Anti-Cutting Sleeves Wholesale: Complete Buyer’s Guide in 2025
May 2, 2025
Share This Article
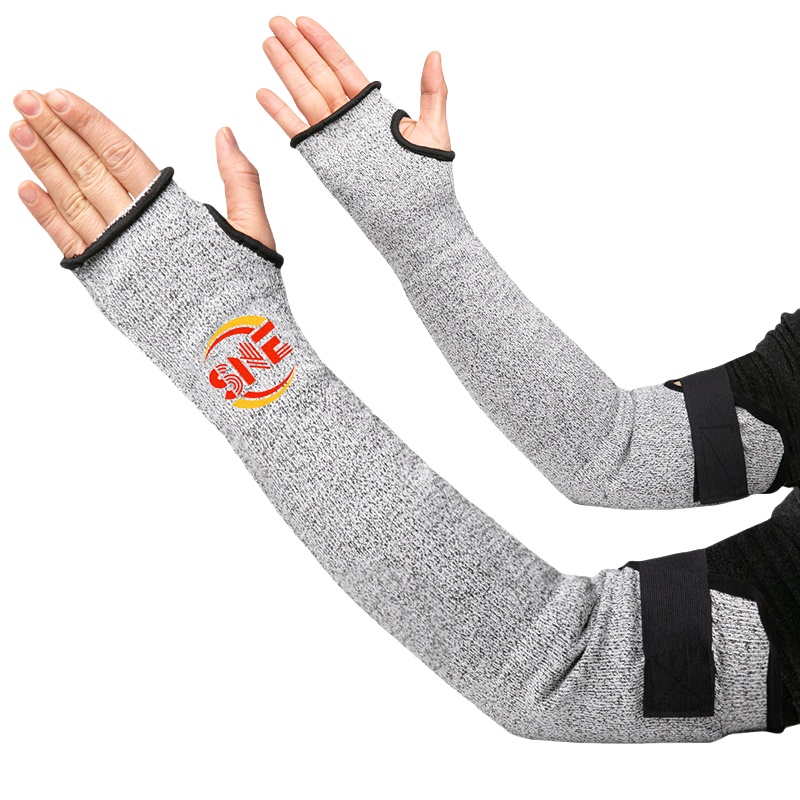
In today’s high-risk industrial environments, protecting workers from cuts and lacerations is paramount for workplace safety. Anti-cutting sleeves have become essential personal protective equipment (PPE) for industries ranging from manufacturing to food processing. This comprehensive guide explores everything you need to know about sourcing wholesale anti-cutting sleeves in 2025, from understanding their advanced materials to finding reliable manufacturers.
What Are Anti-Cutting Sleeves?
Anti-cutting sleeves are specialized protective garments designed to shield the arms and wrists from cuts, abrasions, and punctures. Unlike regular fabric sleeves, these protective accessories are manufactured using high-performance materials specifically engineered to resist cutting forces and prevent injuries in hazardous work environments.
Modern anti-cutting sleeves have evolved significantly from their early iterations. Today’s versions combine multiple advanced materials like high-performance polyethylene (HPPE), Kevlar, fiberglass, stainless steel fibers, and specialized synthetic blends. These materials are woven together using sophisticated techniques to create a barrier that can withstand different levels of cutting hazards while maintaining flexibility and comfort for the wearer.
The primary purpose of anti-cutting sleeves is to protect workers in industries where sharp objects, tools, or materials pose significant risks. These include:
- Metal fabrication and machining
- Glass manufacturing and handling
- Paper processing
- Food processing (especially meat cutting)
- Automotive manufacturing
- Construction
- Recycling operations
- Woodworking
Qingdao Snell Protective Products Co., Ltd. has emerged as an industry leader in developing anti-cutting sleeves that combine superior protection with ergonomic design. Their sleeves feature innovative fiber blends that maximize cut resistance while maintaining breathability and comfort during extended wear.
How to Choose the Best Anti-Cutting Sleeves for Your Business?
Selecting the right anti-cutting sleeves for your specific business needs requires careful consideration of several factors. Making an informed decision will ensure your workers receive appropriate protection while maximizing your investment.
Cut Resistance Levels
The most critical factor in selecting anti-cutting sleeves is understanding the appropriate cut resistance level required for your specific application. Cut resistance is typically classified according to standardized testing methods:
ANSI/ISEA 105 Standard (American):
- A1: Light cut hazards
- A2-A3: Medium cut hazards
- A4-A5: High cut hazards
- A6-A9: Extreme cut hazards
EN 388 Standard (European):
- Level A: Light cut hazards
- Level B-C: Medium cut hazards
- Level D-E: High cut hazards
- Level F: Extreme cut hazards
Match the cut resistance level to your specific workplace hazards. Over-specifying may lead to unnecessary costs, while under-specifying could compromise safety.
Material Considerations
Different materials offer varying levels of protection, comfort, and durability:
- HPPE (High-Performance Polyethylene): Lightweight and offers excellent cut resistance without sacrificing comfort.
- Kevlar: Exceptional cut and heat resistance, though it may degrade with UV exposure.
- Composite Materials: Blends that incorporate steel, fiberglass, or other synthetic fibers to enhance protection while maintaining flexibility.
- HPPE/Spandex Blends: Provide excellent cut resistance with enhanced flexibility and comfort for all-day wear.
Length and Coverage
Anti-cutting sleeves come in various lengths:
- Wrist-to-elbow
- Full arm (wrist-to-upper arm)
- Bicep sleeves
- Sleeves with thumb holes for added wrist protection
Consider the specific areas requiring protection in your workplace and choose accordingly.
Additional Features
Look for sleeves with:
- Breathability features for comfort in hot environments
- Antimicrobial treatments for food processing applications
- Color-coding for size identification or departmental assignment
- UV protection for outdoor work
- Washability and maintenance requirements
- Temperature resistance for hot or cold environments
Testing and Certification
Always verify that the anti-cutting sleeves you’re considering have been tested and certified to relevant standards:
- ANSI/ISEA 105 (American standard)
- EN 388 (European standard)
- Cut Protection Performance Test (CPPT)
- Tomodynamometer (TDM) test results
By thoroughly evaluating these factors, you can select anti-cutting sleeves that provide the optimal balance of protection, comfort, and cost-effectiveness for your specific business needs.
Where to Buy Anti-Cutting Sleeves Wholesale?
When sourcing anti-cutting sleeves in bulk for your business, you have several options to consider, each with unique advantages and potential drawbacks.
Direct Manufacturers
Purchasing directly from manufacturers like Qingdao Snell Protective Products offers several advantages:
Pros:
- Typically lower per-unit pricing
- Ability to customize products to your specifications
- Direct communication with production teams
- Better quality assurance and consistent standards
- Potential for faster resolution of quality issues
Cons:
- Usually higher minimum order quantities (MOQs)
- Longer lead times, especially for international manufacturers
- May require more complex import procedures
Industrial Safety Distributors
Large industrial safety distributors and wholesalers serve as intermediaries between manufacturers and businesses:
Pros:
- Lower minimum order quantities than direct manufacturers
- Ability to bundle different safety products in one order
- Often provide technical support and product expertise
- Faster delivery times for standard products
- May offer credit terms for established business customers
Cons:
- Higher per-unit costs compared to direct manufacturer purchases
- Limited customization options
- Additional markup in the supply chain
Online B2B Marketplaces
Platforms like Alibaba, Global Sources, and industry-specific B2B marketplaces have become increasingly popular:
Pros:
- Access to numerous suppliers in one place
- Easy price comparison
- Supplier verification services on some platforms
- More flexible MOQ requirements
- Secure payment options
Cons:
- Quality can be inconsistent
- Communication challenges with some suppliers
- Longer shipping times for international suppliers
- Potential counterfeiting risks
Trade Shows and Industry Exhibitions
Safety equipment trade shows remain an excellent place to establish direct relationships with manufacturers:
Pros:
- Hands-on product evaluation
- Face-to-face relationship building
- Opportunity to negotiate terms in person
- Discovery of innovative new products
- Direct comparison of multiple suppliers
Cons:
- Higher acquisition costs (travel, accommodation)
- Limited to scheduled events
- May not be feasible for immediate purchasing needs
When seeking quality anti-cutting sleeves at competitive wholesale prices, working directly with established manufacturers like Qingdao Snell often provides the best value, especially for larger orders where customization is important. Their commitment to quality control, certified production processes, and material expertise ensures you’re getting genuinely protective equipment rather than inferior alternatives that might compromise worker safety.
Anti-Cutting Sleeves Manufacturers in China
China has emerged as a global leader in manufacturing anti-cutting sleeves, offering competitive pricing without compromising on quality and innovation. The country’s manufacturing ecosystem provides numerous advantages for businesses seeking reliable wholesale suppliers.
Top Chinese Manufacturers Overview
Among the leading manufacturers in China’s anti-cutting protective gear industry, Qingdao Snell Protective Products Co., Ltd. stands out for its specialized focus on high-performance safety equipment. Established in 2024, the company has quickly built a reputation for excellence through its state-of-the-art production facilities in Gaomi and Nantong.
With six dedicated production lines and ISO9001 and CE certifications, Qingdao Snell exemplifies the quality standards that top-tier Chinese manufacturers bring to the global market. Their engineering team continually develops innovative materials and manufacturing techniques that enhance cut resistance while maintaining comfort and flexibility.
Manufacturing Capabilities and Infrastructure
Chinese manufacturers offer several distinct advantages in anti-cutting sleeve production:
- Advanced Material Innovation: Leading factories like Qingdao Snell have developed proprietary fiber blends that maximize cut resistance while maintaining breathability. Their research teams continuously test new material combinations to improve performance.
- Vertical Integration: Many Chinese manufacturers control multiple stages of production, from raw material processing to final packaging, allowing for better quality control and cost efficiency.
- Scale and Capacity: With multiple high-volume production lines, Chinese manufacturers can fulfill large orders efficiently while maintaining consistent quality. Qingdao Snell’s six production lines enable them to meet substantial wholesale demands with shorter lead times.
- Customization Capabilities: Chinese manufacturers excel at adapting designs to meet specific client requirements, including custom sizing, specialized materials for specific industries, and branding options.
- Quality Control Systems: Reputable manufacturers implement rigorous quality assurance protocols, including:
- Raw material testing
- In-process inspections
- Final product validation
- Regular third-party testing to verify compliance with international standards
Cost Advantages of Chinese Manufacturing
Several factors contribute to China’s competitive pricing for anti-cutting sleeves:
- Economies of scale due to high production volumes
- Lower labor costs compared to Western markets
- Well-established supply chains for specialized materials
- Efficient logistics infrastructure
- Government investments in manufacturing technology
For example, Qingdao Snell offers factory-direct pricing that eliminates middleman markups, providing exceptional value without compromising on quality or safety standards. Their minimum order quantities typically range from 3,000 to 20,000 pieces, making them accessible for medium to large businesses seeking wholesale supplies.
Challenges and Considerations
When sourcing from Chinese manufacturers, businesses should be aware of:
- Lead Times: Production and shipping typically require 2-4 weeks, sometimes longer during peak seasons
- Communication: Working across time zones and potential language barriers
- Quality Verification: The importance of working with certified manufacturers
- Intellectual Property: Ensuring proper protection for custom designs
- Regulatory Compliance: Verifying that products meet destination country standards
By partnering with established manufacturers like Qingdao Snell that prioritize quality control, international certification, and clear communication, businesses can effectively mitigate these challenges while capitalizing on the significant advantages of Chinese manufacturing.
What to Look for in Reliable Anti-Cutting Sleeves?
When investing in wholesale anti-cutting sleeves, understanding the key quality indicators ensures you’re providing genuine protection for your workforce. Here’s what discerning buyers should evaluate before making a purchase decision:
Material Quality and Construction
The foundation of any effective anti-cutting sleeve lies in its materials and construction techniques:
Core Protective Materials:
- High-performance polyethylene (HPPE) fibers
- Para-aramid fibers (like Kevlar or Twaron)
- Steel or glass fiber reinforcement
- Engineered composite blends
Premium sleeves often feature engineered composite materials that combine multiple fiber types in precise ratios. For instance, Qingdao Snell’s advanced sleeves incorporate their proprietary blend of HPPE with reinforcing fibers in a specialized weave pattern that maximizes cut resistance while maintaining flexibility.
Construction Techniques:
- Seamless knitting for comfort and durability
- Reinforced stitching at high-stress points
- Double-layered protection in critical areas
- Specialized weave patterns that enhance cut resistance
Material Weight and Thickness:
Evaluate the balance between protection and comfort. Higher cut resistance typically requires denser materials, but innovative manufacturing can minimize bulk while maintaining protection.
Performance Testing and Certification
Never rely solely on manufacturer claims – verify independent testing results:
Standardized Testing Methods:
- ANSI/ISEA 105-2016 cut resistance testing (American)
- EN 388:2016 mechanical resistance testing (European)
- ISO 13997 TDM cut resistance testing (International)
Certification Verification:
Request test certificates that demonstrate compliance with relevant standards. Legitimate manufacturers like Qingdao Snell readily provide documentation of their ISO9001 quality management system certification and CE marking compliance.
Performance Consistency:
Quality manufacturers conduct batch testing to ensure every production run meets specifications. Ask about quality control protocols and batch-to-batch consistency measures.
Functional Features for Specific Applications
Different work environments require specialized features:
Food Processing Requirements:
- Metal detectability for food safety
- Antimicrobial treatments
- Hygienic design for easy cleaning
- Compliance with food contact regulations
Heavy Industry Applications:
- Enhanced puncture resistance
- Abrasion resistance for rough surfaces
- Heat resistance for work near thermal hazards
- Chemical resistance when needed
Comfort and Usability Features:
- Moisture-wicking properties for extended wear
- Breathable design to reduce heat buildup
- Ergonomic fit to prevent fatigue
- Extended coverage options for maximum protection
Manufacturing Transparency and Quality Control
Reputable manufacturers willingly share information about their production processes:
Production Environment:
- Clean, organized manufacturing facilities
- Worker training and skill certification
- Modern machinery and equipment
- Environmental and labor compliance
Quality Control Processes:
- Incoming material verification
- In-process inspection points
- Final product testing
- Traceability systems for problem resolution
By thoroughly evaluating these factors, you can confidently select anti-cutting sleeves that provide genuine protection rather than merely the appearance of safety. Remember that the consequences of inferior protection can be severe—prioritize quality and performance from established manufacturers with proven track records in safety equipment production.
MOQ Considerations When Ordering Anti-Cutting Sleeves
Understanding minimum order quantity (MOQ) requirements is crucial when planning your wholesale anti-cutting sleeve purchase. MOQs vary significantly among suppliers and can impact both your budget and inventory management strategy.
Typical MOQ Ranges for Anti-Cutting Sleeves
MOQs for anti-cutting sleeves typically fall into several categories based on supplier type:
Direct Manufacturers:
- Large manufacturers: 5,000-50,000+ units
- Mid-sized specialists: 1,000-5,000 units
- Small boutique producers: 500-1,000 units
Distributors and Wholesalers:
- Large industrial distributors: 500-1,000 units
- Specialized safety equipment wholesalers: 100-500 units
- Regional distributors: 50-200 units
Online B2B Platforms:
- Factory-direct suppliers: 1,000-10,000 units
- Trading companies: 300-1,000 units
- Specialized exporters: 200-500 units
Qingdao Snell Protective Products Co., Ltd., as a factory-direct manufacturer, maintains MOQs that typically range from 3,000 to 20,000 pieces depending on the specific product type, customization requirements, and material specifications. While this might seem substantial, their MOQ structure is designed to balance production efficiency with customer needs.
Factors Affecting MOQ Requirements
Several variables influence a supplier’s MOQ policy:
- Product Customization Level:
- Standard products generally have lower MOQs
- Custom colors may increase MOQs by 20-50%
- Custom designs, materials or features can double or triple MOQs
- Proprietary technologies may further elevate minimum quantities
- Material Considerations:
- Specialized cut-resistant materials often come with higher supplier MOQs
- Premium materials like advanced HPPE blends typically require larger orders
- Standard materials may allow for more flexible ordering quantities
- Production Economics:
- Machine setup costs must be amortized across an order
- Material purchasing minimums from upstream suppliers
- Quality control batch testing requirements
- Labor efficiency considerations in production scheduling
Strategies for Managing MOQ Challenges
When facing high MOQs that exceed your immediate needs, consider these approaches:
- Phased Delivery Arrangements:
Order the full MOQ but negotiate scheduled deliveries over time to manage cash flow and storage requirements. Many manufacturers like Qingdao Snell offer flexible delivery schedules for larger orders. - Collaborative Purchasing:
Partner with other businesses in your industry to place a combined order that meets MOQ requirements, then divide the products among participants. - Product Variety Within MOQs:
Negotiate to split the MOQ across different sizes, styles, or colors while maintaining the total volume commitment. For example, an order of 5,000 sleeves might be divided into multiple size categories. - MOQ Negotiation Strategies:
- Commit to repeat orders over time
- Offer deposits or favorable payment terms
- Propose a trial order with commitment to larger follow-up orders
- Leverage seasonal manufacturing downtime for smaller runs
Cost Implications of MOQ Decisions
Understanding the relationship between MOQ and unit pricing helps optimize purchasing decisions:
Order Quantity | Typical Price Discount | Additional Considerations |
---|---|---|
MOQ-1,000 units | Base price | Standard lead times, limited negotiating power |
1,001-5,000 units | 5-10% discount | Improved delivery priority, some customization options |
5,001-10,000 units | 10-15% discount | Enhanced customization options, dedicated quality control |
10,001-20,000 units | 15-20% discount | Priority production scheduling, potential dedicated service team |
20,001+ units | 20%+ discount | Maximum leverage on specifications, premium service levels |
For businesses with fluctuating needs, balancing inventory carrying costs against volume discounts becomes crucial in MOQ decisions. Qingdao Snell works with clients to find the optimal balance point where order volumes provide meaningful cost advantages without creating excessive inventory burden.
How to Customize Anti-Cutting Sleeves with Your Logo and Branding?
Customizing anti-cutting sleeves with your company’s branding creates multiple benefits beyond basic identification. It enhances brand visibility, builds professional image, and can even improve compliance with safety protocols by creating ownership of personal protective equipment among employees.
Available Customization Options
Modern manufacturing techniques offer numerous ways to personalize anti-cutting sleeves:
Logo Application Methods:
- Silkscreen Printing: Most common for simple logos with 1-3 colors. Offers durability and cost-effectiveness for large orders.
- Heat Transfer: Provides excellent detail reproduction and vibrant colors. Ideal for complex logos or photographic elements.
- Embroidery: Creates a premium appearance but may affect cut resistance if not properly engineered. Usually limited to designated safe zones on the sleeve.
- Woven Labels: Sewn onto specific areas of the sleeve for a professional, durable identification method.
- Molded Rubber Patches: High-durability option for harsh environments where printed logos might wear away.
Color Customization:
- Base material colors (subject to minimum quantities)
- Color-coded bands or borders for size or department identification
- Safety-enhancing high-visibility elements
Structural Customization:
- Length modifications
- Attachment points (thumb holes, elastic bands)
- Reinforced areas based on specific work requirements
- Special features for industry-specific needs
Design Considerations for Effective Branding
When designing custom anti-cutting sleeves, balance branding goals with safety functionality:
- Placement Optimization:
- Position logos in areas with minimal flexing or abrasion
- Consider visibility when the sleeve is worn (outer arm areas typically offer best visibility)
- Ensure branding doesn’t interfere with functional elements
- Design Elements:
- Use contrasting colors that stand out against the base material
- Consider simplified versions of complex logos for better reproduction
- Include relevant safety information alongside branding
- Incorporate QR codes for quick access to usage instructions or safety information
- Regulatory Compliance:
- Ensure customization doesn’t obscure mandatory safety markings
- Maintain visibility of cut resistance levels and certification information
- Consider including space for inspection dates or employee assignment information
The Customization Process With Manufacturers
Understanding the typical workflow helps ensure successful customization projects:
- Initial Consultation and Design Submission:
- Provide vector file formats (AI, EPS, PDF) for best results
- Specify exact Pantone colors for accurate matching
- Clarify size requirements and placement preferences
- Sample Approval Process:
- Digital mockups for initial concept approval
- Physical samples for final verification before full production
- Evaluation of branding durability through wash testing
- Production Considerations:
- Extended lead times for customized orders (typically 3-6 weeks)
- Higher MOQs than standard products (Qingdao Snell typically requires 5,000-20,000 units for fully customized sleeves)
- Setup fees for custom tooling or screens
Qingdao Snell Protective Products Co., Ltd. offers comprehensive customization services with their in-house design team that specializes in optimizing branding elements for safety equipment. Their experience ensures that customization enhances rather than compromises the protective qualities of the sleeves.
Cost Implications of Customization
Customization Type | Typical Cost Impact | Minimum Order Requirements |
---|---|---|
Single-color logo printing | +$0.20-0.50 per unit | 3,000-5,000 units |
Multi-color logo printing | +$0.50-1.20 per unit | 5,000-10,000 units |
Embroidered logos | +$0.80-1.50 per unit | 5,000-10,000 units |
Custom color material | +$0.30-0.70 per unit | 10,000+ units |
Structural modifications | +$1.00-3.00 per unit | 10,000-20,000 units |
Combination customization | Variable based on specifications | 10,000-20,000 units |
These cost differentials should be evaluated against the marketing value, improved compliance rates, and reduced loss through clearer ownership identification that customized PPE provides.
What Are the Most Durable Materials for Anti-Cutting Sleeves?
The durability and performance of anti-cutting sleeves directly correlate with their constituent materials. Understanding the properties of these materials helps procurement specialists make informed decisions based on specific workplace hazards and usage conditions.
High-Performance Cut-Resistant Materials
Modern anti-cutting sleeves leverage several advanced materials, each with distinct properties:
1. High-Performance Polyethylene (HPPE)
HPPE has revolutionized cut-resistant apparel with its exceptional strength-to-weight ratio:
Advantages:
- Up to 15 times stronger than steel on a weight-for-weight basis
- Excellent cut resistance without bulk
- Lightweight and comfortable for all-day wear
- Maintains flexibility even in complex weaves
- Highly resistant to moisture, chemicals, and UV degradation
- Washable and maintains performance after multiple cleaning cycles
Limitations:
- Moderate heat resistance (begins to degrade above 170°F/77°C)
- Higher cost than basic materials
- May require blending with other fibers for optimal performance
Applications:
HPPE excels in environments requiring precision handling where flexibility and tactile sensitivity are crucial, such as electronics assembly, automotive manufacturing, and glass handling.
2. Para-Aramid Fibers (Kevlar® and Similar Materials)
These synthetic fibers offer a balance of cut and heat resistance:
Advantages:
- Outstanding cut resistance
- Excellent heat resistance (can withstand up to 800°F/427°C brief exposure)
- Good abrasion resistance
- Maintains integrity under high stress
- Non-conductive properties for electrical work
Limitations:
- Degrades with prolonged UV exposure
- Can absorb moisture, affecting comfort during extended wear
- More challenging to clean effectively
- Stiffer than some alternative materials
Applications:
Para-aramid fibers are ideal for high-heat environments like metal stamping, foundry work, and automotive manufacturing where both cut and thermal hazards exist.
3. Composite and Engineered Materials
The latest innovation in cut protection comes from engineered composite materials:
Advantages:
- Customizable performance characteristics
- Can combine benefits of multiple material types
- Optimized for specific hazard profiles
- Often provides superior cut resistance with less material
- Better comfort-to-protection ratio
Limitations:
- Higher manufacturing complexity
- More variable in performance between manufacturers
- Often requires proprietary production techniques
Qingdao Snell has developed several proprietary composite materials that strategically combine HPPE, performance fibers, and specialized reinforcements in patterns designed to maximize protection at critical strike zones while maintaining flexibility elsewhere.
Material Performance Comparison
Material Type | Cut Resistance (ANSI) | Heat Resistance | Comfort Level | Durability | Relative Cost |
---|---|---|---|---|---|
Standard HPPE | A3-A4 | Moderate | Excellent | Very Good | Medium |
High-Grade HPPE | A4-A6 | Moderate | Very Good | Excellent | High |
Para-Aramid | A3-A5 | Excellent | Good | Very Good | High |
HPPE/Steel Composite | A5-A7 | Moderate | Good | Excellent | High |
HPPE/Glass Fiber Composite | A4-A6 | Good | Very Good | Very Good | Medium-High |
Engineered Composites | A6-A9 | Variable | Very Good | Excellent | Premium |
Environmental Durability Factors
Beyond cut resistance, consider these durability aspects when selecting materials:
Chemical Resistance:
Different materials offer varying resistance to common industrial chemicals:
- HPPE: Excellent resistance to most chemicals, solvents, and petroleum products
- Para-aramids: Good resistance to many chemicals but can degrade with exposure to strong acids
- Composites: Vary based on specific formulation
UV and Weather Resistance:
For outdoor applications, material degradation from UV exposure becomes significant:
- HPPE: Excellent UV resistance with minimal degradation
- Para-aramids: Poor UV resistance, requiring covers or treatments for outdoor use
- Treated materials: Special UV-resistant finishes can extend service life
Washability and Maintenance:
The ability to clean and maintain protective properties significantly affects lifetime cost:
- HPPE: Maintains performance through multiple wash cycles
- Para-aramids: May require special cleaning procedures
- Composite materials: Vary by specific formulation
For environments with multiple hazard types, Snell’s specialized product lines offer engineered solutions that address specific industry challenges while maintaining excellent durability characteristics.
How to Ensure Quality Control for Anti-Cutting Sleeves?
Quality assurance is critical when sourcing anti-cutting sleeves, as substandard products may fail to provide adequate protection when needed most. Implementing comprehensive quality control measures safeguards both your investment and your workers’ safety.
Establishing Effective Supplier Verification
Before placing wholesale orders, thoroughly vet potential manufacturers:
Documentation Review:
- Request and verify relevant certifications (ISO 9001, CE marking)
- Evaluate test reports from accredited laboratories
- Review product specifications against industry standards
- Assess compliance with region-specific regulations
Manufacturing Facility Assessment:
- Request virtual or in-person factory tours
- Verify production capabilities match claimed capacity
- Evaluate cleanliness, organization, and safety protocols
- Assess worker training and quality control processes
Sample Evaluation:
- Request production samples before bulk ordering
- Conduct independent testing of samples
- Compare multiple suppliers’ products side-by-side
- Evaluate consistency between samples
Qingdao Snell Protective Products Co., Ltd. welcomes client audits and provides comprehensive documentation of their quality management system. Their ISO9001 certification demonstrates their commitment to consistent quality control processes throughout their manufacturing operations.
Key Quality Control Testing Methods
Implement these testing procedures to verify product performance:
Visual Inspection Protocols
Develop a systematic visual inspection process:
- Consistent stitching and seam integrity
- Even material density throughout the product
- Accurate sizing and dimensional consistency
- Proper labeling and traceability information
- Absence of manufacturing defects
Physical Testing Standards
Implement performance testing appropriate to your application:
- Cut resistance verification using standardized test methods
- Abrasion resistance testing
- Tensile strength and flexibility measurements
- Washability and dimensional stability after cleaning
- Environmental exposure testing when applicable
Statistical Quality Control Implementation
Apply statistical methods to ensure consistent quality:
- Acceptance Quality Limit (AQL) sampling plans
- Statistical Process Control (SPC) for critical characteristics
- Trend analysis to identify potential manufacturing drift
- Lot traceability systems for recall management if needed
Establishing a Comprehensive Incoming Quality Control System
Develop standard operating procedures for receiving and inspecting shipments:
Sampling Methodology:
Implement appropriate sampling plans based on order size:
Order Size | Recommended Sample Size | Acceptable Defect Rate |
---|---|---|
<5,000 units | 125 units | <1.0% |
5,000-10,000 units | 200 units | <0.75% |
10,000-20,000 units | 315 units | <0.65% |
>20,000 units | 500 units | <0.5% |
Inspection Process:
- Randomly select samples from different cartons and production batches
- Perform standardized visual inspections
- Conduct performance testing on selected samples
- Document all findings systematically
- Make acceptance decisions based on predetermined criteria
Documentation Requirements:
- Create detailed inspection reports
- Maintain records of test results
- Document any non-conformances
- Track supplier performance metrics over time
Continuous Improvement Through Supplier Relationships
Develop collaborative relationships with key suppliers:
- Share quality performance data regularly
- Conduct periodic supplier audits
- Involve suppliers in problem-solving when issues arise
- Recognize and reward exceptional quality performance
By implementing these quality assurance measures, you can significantly reduce the risk of receiving substandard anti-cutting sleeves. Remember that the cost of quality control is far less than the potential consequences of inadequate protection in hazardous work environments.
Working with established manufacturers like Qingdao Snell provides additional assurance through their established quality management systems and willingness to collaborate on continuous improvement initiatives.
Compliance and Certifications Required for Anti-Cutting Sleeves in Different Markets
Navigating the complex landscape of international safety standards and certifications is essential when sourcing anti-cutting sleeves for global operations. These requirements vary by region and industry, making compliance a critical consideration in procurement decisions.
Key International Standards for Cut Resistance
Several foundational standards govern the testing and classification of cut-resistant protective equipment:
ANSI/ISEA 105 (American National Standard)
The American National Standards Institute standard provides a comprehensive framework for hand and arm protection:
- Cut Resistance Classification: Uses an A1-A9 scale, with A9 representing the highest protection
- Testing Methodology: Employs the ASTM F2992-15 test method (CPPT or TDM test)
- Force Measurement: Measures the force required to cut through material with a standardized blade
- Required Documentation: Test reports from accredited laboratories
EN 388 (European Standard)
The European standard for protective gloves against mechanical risks includes specific provisions for cut resistance:
- Classification System: Uses a scale of A-F (with F being highest) under the 2016 revision
- Testing Methodology: ISO 13997 TDM test method
- Comprehensive Protection: Includes ratings for abrasion, cut, tear, and puncture resistance
- Marking Requirements: Products must display the standard’s pictogram with performance levels
ISO 13997 (International Standard)
This international standard specifically addresses cut resistance measurement:
- Force Measurement: Quantifies the force (in Newtons) required to cut through material with a single stroke
- Universal Application: Used as a reference test method across multiple regional standards
- Scientific Approach: Controls variables like blade sharpness and material consistency
Regional Compliance Requirements
Different markets have specific regulatory frameworks governing PPE:
European Union
The EU requires:
- CE Marking: Mandatory for all PPE sold within the European Economic Area
- EU Type-Examination: Third-party verification by a notified body
- Declaration of Conformity: Manufacturer’s statement of compliance with EU regulations
- Technical File: Comprehensive documentation of design, testing, and production
United States
US requirements include:
- OSHA Compliance: Must meet Occupational Safety and Health Administration requirements
- ANSI Conformity: Adherence to relevant American National Standards Institute standards
- Labeling Requirements: Clear indication of performance levels and limitations
- Hazard Assessment: Documentation supporting appropriateness for specific workplace hazards
Asia-Pacific Markets
Requirements vary by country:
- Japan: Compliance with JIS T8116 standard
- Australia/New Zealand: Conformity with AS/NZS 2161 standards
- China: CCC certification for certain categories of protective equipment
Industry-Specific Requirements
Beyond regional regulations, specific industries impose additional requirements:
Food Processing
- FDA Compliance: Materials must be suitable for food contact
- HACCP Compatibility: Design must support hazard analysis critical control point protocols
- Detectability Features: Metal detection capabilities in some environments
- Sanitization Standards: Must withstand food-safe cleaning procedures
Oil and Gas
- Flame Resistance: Often requires additional FR ratings
- Chemical Compatibility: Resistance to petroleum products and processing chemicals
- Anti-Static Properties: Prevention of spark hazards in volatile environments
Electronics Manufacturing
- ESD Standards: Electrostatic discharge protection requirements
- Cleanroom Compatibility: Particulate shedding limitations
- Chemical Resistance: Protection against solvents and cleaning agents
Qingdao Snell Protective Products Co., Ltd. maintains comprehensive certification for their anti-cutting sleeves across major markets. Their products undergo regular testing to ensure continued compliance with evolving standards, and their technical team stays abreast of regulatory changes to provide customers with up-to-date compliance information.
Documentation and Traceability Requirements
Proper documentation is essential for compliance verification:
Required Documentation:
- Test Reports: From accredited laboratories demonstrating performance levels
- Certificates of Conformity: Manufacturer’s declaration of standard compliance
- Technical Data Sheets: Detailed specifications and performance characteristics
- User Instructions: Required information on proper use, limitations, and maintenance
Traceability Elements:
- Batch Coding: Identification of production lots
- Manufacturing Date: Clear indication of production timing
- Supply Chain Documentation: Records of material sourcing and production processes
By thoroughly understanding these compliance requirements, procurement professionals can ensure their anti-cutting sleeve purchases meet all necessary legal and safety standards for their specific applications and markets.
Latest Innovations in Anti-Cutting Sleeves Manufacturing for Industrial Use
The field of protective equipment is experiencing rapid technological advancement, with anti-cutting sleeves benefiting from numerous innovations that enhance both protection and user experience. Understanding these developments helps procurement professionals make forward-looking decisions when sourcing wholesale supplies.
Advanced Material Science Breakthroughs
Recent years have seen remarkable progress in the materials used for cut protection:
Nano-Enhanced Fibers
Nanotechnology is revolutionizing cut-resistant materials:
- Carbon Nanotube Reinforcement: Microscopic carbon structures integrated into fibers increase strength while maintaining flexibility
- Nano-Ceramic Particles: Embedded ceramic nanoparticles enhance cut resistance without adding significant weight
- Molecular Orientation: Advanced processing techniques align molecules for maximum strength along critical axes
- Surface Treatments: Nano-scale coatings improve durability and performance characteristics
Bio-Based Sustainable Materials
Environmental considerations are driving innovation in sustainable cut-resistant materials:
- Plant-Based Fibers: High-performance materials derived from renewable sources like eucalyptus, bamboo, or agricultural waste
- Biodegradable Composites: Materials engineered to maintain performance while reducing environmental impact at end-of-life
- Recycled Content Integration: Incorporation of recycled materials without compromising protection levels
Qingdao Snell has been at the forefront of sustainable material development, with their eco-conscious product line incorporating recycled HPPE fibers and bio-based components that maintain ISO and CE certification standards while reducing environmental footprint.
Manufacturing Process Innovations
Advanced production techniques are improving consistency and performance:
Computer-Optimized Knitting Technologies
Precision manufacturing has transformed production capabilities:
- Variable Density Knitting: Strategic reinforcement in high-risk areas while maintaining flexibility elsewhere
- 3D Knitting Technology: Seamless construction that eliminates weak points and enhances comfort
- Digital Pattern Optimization: Computer modeling to maximize protection from typical cutting angles
- Multi-Layer Integration: Unified construction of different protective layers without bulky seams
Smart Manufacturing and Quality Control
Industry 4.0 technologies are enhancing production precision:
- Inline Testing Systems: Continuous monitoring during production rather than batch sampling
- Computer Vision Inspection: Automated detection of manufacturing inconsistencies
- Digital Twin Modeling: Virtual prototyping to predict performance before physical production
- Blockchain Traceability: Complete material and production history for quality assurance
Performance-Enhancing Features
Beyond basic cut protection, modern sleeves incorporate additional functional elements:
Integrated Sensing Technologies
Smart protective equipment is beginning to enter the market:
- Impact Sensors: Embedded electronics that record significant impacts
- Wear Indicators: Visual cues that show when protection has been compromised
- RFID Tracking: Inventory management and compliance verification capabilities
- Connected PPE: Data collection for safety program optimization
Ergonomic Advancements
User comfort and performance are driving design innovations:
- Anatomically Mapped Protection: Varying protection levels based on vulnerability mapping
- Compression Zones: Strategic support for muscles during repetitive tasks
- Thermal Regulation: Advanced materials that manage heat and moisture
- Antimicrobial Properties: Treatments that reduce odor and bacterial growth
Future Directions in Anti-Cutting Sleeve Technology
The industry continues to evolve with several emerging trends:
Customization Through Digital Manufacturing
On-demand production is becoming increasingly viable:
- 3D-Printed Components: Additively manufactured reinforcements tailored to specific tasks
- Digital Knitting Programming: Rapid pattern changes without retooling
- Mass Customization: Economical personalization for individual worker requirements
- Just-in-Time Manufacturing: Reduced inventory requirements through responsive production
Multi-Hazard Protection Integration
Unified protection against multiple workplace hazards:
- Cut and Impact Protection: Combined solutions for comprehensive arm safety
- Thermal Management with Cut Resistance: Protection from both cutting and temperature extremes
- Chemical Resistance Integration: Barriers that protect against both mechanical and chemical hazards
- Anti-Vibration Features: Reduction of vibration transfer while maintaining cut protection
These innovations represent significant advancements in worker protection, with leading manufacturers like Qingdao Snell continuously incorporating new technologies into their product development. Their research and development team collaborates with material scientists and industrial safety experts to create next-generation protective solutions that address emerging workplace hazards.
By staying informed about these technological developments, safety managers and procurement specialists can make forward-looking decisions that not only address current safety needs but also anticipate future requirements.
How to Find a Reliable OEM Work Gloves Factory in China
Identifying and partnering with a dependable OEM work gloves factory in China requires a systematic approach. The right manufacturing partner can provide significant competitive advantages through cost efficiency, quality control, and customization capabilities.
Effective Search Strategies for Identifying Potential Suppliers
Begin your supplier search with these proven methods:
B2B Platforms and Trade Directories
Online resources provide an initial supplier pool:
- Alibaba and Global Sources: Filter suppliers by certification, years in business, and product categories
- Made-in-China and HKTDC: Specialized directories with verified supplier information
- Industry-Specific Platforms: Safety equipment associations and directories
- Chinese Manufacturing Directories: Regional manufacturing databases
Trade Shows and Industry Exhibitions
Despite digital alternatives, in-person evaluation remains valuable:
- A+A Safety Exhibition (Germany): Premier international safety equipment show
- National Safety Council Expo (USA): Major North American safety equipment exhibition
- China International Occupational Safety & Health Exhibition: Largest Asian safety show
- Regional Safety Equipment Exhibitions: Smaller shows focused on specific markets
Industry Referrals and Networks
Leverage existing relationships for qualified recommendations:
- Current Suppliers: Often have connections in complementary product categories
- Industry Associations: Member directories and networking opportunities
- Customs Data Analysis: Identifying who your competitors source from
- Commercial Services: Embassy commercial services and trade promotion organizations
Comprehensive Supplier Evaluation Criteria
Once you’ve identified potential partners, assess them using these criteria:
Manufacturing Capabilities Assessment
Evaluate technical capabilities and production capacity:
- Factory Scale and Equipment: Modern machinery indicates investment in quality
- Production Capacity: Ability to handle your volume requirements
- Technical Expertise: Engineering capabilities for product development
- Quality Control Systems: In-process inspection and testing procedures
- Vertical Integration: Control over supply chain components
Certification and Compliance Verification
Confirm legitimate quality and safety credentials:
- Business Licenses: Proper registration and operating permits
- Quality Management Systems: ISO 9001 certification
- Product Certifications: CE, ANSI/ISEA compliance documentation
- Social Compliance: BSCI, WRAP, or similar social responsibility audits
- Environmental Standards: ISO 14001 or other environmental management systems
Business Stability Indicators
Assess long-term partnership viability:
- Years in Operation: Track record of stability and growth
- Client Portfolio: Diversity of customers and markets served
- Financial Health: Where possible, evaluate financial stability
- Management Experience: Leadership with industry expertise
- Export History: Experience serving your specific market
Due Diligence and Verification Processes
Thorough validation helps avoid costly mistakes:
Factory Audit Procedures
On-site or third-party verification is essential:
- Physical Inspection: Direct observation of facilities and operations
- Production Line Assessment: Evaluation of workflow and efficiency
- Quality Control Observation: Review of testing and inspection processes
- Worker Conditions: Verification of labor practices and safety protocols
- Sample Room Capabilities: Ability to develop and refine prototypes
Background Investigation Best Practices
Verify claims through independent means:
- Reference Checks: Contact existing clients for feedback
- Document Verification: Authenticate certifications through issuing bodies
- Online Reputation Analysis: Research company history and performance
- Credit Reports: Where available, review financial stability
- Legal History: Check for litigation or regulatory issues
Building Effective Long-Term Partnerships
After selecting a supplier, focus on relationship development:
Communication Protocols
Establish clear channels for ongoing collaboration:
- Regular Meeting Schedule: Structured communication cadence
- Designated Points of Contact: Clear responsibility assignment
- Language Considerations: Bilingual staff or translation services
- Time Zone Management: Accommodating international time differences
- Documentation Standards: Specifications, quality expectations, and timelines
Quality Assurance Frameworks
Implement systems to maintain consistent quality:
- Detailed Product Specifications: Clear documentation of requirements
- Sample Approval Process: Systematic review and approval procedures
- In-Process Inspection Plans: Key checkpoints during production
- Pre-Shipment Inspection Protocols: Final verification before dispatch
- Continuous Improvement Mechanisms: Process for addressing issues
Qingdao Snell Protective Products exemplifies the qualities of a reliable OEM partner in China. With over 10 years of industry expertise, ISO 9001 and CE certifications, and a focus on direct manufacturing relationships, they offer both the technical capabilities and business stability needed for successful long-term sourcing partnerships. Their minimum order quantities of 3,000-20,000 pieces are structured to balance production efficiency with customer requirements, making them an excellent option for medium to large-volume buyers seeking quality anti-cutting sleeves.
FAQ: Anti-Cutting Sleeves Wholesale
What are the minimum order quantities for wholesale anti-cutting sleeves?
Minimum order quantities (MOQs) vary by manufacturer and product type. For standard models, MOQs typically range from 500-1,000 pieces with distributors, while direct manufacturers like Qingdao Snell generally require 3,000-20,000 pieces. Custom designs, colors, or materials usually have higher MOQs, often starting at 5,000 pieces. Volume discounts typically begin at quantities of 5,000+ and increase substantially at 10,000+ units.
How do I verify the cut resistance ratings of wholesale anti-cutting sleeves?
Verify cut resistance by checking certification documentation from accredited testing laboratories. Legitimate manufacturers provide test reports confirming compliance with standards like ANSI/ISEA 105 (A1-A9 scale) or EN 388 (A-F scale). For additional assurance, you can send random samples from received shipments to independent testing facilities for verification. Always ensure test reports are recent (within 1-2 years) and match the exact product specifications you’re purchasing.
What is the typical price range for wholesale anti-cutting sleeves?
Wholesale pricing varies significantly based on cut resistance level, materials, and order volume:
Cut Resistance Level | Material Type | Price Range (per unit) |
---|---|---|
Basic (A1-A2) | Standard fibers | 1.50−1.50-1.50−3.00 |
Medium (A3-A4) | HPPE blend | 2.50−2.50-2.50−5.00 |
High (A5-A6) | Advanced composites | 4.00−4.00-4.00−8.00 |
Ultra (A7-A9) | Specialized composites | 7.00−7.00-7.00−15.00 |
Customization adds 0.50−0.50-0.50−3.00 per unit depending on complexity. Direct factory pricing from manufacturers like Qingdao Snell is typically 20-40% lower than distributor pricing due to eliminated middleman margins.
How long do anti-cutting sleeves typically last in industrial use?
Durability varies by material, usage intensity, and maintenance practices. Under normal industrial conditions with proper care, high-quality anti-cutting sleeves typically last:
- Light duty: 6-12 months
- Medium duty: 3-6 months
- Heavy duty: 1-3 months
- Extreme conditions: May require weekly replacement
Extending lifespan requires proper cleaning according to manufacturer guidelines, regular inspection for damage, and rotation between multiple pairs when possible. Premium materials from established manufacturers generally offer 30-50% longer service life than budget alternatives.
Can anti-cutting sleeves be customized with company logos and colors?
Yes, most manufacturers offer customization options. Logo application methods include silkscreen printing (most common), heat transfer, embroidery, and attachable patches. Custom base colors usually require higher minimum orders (10,000+ pieces). For best results, provide vector logo files (AI, EPS) and specific Pantone color codes. Customization typically adds 2-3 weeks to production time and increases costs by 5-15% depending on complexity.
What certifications should I look for when sourcing wholesale anti-cutting sleeves?
Essential certifications include:
- Cut resistance certification to ANSI/ISEA 105 or EN 388 standards
- ISO 9001 quality management system certification for the manufacturer
- CE marking for European markets
- Product-specific test reports from accredited laboratories
- Material safety documentation for food processing applications
Additional industry-specific certifications may be required depending on your application. Always verify certification legitimacy through issuing organizations or third-party verification services.
How should anti-cutting sleeves be maintained to ensure maximum protection?
Proper maintenance includes:
- Washing according to manufacturer guidelines (typically mild detergent, no bleach)
- Air drying away from direct heat sources
- Regular visual inspection for cuts, tears, or significant wear
- Replacement when protection is compromised
- Storage away from sharp objects, chemicals, and UV exposure
- Following manufacturer recommendations for maximum number of wash cycles
Advanced materials like HPPE generally maintain protection levels better through multiple wash cycles compared to traditional materials.
What’s the difference between cut-resistant and cut-proof sleeves?
Cut-resistant sleeves provide varying levels of protection that slow or resist cutting forces but can be compromised under sufficient force or repeated stress. Cut-proof is a misnomer as no material provides absolute protection against all cutting hazards under all conditions. The terms are often used interchangeably in marketing, but technical specifications should always refer to specific cut resistance levels (A1-A9 or A-F) rather than absolute claims of being “cut-proof.” Always select protection level based on specific workplace hazard assessments.
How do I choose between different materials for anti-cutting sleeves?
Material selection should be based on your specific working environment:
- HPPE: Best for precision work requiring flexibility and dexterity
- Para-aramid (Kevlar): Ideal when both cut and heat resistance are needed
- HPPE/steel composites: Maximum cut protection for high-hazard environments
- HPPE/glass fiber: Good balance of protection, comfort and cost
- Engineered composites: Specialized applications with multiple hazard types
Consider additional factors like washability, chemical exposure, temperature conditions, and required dexterity when making your selection.
What are the latest innovations in anti-cutting sleeve technology?
Recent innovations include:
- Nano-enhanced fibers with dramatically improved cut resistance-to-weight ratios
- Sustainable bio-based materials that maintain protection levels
- Variable-density knitting that reinforces high-risk areas while maintaining flexibility
- Antimicrobial treatments for improved hygiene in food processing
- Smart textiles with wear indicators or impact sensors
- Improved ergonomics through anatomical mapping and compression zones
- Multi-hazard protection combining cut, impact, and chemical resistance
Leading manufacturers like Qingdao Snell continuously incorporate these innovations into their product development to provide enhanced protection with improved comfort and durability.