanding the comparative advantages of manufacturers from different regions can help you make more informed procurement decisions. Each manufacturing region offers distinct benefits and considerations that may align differently with your specific requirements.
Manufacturing Region | Cost Efficiency | Quality Control | Innovation | Customization | Minimum Order Quantities | Lead Times | Regulatory Compliance |
---|---|---|---|---|---|---|---|
China | ★★★★★ | ★★★☆☆ to ★★★★★ (varies significantly by manufacturer) | ★★★☆☆ | ★★★★☆ | 1,000-10,000 pairs (Qingdao Snell: 3,000-20,000) | 25-45 days production + 30-45 days shipping | ★★★☆☆ to ★★★★☆ |
USA | ★★☆☆☆ | ★★★★★ | ★★★★☆ | ★★★★★ | 250-1,000 pairs | 15-30 days total | ★★★★★ |
Europe | ★★☆☆☆ | ★★★★★ | ★★★★★ | ★★★★☆ | 300-1,500 pairs | 20-40 days total | ★★★★★ |
Southeast Asia | ★★★★☆ | ★★★☆☆ | ★★☆☆☆ | ★★★☆☆ | 1,000-5,000 pairs | 30-50 days total | ★★★☆☆ |
India | ★★★★☆ | ★★☆☆☆ to ★★★☆☆ | ★★☆☆☆ | ★★★☆☆ | 1,000-3,000 pairs | 30-60 days total | ★★★☆☆ |
Detailed Regional Comparisons
China vs. USA:
Chinese manufacturers like Qingdao Snell offer significant cost advantages and larger production capacity, making them ideal for high-volume orders. Their minimum order quantities typically start at 3,000 pairs, compared to as low as 250 pairs for some US manufacturers. However, US producers generally provide faster delivery to North American customers, more hands-on technical support, and often exceed regulatory requirements.
Europe vs. China:
European manufacturers excel in advanced technical innovations and ergonomic design, particularly for specialized applications. Their products typically feature proprietary materials and protection systems that may outperform standard offerings from Chinese factories. However, this comes at a premium price point often 40-80% higher than comparable Chinese products. Chinese manufacturers like Qingdao Snell have narrowed this gap in recent years by investing in advanced production technologies and quality control systems.
USA vs. Europe:
US and European manufacturers share similar quality standards and price points, but with subtle differences in focus. US producers often emphasize practical functionality and compatibility with American workplace practices, while European manufacturers may place greater emphasis on ergonomic refinement and environmental sustainability. Regulatory approaches also differ, with US manufacturers focusing on ANSI standards while European producers build around EN standards.
Southeast Asia vs. China:
Emerging manufacturing nations in Southeast Asia (particularly Vietnam and Malaysia) offer cost structures similar to China but typically with less developed technical capabilities and smaller production capacity. These regions present growing alternatives for basic anti-impact glove styles but generally lag behind Chinese manufacturers in advanced features and customization options.
Strategic Sourcing Considerations
When comparing manufacturers across regions, consider these strategic factors:
- Volume Requirements – For large-volume orders (10,000+ pairs), Chinese manufacturers like Qingdao Snell offer significant economies of scale that may outweigh other considerations.
- Technical Complexity – For highly specialized applications with unique protection requirements, European or US manufacturers may offer technical advantages that justify premium pricing.
- Lead Time Sensitivity – When rapid delivery is critical, proximity to your location becomes more important, potentially favoring domestic or regional suppliers.
- Customization Needs – All regions offer customization, but depth of capabilities varies. US manufacturers typically offer the most extensive customization for small runs, while Chinese manufacturers like Qingdao Snell provide excellent customization for larger volumes.
- Compliance Requirements – For products requiring extensive documentation and certification, European and US manufacturers typically provide more comprehensive compliance packages.
- Long-term Partnership – Consider not just the initial order but the potential for ongoing collaboration. Manufacturers with strong R&D capabilities can become valuable partners in developing future hand protection solutions.
What to Look for in a Reliable OEM Anti-Impact Gloves Factory
Selecting the right OEM partner for anti-impact gloves is a critical decision that affects not only product quality and worker safety but also your supply chain reliability and total cost of ownership. Here are the essential factors to evaluate when assessing potential manufacturing partners:
1. Manufacturing Capabilities and Facility Assessment
A thorough evaluation of the manufacturer’s production facilities provides crucial insights into their capabilities:
Production Capacity:
- Number and type of production lines
- Maximum monthly output capacity
- Ability to scale production during peak demand periods
- Backup production capabilities for business continuity
Manufacturing Technology:
- Age and condition of manufacturing equipment
- Level of automation in critical processes
- In-house testing facilities and equipment
- Pattern-making and prototype development capabilities
Facility Conditions:
- General cleanliness and organization
- Worker safety provisions
- Material storage conditions
- Quality control checkpoints throughout production
Qingdao Snell operates modern facilities with six specialized production lines across their Gaomi and Nantong factories, enabling them to produce various glove styles simultaneously while maintaining consistent quality standards.
2. Quality Management Systems
The manufacturer’s approach to quality management directly affects the consistency and reliability of their products:
Certifications to Verify:
- ISO 9001:2015 quality management certification
- Industry-specific certifications (ISO 45001 for occupational health and safety)
- Product-specific certifications (EN 388, ANSI/ISEA 138)
- Environmental management systems (ISO 14001)
Quality Control Processes:
- Incoming material inspection protocols
- In-process quality checks at critical production stages
- Final product testing procedures and sampling rates
- Documentation and traceability systems
Testing Capabilities:
- In-house testing facilities for routine quality verification
- Relationships with accredited third-party testing laboratories
- Documented testing protocols aligned with relevant standards
- Historical test results and consistency records
3. Materials and Component Sourcing
The quality of raw materials significantly impacts the performance and durability of anti-impact gloves:
Material Supply Chain:
- Sources of critical materials (impact-absorbing compounds, palm materials, etc.)
- Quality verification processes for incoming materials
- Material stock levels and supply chain resilience
- Alternative material sources for business continuity
Material Innovation:
- Research and development capabilities
- Partnerships with material suppliers for custom solutions
- Ability to incorporate new materials as they become available
- Continuous improvement in material performance
Material Compliance:
- REACH compliance for chemical components
- Documentation of material properties and performance
- Restricted substance testing and verification
- Material safety data sheets and chemical inventories
4. Design and Development Capabilities
A manufacturer’s ability to develop and refine designs affects their value as a long-term partner:
Design Expertise:
- In-house design team qualifications and experience
- Previous design innovation examples
- 3D modeling and digital design capabilities
- Prototyping processes and speed
Development Process:
- Structured product development methodology
- Timeline for moving from concept to production
- Sample development and refinement process
- Design validation and verification procedures
Customization Abilities:
- Experience with client-specific design requirements
- Capacity to modify standard designs to meet specific needs
- Color matching and branding capabilities
- Minimum quantities for customized products
5. Compliance and Documentation
Comprehensive documentation is essential for regulatory compliance and risk management:
Required Documentation:
- Product technical files
- Test reports from accredited laboratories
- Declaration of Conformity for applicable standards
- Safety data sheets and user instructions
Regulatory Knowledge:
- Understanding of market-specific requirements (EU, US, etc.)
- Compliance with local and international labor laws
- Environmental compliance documentation
- Export documentation capabilities
6. Business Practices and Ethics
The manufacturer’s business approach affects the long-term viability of the partnership:
Communication:
- Responsiveness to inquiries
- English proficiency of key contacts
- Communication systems and technology
- Transparency in addressing problems
Business Ethics:
- Social compliance certifications (BSCI, SMETA, etc.)
- Working conditions and labor practices
- Environmental responsibility initiatives
- Intellectual property protection practices
Financial Stability:
- Years in business
- Client references and longevity of client relationships
- Business registration and legal status
- Credit references or financial disclosures when appropriate
7. Service and Support
The level of service provided by the manufacturer can significantly impact your operational efficiency:
Order Management:
- Order processing systems
- Production scheduling transparency
- Progress reporting during production
- Ability to accommodate rush orders when needed
Technical Support:
- Product training resources
- Technical documentation quality
- Problem-solving capabilities
- Post-sale technical assistance
Logistics Support:
- Shipping documentation preparation
- Export packaging quality
- Relationships with freight forwarders
- Customs compliance knowledge
MOQ (Minimum Order Quantity) Considerations When Ordering Anti-Impact Gloves
Minimum Order Quantity (MOQ) requirements significantly influence sourcing decisions for anti-impact gloves, particularly when working with OEM manufacturers. Understanding the factors affecting MOQs and strategies for managing them can help optimize your procurement process.
Typical MOQ Structures in the Anti-Impact Glove Industry
MOQ requirements vary significantly based on manufacturer size, location, and business model:
Manufacturer Type | Standard Models MOQ | Custom Models MOQ | Color Customization MOQ | Full Custom Design MOQ |
---|---|---|---|---|
Large Chinese OEMs | 1,000-5,000 pairs | 3,000-10,000 pairs | 3,000-10,000 pairs | 5,000-20,000 pairs |
Qingdao Snell | 3,000 pairs | 5,000 pairs | 5,000 pairs | 10,000-20,000 pairs |
Medium European OEMs | 500-1,500 pairs | 1,000-3,000 pairs | 1,500-3,000 pairs | 3,000-5,000 pairs |
US Manufacturers | 250-1,000 pairs | 500-2,000 pairs | 1,000-2,500 pairs | 2,500-5,000 pairs |
Distributors/Wholesalers | 50-300 pairs | Limited options | Very limited options | Generally unavailable |
Factors Influencing MOQ Requirements
Several key factors determine why manufacturers set specific MOQ levels:
1. Production Economics
Manufacturers set MOQs to achieve production efficiency by:
- Optimizing machine setup times
- Allocating appropriate production line time
- Achieving material purchasing efficiencies
- Managing labor resources effectively
For example, changing production from one glove style to another requires machine reconfiguration, operator training adjustments, and quality control system updates—all of which are more cost-effective when amortized over larger production runs.
2. Material Considerations
Material suppliers typically have their own minimum order requirements, which influence glove manufacturers’ MOQs:
- Specialized impact-resistant materials often have high minimum purchase quantities
- Custom colors for TPR impact protection require minimum dye lots
- Material wastage is proportionally higher on smaller production runs
- Custom materials may require significant minimum purchases from suppliers
3. Design and Development Costs
For customized anti-impact gloves, manufacturers must recoup design and development investments:
- Pattern development and refinement
- Sample production and testing
- Production method engineering
- Quality control procedure development
- Product certification and testing costs
These fixed costs must be distributed across the production quantity, making smaller runs economically challenging.
Strategies for Managing MOQ Requirements
For buyers facing challenges with manufacturer MOQs, several strategies can help bridge the gap between supplier requirements and your actual needs:
1. Phased Ordering Approaches
Work with manufacturers who offer flexible ordering structures:
- Initial smaller order with commitment to future orders
- Blanket purchase orders with scheduled releases
- Deposit-based production reservations with flexible delivery scheduling
Some manufacturers, including Qingdao Snell, may offer more flexible terms for established customers with proven ordering history.
2. Stock Program Participation
Some manufacturers maintain stock programs for popular models:
- Standard designs kept in unbranded inventory
- Lower MOQs for adding branding to stock items
- Quick-ship options from manufacturer inventory
- Participation in stock forecasting programs for priority access
3. Consortium Purchasing
For smaller buyers, collaborative purchasing can help meet MOQs:
- Industry association group purchasing
- Multi-company consolidated orders
- Working through distributors who aggregate demand
- Partnership with complementary businesses for combined orders
4. Model Rationalization
Streamlining your glove selection can help concentrate volume:
- Standardizing on fewer models across departments
- Selecting versatile styles that serve multiple applications
- Focusing customization on critical features only
- Using consistent platforms with application-specific variations
5. MOQ Negotiation Approaches
When discussing MOQs with manufacturers, consider these approaches:
- Demonstrate growth potential and long-term partnership value
- Accept longer lead times in exchange for lower MOQs
- Commit to multi-year purchasing agreements
- Accept slight price premiums for below-standard MOQ orders
Balancing MOQ Constraints with Inventory Management
Finding the optimal balance between meeting manufacturer MOQs and managing your inventory efficiently requires careful planning:
Inventory Carrying Cost Considerations:
- Storage space requirements and costs
- Capital tied up in inventory
- Risk of obsolescence or degradation
- Inventory management administrative costs
Ordering Frequency Strategy:
- Calculate economic order quantity considering both MOQs and carrying costs
- Develop accurate usage forecasting to prevent overstocking
- Implement appropriate inventory management systems
- Create safety stock policies based on lead times and usage variability
Hybrid Approaches:
- Maintain stock of high-usage standard items ordered at full MOQs
- Supplement with smaller quantities of specialized items from distributors
- Use just-in-time approaches where possible
- Implement vendor-managed inventory programs with key suppliers
How to Customize Anti-Impact Gloves with Your Logo and Branding?
Customizing anti-impact gloves with your company branding creates multiple benefits: enhanced professional appearance, improved brand visibility, reduced theft, and easier identification of appropriate PPE for specific tasks. Here’s a comprehensive guide to effectively customizing anti-impact gloves:
Available Customization Methods
Modern manufacturing offers several approaches to customizing anti-impact gloves, each with distinct advantages and limitations:
1. Silicone Heat Transfer
This popular method uses silicone-based ink applied through heat and pressure:
- Advantages: Durable, maintains flexibility, excellent color vibrancy, raised texture option
- Limitations: Limited to flat areas, typically restricted to back of hand or cuff
- Best for: Logos with 1-3 colors, detailed designs requiring durability
- Typical placement: Back of hand (between impact elements), cuff area
2. Pad Printing
A method transferring ink via a silicone pad:
- Advantages: Precise detail reproduction, can print on slightly uneven surfaces
- Limitations: Less durable than other methods, limited color depth
- Best for: Single-color logos, part numbers, simple identification
- Typical placement: Cuff area, fingertips, palm
3. Screen Printing
Traditional method pushing ink through a mesh stencil:
- Advantages: Cost-effective for large quantities, good color consistency
- Limitations: Requires flat surfaces, may crack if on flexible areas
- Best for: Large areas of solid color, simple designs
- Typical placement: Primarily cuff area, occasionally between impact elements
4. Embroidery
Stitched designs for fabric areas:
- Advantages: Premium appearance, excellent durability
- Limitations: Only suitable for fabric areas, adds thickness
- Best for: Cuff branding, high-end gloves
- Typical placement: Restricted to cuff area
5. Molded-In Branding
Logos incorporated directly into TPR impact protection elements:
- Advantages: Seamless integration, maximum durability
- Limitations: Highest setup costs, requires large volumes
- Best for: Large orders, long-term branded products
- Typical placement: Back of hand impact protection elements
6. Custom Color Impact Elements
Using company colors for the TPR impact protection components:
- Advantages: High visibility, brand color reinforcement
- Limitations: Significant MOQs, additional setup costs
- Best for: Complete brand integration, large orders
- Typical placement: All impact protection elements
Customization Design Guidelines
Creating effective customization requires understanding both technical constraints and design best practices:
1. Logo Adaptation
Most company logos need modification for effective application on gloves:
- Simplify complex elements to ensure clarity at small scale
- Consider creating a specialized version optimized for gloves
- Ensure adequate contrast with the glove material color
- Maintain minimum size requirements for legibility
2. Color Selection
Color choices significantly impact visibility and durability:
- Limit designs to 1-3 colors for most applications
- Select colors with good contrast against the glove material
- Consider environment of use (high-visibility in low-light conditions)
- Understand that some colors may require additional charges
3. Placement Optimization
Strategic placement ensures visibility while maintaining protection:
- Back-of-hand placement between impact elements maximizes visibility
- Cuff placement offers larger printing area but less visibility during use
- Side-finger placement provides visibility in certain gripping positions
- Multiple placement locations can reinforce branding but increase costs
4. Size Considerations
Logo size affects both visibility and production costs:
- Standard sizes range from 1-3 inches wide depending on placement
- Minimum detail size is typically 0.5mm for most printing methods
- Text should generally be no smaller than 6pt for legibility
- Allow adequate clear space around logos (minimum 3mm)
Customization Process with Manufacturers
When working with OEM manufacturers like Qingdao Snell, follow these steps for successful customization:
1. Initial Consultation
Begin by discussing your requirements with the manufacturer:
- Provide your existing logo files (vector format preferred)
- Discuss quantity requirements and budget constraints
- Review available methods appropriate for your selected glove style
- Explore special requirements (color matching, multiple locations, etc.)
2. Design Development
Work with the manufacturer to optimize your design:
- Review digital mockups showing logo placement
- Evaluate color options and recommendations
- Consider technical limitations and solutions
- Approve final design specifications
3. Sampling Process
Request samples before full production:
- Physical samples demonstrate actual appearance and placement
- Review durability through wash and wear testing
- Confirm color accuracy under different lighting conditions
- Approve final production sample before full order
4. Production Specifications
Document all customization details clearly:
- Exact Pantone colors to be used
- Precise measurements and placement coordinates
- Approved printing/application method
- Quality control reference standards
Cost Implications of Customization
Customization adds costs through several factors:
Setup Charges:
- One-time fees for creating screens, plates, or embroidery programs
- Typically range from 50−50-50−300 depending on complexity
- May be waived for large orders or repeat business
Unit Cost Increases:
- Per-pair cost additions ranging from 0.20−0.20-0.20−2.00 depending on method
- Multi-color designs increase costs progressively
- Multiple placement locations multiply costs accordingly
Minimum Order Requirements:
- Customization typically increases minimum order quantities
- Standard minimums range from 3,000-5,000 pairs for most methods
- Premium customization (custom colors, molded elements) may require 10,000+ pairs
Cost Optimization Strategies:
- Simplify designs to reduce colors and complexity
- Consolidate orders to meet higher minimums
- Consider standardizing on one design across multiple glove styles
- Explore stock program options with periodic customization runs
Working with established manufacturers like Qingdao Snell provides access to experienced design teams who can help optimize your branding for both impact and cost-effectiveness across their production capabilities.